Assessing Transformer Oil Filter Machine Running Status
In power systems, transformer oil plays a crucial role as both an insulating and cooling medium. The quality of the transformer oil is directly related to the safe and stable operation of the equipment. The transformer oil filter machine is designed to remove solid impurities, moisture, and gases from the transformer oil. It is essential to accurately determine the running status of the transformer oil filter machine to ensure the quality of the transformer oil and the safety and stability of the power equipment.
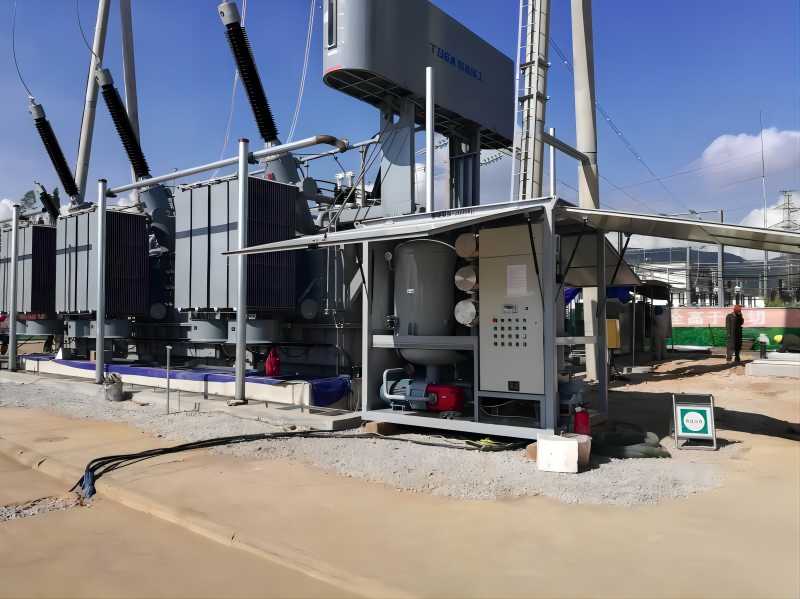
Working Principle of Transformer Oil Purification Systems
The operation of a transformer oil purification system is based on a series of precise mechanical and physical processes. Initially, transformer oil is pumped into the filtration system via an oil pump. The oil then passes through a heater, where it is heated to reduce the solubility of moisture and gases, enhancing the efficiency of subsequent filtration steps. After heating, the oil is cooled in a cooler to prevent high temperatures from damaging the equipment. Finally, the cooled oil passes through precision filter elements, which remove impurities such as dust and metal particles, thereby purifying the oil. The entire process is monitored and regulated by a precise control system to ensure that all parameters meet the requirements for transformer operation.
Key Parameters for Monitoring the Running Status of Transformer Oil Purification Machine
To assess the normal running condition of the transformer oil filter machine, it is crucial to monitor several key parameters.
1. Oil Temperature Monitoring
Oil temperature is a key parameter that directly affects the quality of oil products and the running state of equipment. If the oil temperature is too high, it will accelerate the oxidation of the oil, which will adversely affect its insulation performance and chemical stability. In addition, too high a temperature will cause the equipment to overheat and shorten its service life. High-precision oil temperature sensors can be installed to monitor temperature changes in real time and take necessary measures to adjust.
2. Oil Pressure Monitoring
Oil pressure is an important parameter that reflects the working status of the filtration system. Low oil pressure may indicate system leakage or clogging of the filter element, which can lead to a decrease in filtration efficiency and even result in equipment malfunction. On the contrary, excessive oil pressure may be caused by clogging of the filter element or excessive internal pressure in the system, which can also affect the filtration effect and safe operation of the equipment. By installing an oil pressure sensor, it is possible to monitor changes in oil pressure in real time and promptly identify and address potential issues.
3. Oil Level Monitoring
The oil level directly affects the efficiency of the filter and the safety of the equipment. Too low oil level may mean that the filter element is saturated and needs to be replaced, while too high oil level may be caused by too much oil inside the system, which may affect the filtration effect and the stable operation of the equipment. By installing an oil level sensor, the oil level changes can be monitored in real time to ensure that the oil level fluctuates within an appropriate range.
4. Oil Quality Monitoring
Oil quality monitoring is an important means of evaluating the operational effectiveness of transformer oil filter machines. By regularly sampling and analyzing the moisture, gas, and impurity content in the oil, the quality status of the oil can be understood. If an abnormal increase in moisture, gas, or impurity content is found in the oil, it may indicate that the filtering effect of the filter is poor, or that the oil has reached the replacement cycle. At this point, corresponding measures should be taken in a timely manner, such as replacing the filter element or replenishing fresh oil.
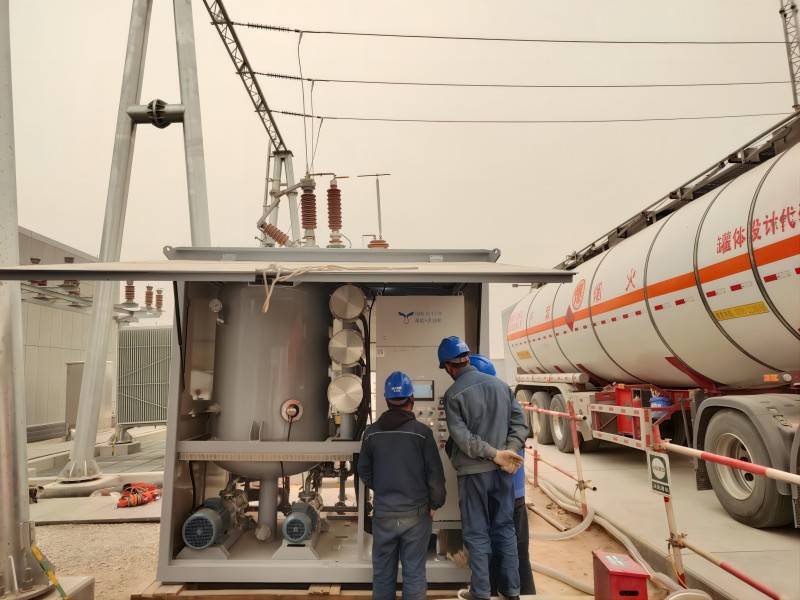
Monitoring the Components of the Filtration System
In addition to these parameters mentioned above, it is also important to monitor the operating conditions of the various components of the transformer oil filter machine, such as motors, pumps, and valves. These components play a critical role in the overall function of the machine, and any malfunction or wear can have a significant impact on the filtration process and the longevity of the equipment. Routine inspections and maintenance can help ensure their continued operation and identify any potential issues before they escalate.
Advanced Monitoring and Control Systems
Modern transformer oil filtration systems are typically equipped with advanced online monitoring and control systems. These systems can continuously collect data on critical parameters like oil temperature, oil pressure, and oil level. Through data analysis, they provide a comprehensive view of the equipment’s operational status. Furthermore, these systems can automatically adjust operational parameters based on the monitored data, optimizing filtration efficiency and enhancing operational effectiveness. Maintenance personnel can use these systems to remotely monitor the equipment, quickly responding to any abnormalities and ensuring stable operation.
Routine Maintenance and Fault Management
Routine maintenance and fault management are fundamental to ensuring the long-term stable operation of transformer oil filtration systems. By developing detailed maintenance plans, including regular inspections, cleaning, and replacement of worn parts, potential faults can be prevented, and the equipment’s lifespan extended. Detailed maintenance logs should be kept to track the equipment’s operational status and maintenance history. Prompt diagnosis and resolution of any faults are necessary to prevent minor issues from escalating into significant problems, affecting the equipment’s normal operation.
Professional Tools and Techniques for Operational Assessment
Using professional tools and techniques is essential for assessing the operational status of transformer oil filtration systems. For example, oil analysis instruments can quickly and accurately measure moisture, gas, and impurity content in the oil. Infrared thermography can be used to non-contact measure surface temperatures of the equipment, helping identify potential hotspots. Simulation experiments and numerical analysis can predict equipment performance under different operating conditions, providing a scientific basis for maintenance decisions.
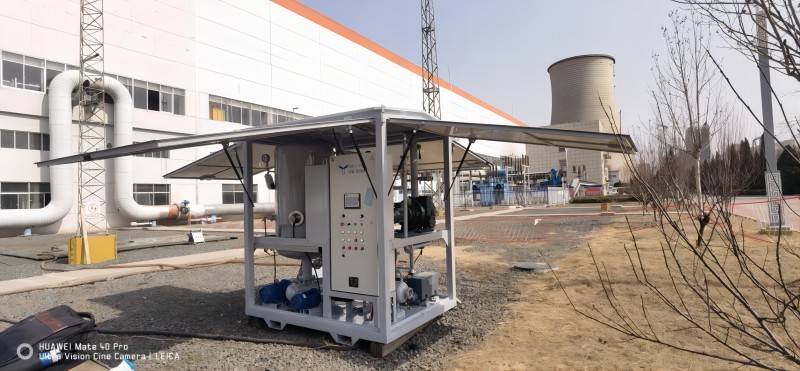
In summary, assessing the operational status of transformer oil filtration systems requires a comprehensive approach that combines various monitoring techniques and technologies. Real-time monitoring of critical parameters such as oil temperature, oil pressure, oil level, and oil quality, along with detailed system component inspections, can thoroughly evaluate the equipment’s condition. Advanced online monitoring systems and professional maintenance tools can enable precise control and effective maintenance of the equipment. Continuous technological innovation and management optimization can further enhance the operational efficiency and reliability of transformer oil filtration systems, contributing significantly to power systems’ stable operation and the power industry’s sustainable development.