Dry Air Generator For Transformer Frequently Asked Questions(FAQs)
Ensuring the optimal humidity level inside the equipment is crucial when it comes to transformer maintenance. The transformer drying air generator is a specialized equipment designed specifically for this purpose. This article will introduce some common issues related to transformer dry air generators.
Transformer Dry Air Generators Vs. Ordinary Dehumidifiers
Transformer dry air generators are purpose-built for the specific needs of transformers, offering precise control over humidity levels to prevent moisture-related damage. Unlike ordinary dehumidifiers, which typically target broader indoor humidity control in residential or commercial settings, transformer dry air generators are engineered with features that cater specifically to the unique environment and operational demands of transformers.
Transformer dry air generators employ advanced technologies such as silica gel adsorption or molecular sieve absorption to achieve extremely low dew points, often below -40°C, ensuring that even the smallest traces of moisture are effectively removed from the transformer’s insulation system. This level of moisture control far surpasses what traditional dehumidifiers can achieve, making the machines indispensable for transformer applications where moisture ingress can lead to insulation degradation and eventual failure.
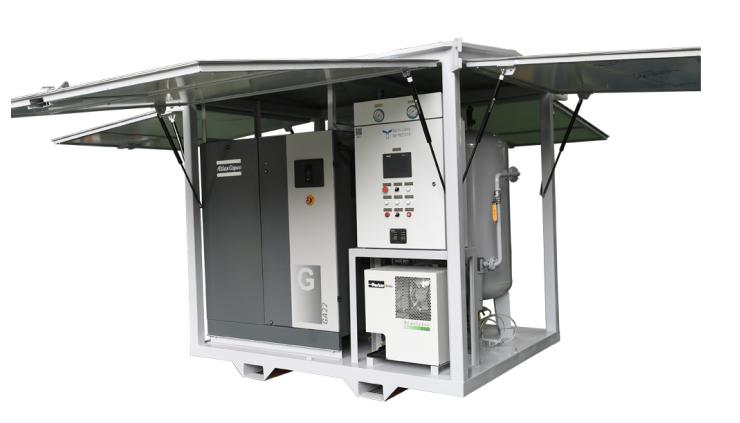
What Are The Main Usage Scenarios Of Transformer Dry Air Generators
Transformer dry air generators are essential components in various industrial and commercial settings, providing precise humidity control to protect critical equipment and processes. Here are some of the primary usage scenarios:
Transformer Dry Air Generators are critical components in the maintenance and operation of transformers, particularly in scenarios where moisture control is paramount. The following are the main usage scenarios:
1. New Transformer Commissioning
When new transformers are installed and commissioned, they are at their most vulnerable to moisture ingress. The insulation system, primarily composed of cellulose and oil, is highly susceptible to absorbing moisture from the surrounding environment. This moisture can degrade the dielectric strength of the insulation, leading to reduced efficiency and potential failures. TDAGs are deployed during the commissioning phase to create a controlled, moisture-free environment within the transformer. By continuously supplying dry air, TDAGs ensure that the insulation remains dry, preserving the transformer’s integrity from the very beginning.
2. Long-Term Storage of Transformers
Transformers that are not immediately put into service often require long-term storage. During this period, the risk of moisture ingress increases, particularly in regions with high humidity levels. If moisture is allowed to accumulate, it can lead to the deterioration of the insulation materials, corrosion of metal components, and ultimately, the transformer’s failure once it is energized. TDAGs play a crucial role in such storage scenarios by maintaining a low-humidity environment inside the transformer. They ensure that the moisture content remains well below critical levels, effectively safeguarding the transformer’s condition throughout the storage period.
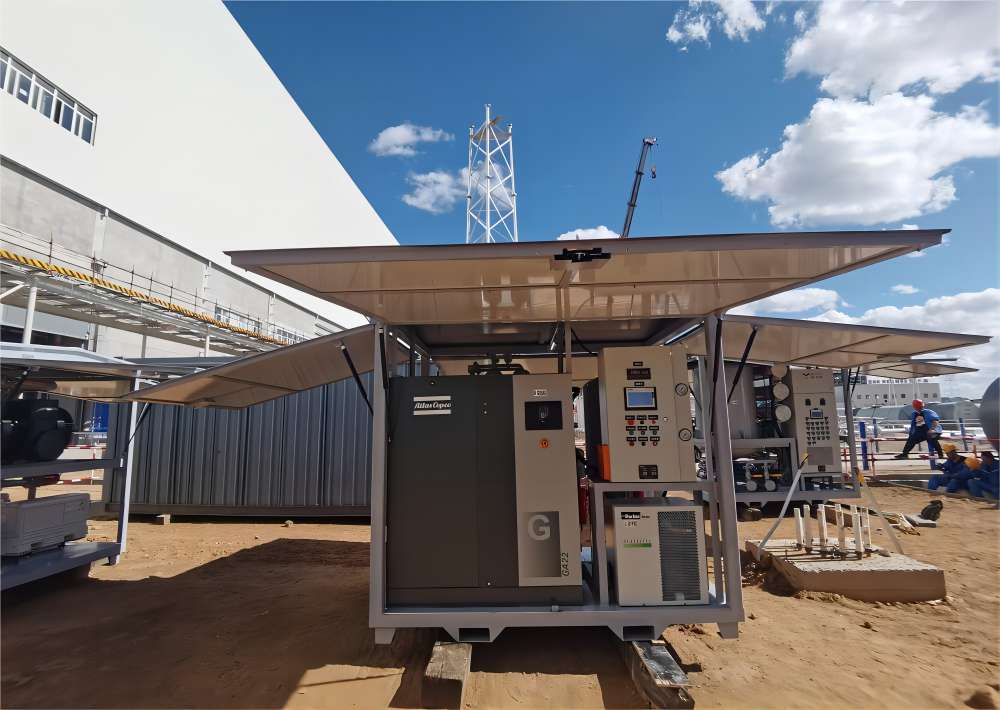
3. Operational Maintenance and Repair
Even after transformers are commissioned and operational, they require ongoing maintenance to ensure they function at peak performance. During routine maintenance or repair activities, the transformer’s internal components may be exposed to ambient air, which can introduce moisture into the system. Transformer dry air generators are utilized during these operations to provide a continuous flow of dry air, preventing moisture from entering the insulation system. This practice is particularly important during oil filtration, replacement of insulation materials, or when transformers are opened for internal inspections. By controlling the moisture levels, Transformer dry air generators help in preserving the insulation’s dielectric properties, ensuring the transformer remains reliable and efficient over its operational life.
4. Emergency Situations
In the event of a transformer failure or emergency repairs, moisture control becomes critical. For instance, if a transformer experiences a leak or if there is a need for urgent repairs that involve opening the transformer, the risk of moisture ingress is high. Transformer dry air generators can be quickly deployed to provide dry air, minimizing the exposure time and reducing the risk of further damage. In such emergency scenarios, these machines not only protect the transformer from additional moisture-related issues but also help in speeding up the repair process by maintaining a stable and dry internal environment.
5. High-Humidity Environments
In geographical regions with consistently high humidity levels, transformers are under constant threat of moisture ingress. These environments make it challenging to maintain optimal humidity levels within the transformer using conventional methods. Transformer dry air generators are particularly useful in such scenarios, as they can continuously supply dry air to the transformer, ensuring that the internal environment remains dry regardless of external conditions. This continuous protection is crucial in preventing long-term moisture accumulation that could compromise the transformer’s performance and lifespan.
6. Retrofit and Upgrade Projects
When older transformers are retrofitted with new technology or upgraded to enhance their performance, the internal components may be exposed to moisture during the process. TDAGs are often employed during these projects to maintain a dry environment inside the transformer. This precaution ensures that the upgraded components are not compromised by moisture, which could otherwise undermine the benefits of the retrofit or upgrade.
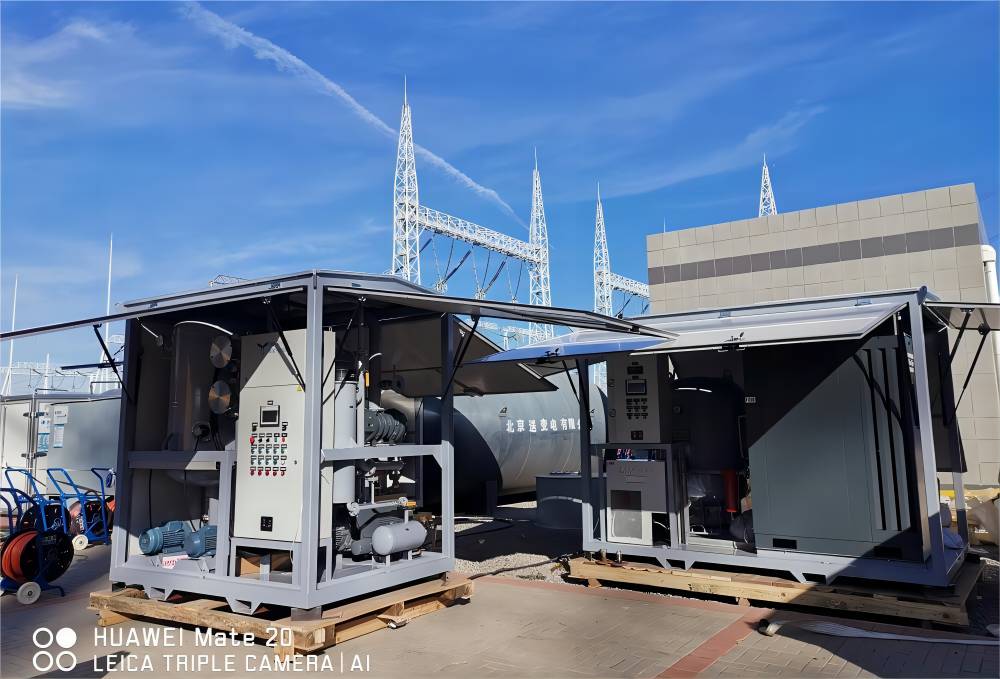
How Often Is The Maintenance Cycle Of Dry Air Generators
The maintenance cycle of Transformer Dry Air Generators is a critical aspect of ensuring their long-term reliability and efficiency. Generally, it requires periodic maintenance every 6 to 12 months, depending on operational conditions and the specific model in use. However, in environments with higher humidity or more demanding operational conditions, more frequent checks may be necessary.
- Routine Inspections: Every few months, it’s essential to inspect the desiccant material (such as silica gel or molecular sieve) for signs of saturation. If the desiccant is saturated, it should be regenerated or replaced to maintain optimal moisture absorption capacity.
- Filter Maintenance: Filters should be replaced every 3 to 6 months, depending on the air quality and the generator’s usage intensity. Clogged or dirty filters can impede airflow, reducing the efficiency of the drying process.
- Calibration of Sensors: Humidity sensors should be calibrated at least once a year to ensure accurate readings. This ensures that the system maintains the precise control needed for transformer protection.
Common Problems And Solutions For Dry Air Generators
Transformer Dry Air Generators, while robust, can occasionally encounter issues that may affect their performance. Understanding these common problems and their solutions ensures minimal downtime and optimal operation:
- Silica Gel/Molecular Sieve Saturation: Over time, the desiccant material in dry air generators becomes saturated with moisture, reducing its effectiveness. This is indicated by a color change in the desiccant or an increase in the dew point of the air. The solution is to regenerate the desiccant by heating it to remove absorbed moisture or to replace it entirely. Regular monitoring can prevent saturation from leading to inadequate moisture control.
- Filter Clogging: Air filters in dry air generators can become clogged with dust and debris, restricting airflow and reducing the system’s efficiency. Regular filter inspections and replacements are essential to avoid this issue. Using high-quality filters can also extend the intervals between changes.
- Sensor Calibration Drift: Humidity sensors in the dry air generator may drift over time, leading to inaccurate readings. This can result in the generator either overworking (leading to unnecessary wear) or underperforming (leading to moisture ingress). Periodic recalibration of these sensors ensures that they continue to provide accurate data, allowing the generator to maintain optimal humidity levels.
- Electrical Component Failures: Like any other equipment, dry air generators can experience electrical issues such as sensor failures or control panel malfunctions. Routine electrical checks and immediate repair or replacement of faulty components can prevent these problems from escalating.
By addressing these issues promptly and following a regular maintenance schedule, users can ensure that their Transformer Dry Air Generators continue to operate efficiently, providing critical moisture protection for transformers and extending their operational lifespan.
Yuneng Transformer Dry Air Generator
The YUNENG dry air generator is designed for various applications, including the drying of large power equipment such as transformers and reactors within power systems. It is also well-suited for air drying and circulating drying in industries such as warehouses, packaging, and electronics.
If you are in any need, please contact YUNEG.