Application Cases of Turbine Oil Purification in the Power Industry
Table of Contents
Turbine oil purification systems play an important role in maintaining the efficiency and reliability of power generation equipment in the power industry. Its purpose is to remove contaminants from turbine oil to ensure optimal performance and extend the life of critical machinery. Here, we will explore the important applications of turbine oil purification in different types of power plants and highlight the technological advances in this important field.
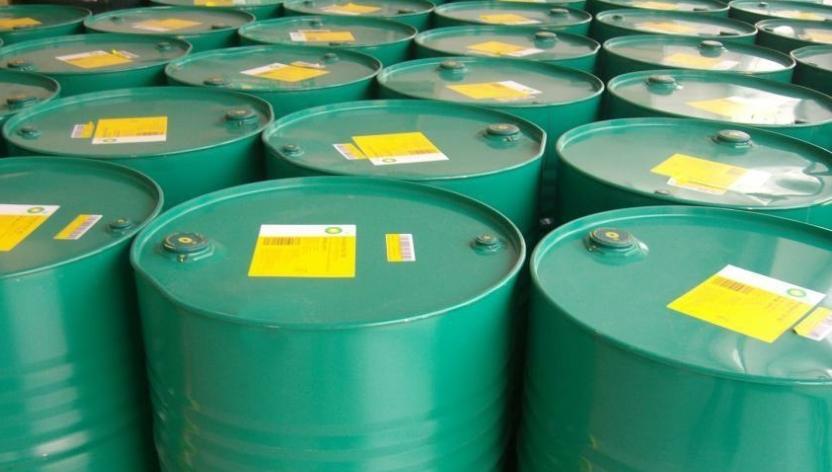
Role of Turbine Oil Purification Systems
Turbine oil purification systems play a critical role in enhancing the performance and durability of turbines and other rotating machinery, especially in power generation facilities. These systems are designed to ensure the cleanliness and chemical stability of turbine oils, which are vital for smooth operation.
- One of their primary functions is to remove contaminants, such as water, particles, gases, and acids. Contaminants in oil can compromise lubrication, cause corrosion, and accelerate equipment wear, leading to reduced efficiency or even failure. By filtering out these impurities, purification systems safeguard the oil’s quality.
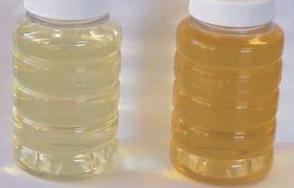
- Furthermore, they maintain oil quality by preserving its lubricating properties. Clean oil reduces friction between turbine components, preventing excessive wear and prolonging the life of critical machinery parts. This helps ensure consistent performance, improving overall operational reliability.
- In addition, by keeping turbine oils in optimal condition, purification systems extend equipment lifespan. Regular oil purification prevents the accumulation of damaging substances, minimizing the risk of unexpected breakdowns. This proactive maintenance reduces downtime and maintenance costs, making it an essential component of any power generation facility’s upkeep strategy.
Turbine Oil Purification in the Power Industry Cases
1. Large Coal-Fired Power Plants
Coal-fired power plants, while a cornerstone of energy production, are prone to various contaminants that can compromise turbine oil quality and performance. These contaminants include:
- Coal Dust: Fine particles of coal can enter the turbine oil system, causing abrasive wear on components and clogging oil passages.
- Ash: Ash produced during the combustion process can accumulate in the oil, leading to increased viscosity and reduced heat transfer.
- Oxidation Products: The high temperatures and pressures within coal-fired turbines can accelerate the oxidation of turbine oil, resulting in the formation of acidic compounds that can corrode metal surfaces.
Turbine oil purification systems in coal-fired power plants are designed to address these challenges by:
- Removing Solid Contaminants: Advanced filtration technologies, such as depth filtration and coalescing filtration, are employed to effectively remove coal dust, ash, and other particulate matter.
- Neutralizing Acids: Chemical treatment processes can be used to neutralize acidic compounds formed during oil oxidation, preventing corrosion and maintaining oil stability.
- Controlling Moisture: Dehydration techniques, such as vacuum degassing, are essential to remove moisture from the oil, which can promote corrosion and reduce lubrication effectiveness.
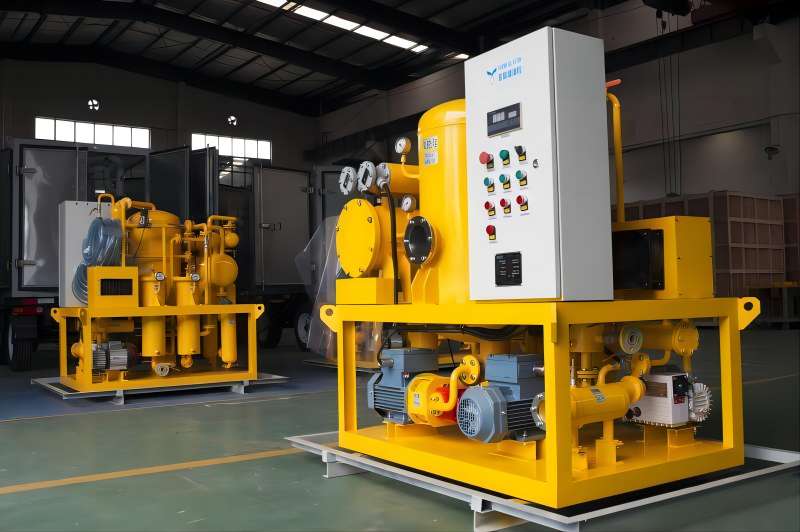
2. Hydroelectric Power Stations
Hydroelectric power plants, while considered environmentally friendly, also face unique challenges regarding turbine oil contamination. These challenges include:
- Water Ingress: Water can enter the turbine oil system through leaks, seals, or ventilation systems, leading to emulsion formation and reduced oil quality.
- Hydrostatic Pressure: The high hydrostatic pressure exerted by water can cause cavitation, which can damage turbine components and accelerate oil degradation.
- Biofouling: Microorganisms can proliferate in turbine oil, leading to sludge formation and increased viscosity.
Turbine oil purification systems in hydroelectric power plants are specifically designed to:
- Remove Water: Coalescing filtration and vacuum degassing are effective in removing water from the oil, preventing emulsion formation and maintaining oil stability.
- Prevent Cavitation: Proper system design and operation can help minimize cavitation by ensuring adequate oil flow and preventing excessive pressure drops.
- Control Biofouling: Regular oil analysis and filtration, combined with the use of biocides when necessary, can help prevent biofouling and maintain oil quality.
3. Gas Turbine Combined Cycle Plant
Gas turbine combined cycle plants are highly efficient power generation systems that utilize both gas and steam turbines. The high temperatures and pressures generated in these plants can place significant stress on the turbine oil. Contaminants such as combustion byproducts, moisture, and wear debris can degrade oil quality and reduce turbine lifespan.
Turbine oil purification systems in gas turbine combined cycle plants are vital for:
- Removal of combustion byproducts: These contaminants can accelerate oil degradation and reduce its lubricating properties.
- Moisture control: Excessive moisture can lead to corrosion and reduced lubrication efficiency.
- Particle removal: Wear debris and other particulate matter can accelerate wear on turbine components.
By regularly purifying the turbine oil in these power plants, operators can ensure the long-term reliability and efficiency of their equipment, while also reducing maintenance costs and downtime.
Technological Advancements and Innovations
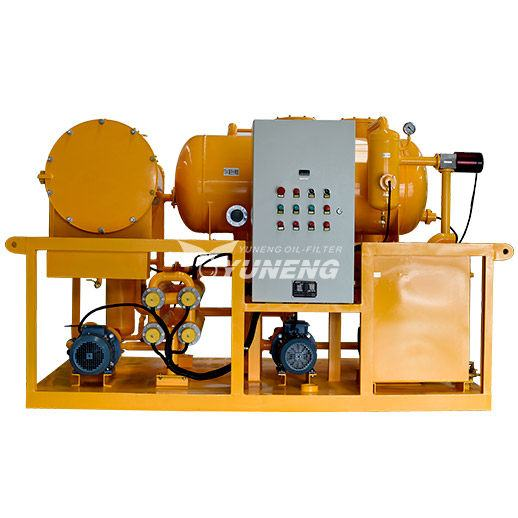
Recent advancements in turbine oil purification technologies, particularly intelligent manufacturing of turbine oil purifiers, such as YUNENG DYJC Series Online Turbine Oil Purification System, have significantly enhanced processing efficiency and automation control. These technological breakthroughs have contributed to improving the overall operational efficiency and equipment management within the power industry.
- Intelligent manufacturing: The integration of advanced automation and data analytics into oil purifier design has resulted in machines capable of self-optimization, predictive maintenance, and real-time performance monitoring.
- Enhanced processing efficiency: These intelligent oil purifiers can process larger volumes of oil more rapidly while maintaining high levels of purity. This increased throughput reduces downtime and minimizes the risk of equipment failure.
- Improved automation control: Advanced control systems enable precise adjustments to operating parameters, ensuring optimal performance under varying conditions. This level of automation also reduces the need for manual intervention, minimizing human error and improving safety.
- Benefits to the power industry: These technological advancements have a direct impact on the power industry by:
- Increasing equipment reliability: Clean and dry turbine oil prolongs the lifespan of critical equipment.
- Reducing maintenance costs: Predictive maintenance capabilities minimize unplanned downtime and reduce overall maintenance expenses.
- Improving overall operational efficiency: By optimizing oil purification processes, power plants can achieve greater energy efficiency and reduce their environmental footprint.
By offering higher processing efficiency, better automation control, and improved equipment reliability, these advancements are playing a crucial role in enhancing the overall performance and sustainability of power generation facilities.
In a word, turbine oil purification systems are indispensable for ensuring the reliability, efficiency, and longevity of power generation equipment across various sectors of the power industry. Continued advancements in purification technology underscore their critical role in maintaining operational excellence and sustainability in power generation facilities worldwide.