A Guide to SF6 Gas Filling Equipment
SF6 gas filling equipment is a special equipment used to safely and accurately fill sulfur hexafluoride (SF6) gas into high-voltage switchgear, circuit breakers and other power equipment. SF6 gas has excellent insulation properties and arc extinguishing ability, so it is widely used in power systems. Filling equipment usually includes key components such as vacuum pumps, gas metering devices, heating systems, and control systems to ensure that the purity and pressure of the gas during the filling process meet the requirements.
Design and Application of SF6 Gas Filling Equipment
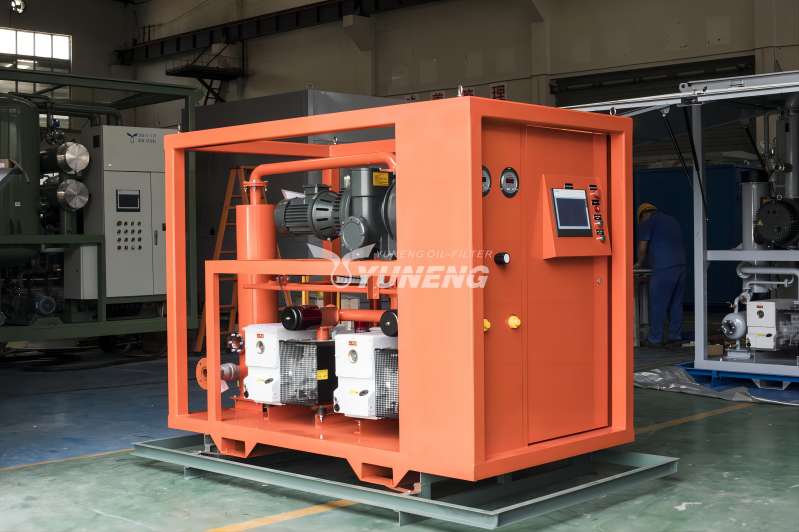
SF6 gas filling equipment is carefully designed to ensure safe handling of SF6 gas. The design highlights include the following aspects:
- System integration: The device should integrate multiple functions such as recovery, charging and discharging, purification, vacuuming, storage and filling to achieve a one-stop SF6 gas management solution.
- Ease of operation: The design should focus on the convenience of operation, and control the series connection or switching of various functions through centralized electric control boxes and ball valves.
- Efficient recovery technology: The freezing liquefaction method is adopted to utilize the synergistic effect of the compressor and refrigerant to efficiently recover SF6 gas and liquefy it for storage.
- Safe charging and discharging mechanism: During the charging and discharging process, vacuum pumps are used to ensure that no impurities or moisture enter, ensuring the stable operation of the equipment.
- Flexible filling capacity: Utilizing the characteristics of the refrigerant, the liquefied SF6 can be directly filled into the cylinder to meet different storage and transportation needs.
Main Application of SF6 Gas Filling Equipment
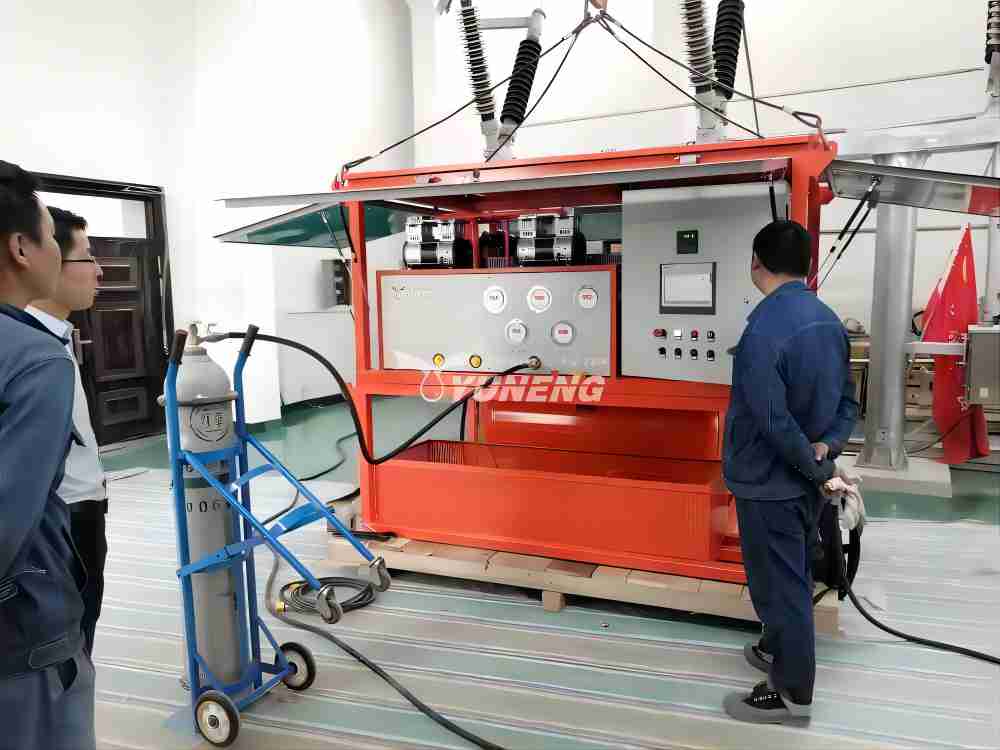
SF6 gas filling devices play an important role in multiple industrial fields. The following are several typical application scenarios of SF6 gas filling devices:
- Application in the power industry: In power systems, SF6 gas is widely used as an insulating medium for high-voltage switchgear and gas-insulated transformers (GIS). SF6 gas filling devices are used in the manufacturing, installation, overhaul and maintenance of these equipment, responsible for filling, recycling and purifying SF6 gas.
- Gas recovery and reuse: Since SF6 is a potent greenhouse gas with extremely high stability in the atmosphere, recycling and reusing SF6 gas is essential for environmental protection. The filling device can be used to collect used SF6 gas, purify and dry it, and then refill it into the equipment, reducing the demand for new gas and environmental impact.
- Application in industrial production: In some industrial production processes, such as metal smelting and electronics manufacturing, SF6 gas is also used as a protective gas or participates in specific chemical reactions. Filling devices are used in these situations to ensure gas supply and quality control.
- Gas management in emergency situations: In emergency situations or accident handling, such as SF6 gas leakage, filling devices can be used to quickly recover leaked gas and reduce environmental pollution and safety risks.
- Environmental monitoring and research: In environmental science research, filling devices can be used to monitor the concentration of SF6 in the atmosphere, evaluate its impact on the environment, or simulate the behavior of SF6 under laboratory conditions.
These application scenarios reflect the multiple values of SF6 gas filling devices in ensuring industrial production safety, improving resource utilization efficiency and protecting the environment.
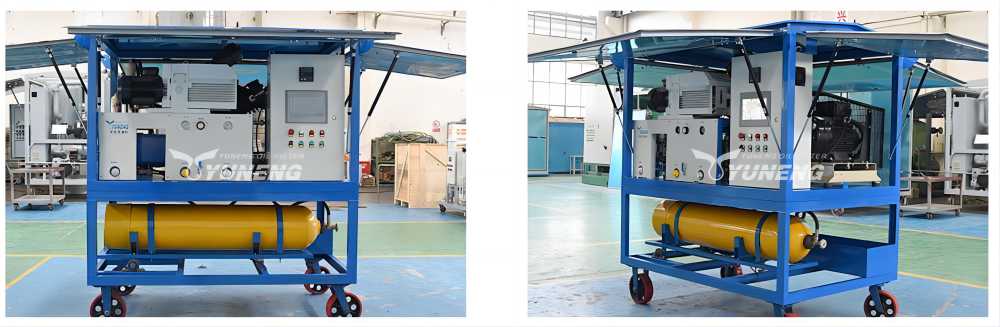
Daily Maintenance Points of SF6 Gas Filling Equipment
Daily maintenance of SF6 gas filling equipment is the key to ensure the normal operation and safety of the equipment. The following are some important maintenance points:
- Equipment inspection: Regularly check all parts of the equipment, including pipes, joints, wiring and fasteners, to ensure that they are intact, not loose or damaged.
- Vacuum pump maintenance: Check whether the vacuum pump oil level is appropriate and ensure that the oil level is within the oil sight glass. When there is a lack of oil, the operation should be stopped and the oil should be replaced or replenished in time.
- Compressor operation: Avoid long-term vacuum operation of the compressor, pay attention to the compressor inlet pressure, and stop recycling in time to protect the compressor.
- Refrigeration system inspection: Keep the condenser clean, check whether the suction and exhaust pressure values of the refrigeration compressor are within the specified range, and pay attention to check for leakage or oil seepage.
- Purification and drying system: Regularly check the oil separator and dry filter, and regenerate or replace the molecular sieve if necessary to maintain the purity of the gas.
- Instrument calibration: Regularly calibrate the pressure gauge and vacuum gauge to ensure the accuracy of the instrument.
- Safety protection: When operating and maintaining SF6 equipment, you should follow safe operating procedures, use appropriate personal protective equipment, and ensure that the work area is well ventilated.
- Emergency preparedness: Develop an emergency plan so that you can take quick action to reduce potential safety risks when the equipment fails or leaks.
Through these maintenance steps, you can ensure the efficient operation of SF6 gas filling equipment and the safety of operators.
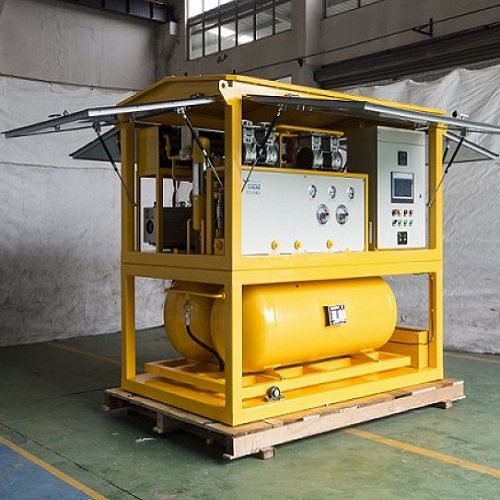
How to Choose SF6 Gas Filling Equipment
When choosing the right SF6 gas filling equipment, you should consider the following key factors:
- Technical specifications of the equipment: Make sure the selected equipment can meet your operating pressure, flow and working environment requirements. Check whether the maximum working pressure of the equipment meets your system standards and whether it has sufficient capacity to complete the filling task.
- Safety features: Since SF6 is a potent greenhouse gas, the selected equipment should be equipped with necessary safety measures such as leak detection, emergency shut-off valves and explosion-proof design to ensure the safety of operators and the environment.
- Reliability and durability: Choose equipment produced by well-known brands and verified manufacturers, which usually have higher quality assurance and longer maintenance cycles. Check the manufacturing materials and structural design of the equipment to evaluate its corrosion resistance and long-term stability.
- Operation convenience: The control system of the equipment should be intuitive and easy to use so that the operator can perform the filling operation quickly and accurately. Consider the human-machine interface design of the equipment, including display screens, buttons and indicator lights, etc.
- After-sales service and technical support: Choose a supplier that provides comprehensive after-sales service and technical support, so that you can get professional help during equipment installation, commissioning and daily maintenance. Understand the supplier’s service network and service commitment to ensure that you can get support in time when you need it.
By comprehensively considering the above factors, you can choose an SF6 gas filling equipment that can meet technical requirements and ensure operational safety.
YUNENG’s SF6 gas refilling equipment is known for its reliability, efficiency, and ease of use. Our products are used by customers all over the world, including in the power generation, transmission, and distribution industries. We are looking forward to building a good cooperation relationship with you!