Common Mistakes to Avoid When Operating Turbine Oil Purifier
Table of Contents
Turbine oil purifiers are an important piece of equipment for maintaining and extending the life of your turbine system by removing contaminants from the oil. However, improper operation and lack of proper maintenance can lead to system inefficiencies, shortened oil life, and ultimately costly downtime. By understanding the basics of turbine oil purifiers, identifying common operating errors, and implementing best practices, we can optimize equipment performance and extend its life.
Basics of a Turbine Oil Purifier
A turbine oil purifier is a machine used in power plants, marine vessels, and industrial settings where turbines are employed. Its primary function is to clean turbine oil by removing impurities that can degrade performance. The purifier typically uses a centrifugal force mechanism to separate contaminants based on density differences. The clean oil is returned to the turbine system, while the contaminants are discarded, ensuring the oil remains in optimal condition.
The purifier works in two main steps: separation and filtration.
- During the separation phase, the dirty oil enters the purifier and is subjected to high-speed rotation, which forces contaminants like water, sludge, and particulate matter to the edges of the separator drum. The oil that remains in the center is cleaner and is pumped back into the turbine system.
- In the filtration phase, fine contaminants are removed through filtration cartridges or other filtration media, ensuring that the oil is thoroughly purified.
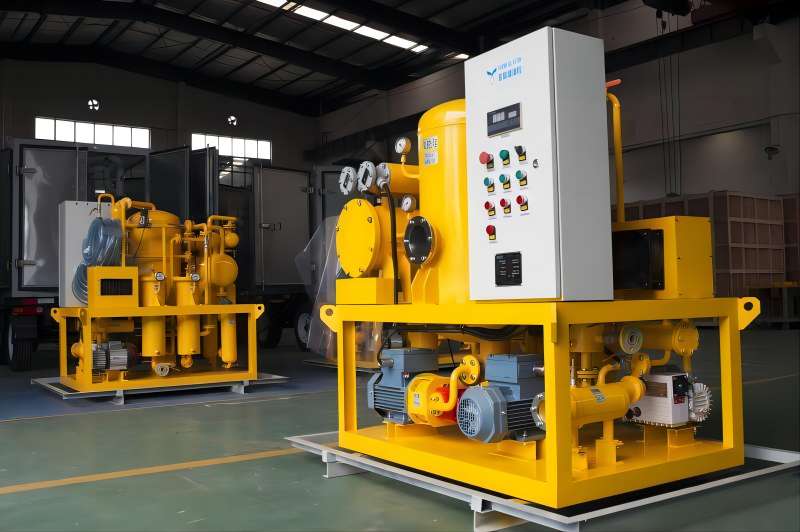
Common Operational Mistakes and How to Avoid Them
Here are four of the most common operating errors when running a turbine oil purifier, detailed descriptions, and strategies for avoiding them.
Failing to Monitor Oil Quality Regularly
One of the most significant mistakes is neglecting to regularly monitor the quality of the oil being purified. While the turbine oil purifier is designed to clean the oil, over time, the oil can degrade or become contaminated again, even after going through the purification process. Failure to monitor oil quality can lead to unnoticed contamination, resulting in decreased lubrication efficiency, potential overheating, and turbine component wear.
How to Avoid It?
- Establish a routine for oil testing: Implement a consistent schedule for oil analysis, such as performing periodic sample tests or using oil quality monitoring sensors.
- Use oil analysis tools: Invest in oil testing kits or sensors that can detect contaminants such as water, particulates, and sludge in real time.
- Check for water content regularly: Water is one of the most common contaminants found in turbine oil. Be sure to test for water content, as even small amounts can cause corrosion and wear.
- Establish thresholds: Set specific limits for acceptable oil quality and ensure the purifier is activated or the oil replaced when those limits are exceeded.
Incorrect Oil Flow Rate
The flow rate of oil through the purifier has a direct effect on the efficiency of the separation process. If the flow rate is too high, the purifier may not have sufficient time to remove contaminants, leading to incomplete filtration effectively. Conversely, if the flow rate is too low, the oil may move through the purifier too slowly, which can reduce the system’s overall throughput and operational efficiency.
Here are tips to avoid:
- Follow Manufacturer Guidelines: Always adhere to the recommended flow rate provided by the manufacturer, as these guidelines are tailored to the purifier’s design and capacity.
- Adjust Flow Rate Based on Oil Conditions: Modify the flow rate according to the oil’s viscosity and contamination level. For example, thicker oils or those with higher contaminants may need a slower flow to ensure proper separation.
- Monitor Flow with Flow Meters: Install flow meters to track the oil flow rate continuously. This will help maintain the optimal flow rate range for efficient purification.
- Conduct Regular Inspections: Regularly inspect components like valves and hoses to ensure there are no blockages or leaks that could disrupt the flow rate and hinder the purifier’s performance.
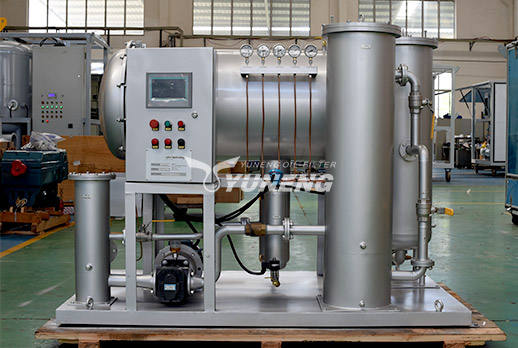
Improper Handling of Contaminated Oil
Improper handling of contaminated oil can not only disrupt the purification process but also pose serious environmental and safety risks. For instance, failing to store or dispose of contaminated oil correctly can lead to spills, environmental harm, or health hazards for personnel. A common mistake among operators is neglecting proper disposal procedures, such as using inappropriate containers or disregarding disposal regulations.
We can do this to avoid it:
- Follow proper disposal guidelines: Always adhere to local environmental laws and regulations when disposing of contaminants like sludge, water, and used oil. Use designated containers and ensure safe handling of hazardous materials.
- Store contaminated oil properly: If temporary storage is needed before disposal, use sealed, appropriate containers to prevent leaks and environmental contamination.
- Train operators on safety and disposal: Make sure all operators are trained in the correct procedures for handling contaminated oil, including proper storage, labeling, and disposal methods.
- Regularly inspect storage areas: Conduct frequent checks of storage containers for signs of leaks or damage. If any issues are found, take prompt corrective action to avoid contamination.
Neglecting Regular Maintenance
Turbine oil purifiers, like all industrial machinery, require consistent maintenance to function at their best. A common mistake is postponing routine upkeep or overlooking early warning signs of wear and tear. Neglecting proper maintenance can lead to decreased performance, higher chances of system failure, and escalated repair costs. For example, if the separator bowl is not cleaned regularly or seals are not replaced when they become worn, contaminants could bypass the purification process, resulting in oil contamination.
How to Avoid It:
- Establish a maintenance schedule: Set up a clear and regular maintenance plan for the turbine oil purifier. This should include tasks like cleaning the separator bowl, replacing worn seals, inspecting the filtration system, and lubricating moving parts.
- Check for leaks: Routinely inspect seals, gaskets, and hoses to identify leaks, which can cause inefficiencies and pose safety risks.
- Inspect the filtration media: Filters can become clogged or degrade over time, reducing the purifier’s efficiency. Follow the manufacturer’s guidelines to check and replace the filtration media as needed.
- Train staff on maintenance: Ensure operators are trained to recognize early signs of wear, such as unusual noises, vibrations, or drops in performance, and are capable of performing basic maintenance tasks.
By addressing these common mistakes and following the suggested strategies, you can improve the performance of your turbine oil purifier, prolong its lifespan, and ensure that your turbine system operates efficiently and safely.
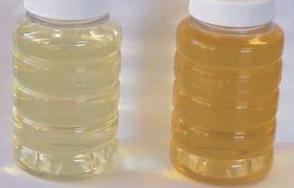
Best Practices for Operating Turbine Oil Filter Machines
To get the most out of your turbine oil purifier, following best practices is essential. Here are a few key tips:
- Preheat Oil Before Filtration: Warming the oil to the recommended temperature before filtration lowers its viscosity, making it easier to remove contaminants. This step can also enhance the purifier’s overall efficiency.
- Use Quality Filtration Media: Choose the appropriate, high-quality filtration media for your turbine oil purifier. Premium filters are more effective at capturing fine particles and can prolong the life of your system.
- Regularly Calibrate the Purifier: The purifier’s performance may decline over time due to normal wear. Regular calibration helps maintain optimal functionality and ensures efficient operation.
- Train Operators Thoroughly: Comprehensive training is vital for all operators. They should understand the purifier’s functions, be able to troubleshoot effectively and know proper oil handling procedures.
- Provide Adequate Ventilation: Turbine oil purifiers produce heat during use. Place the purifier in a well-ventilated area to avoid overheating and ensure consistent, efficient operation.
Where To Find a Turbine Oil Purifier?
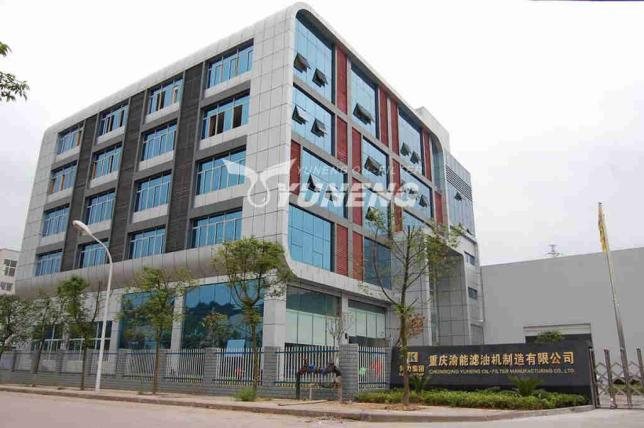
Turbine oil purifiers can be found through various industrial equipment suppliers and manufacturers. Major suppliers typically offer a range of oil purification systems suited for different types of turbines and industries. It’s important to choose a reputable supplier that provides not only high-quality products but also technical support and maintenance services.
You can find turbine oil purifiers through:
- Industrial Equipment Suppliers: Many companies specialize in offering turbine maintenance equipment, including oil purifiers. Look for suppliers with experience in the turbine and power generation industries.
- Manufacturer Direct Sales: Some turbine manufacturers, such as YUNENG, sell their proprietary oil purifiers directly to customers.
- Online Marketplaces: Reputable online industrial marketplaces often carry turbine oil purifiers from various manufacturers.
- Local Distributors: Depending on your region, there may be local distributors who can provide turbine oil purifiers and servicing.
Before purchasing, it’s important to assess your specific needs, including the size of the turbine, the type of oil, and the level of contamination you’re dealing with, to ensure you select the most appropriate purifier.