Dry Air Generators: Essential Tools for Safe and Efficient Transformer Drying
Transformers are crucial components in the electrical grid, responsible for stepping up or down voltage levels to efficiently transmit electricity. Proper maintenance of these transformers is essential for ensuring reliable power delivery. Moisture is a significant enemy of transformer health. It can weaken insulation, accelerate corrosion, and lead to electrical breakdowns. Dry air generators play a vital role in transformer maintenance by providing a controlled and efficient method for removing moisture from the transformer during critical processes like installation, repairs, and oil changes.
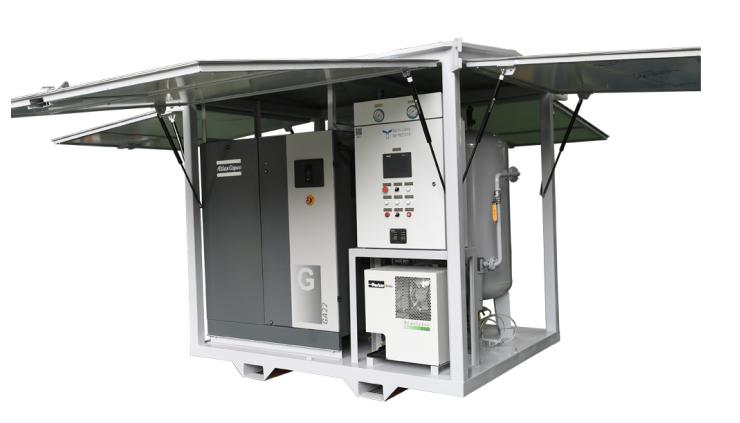
Importance of Dry Air in Transformer Maintenance
Transformers rely on the insulating properties of oil and cellulose paper to function safely and efficiently. Unfortunately, moisture can easily enter a transformer through various means, including condensation from ambient air, leaks, and even from the cellulose paper itself. The presence of moisture can have several detrimental effects:
- Reduced Insulation Strength: Water readily absorbs into cellulose paper, significantly reducing its electrical resistance. This can lead to leakage currents and ultimately electrical breakdown.
- Corrosion: Moisture promotes the corrosion of metal components within the transformer, such as windings and tank walls. This can weaken the structure and compromise the transformer’s integrity.
- Formation of Byproducts: The interaction of moisture with transformer oil can lead to the formation of harmful byproducts like sludge and acids. These byproducts further accelerate the degradation of insulation and oil.
By maintaining a dry environment inside the transformer during critical maintenance procedures, dry air generators help mitigate these risks. They ensure that the insulation remains dry and retains its insulating properties, preventing electrical breakdowns and extending the transformer’s lifespan.
Working Principle of Dry Air Generators
Dry air generators function by utilizing desiccant technology to extract moisture from surrounding air. Desiccants are materials with a high attraction to water vapor, a property known as hygroscopicity. Here’s a breakdown of the process:
- Desiccant Bed: The core component of the generator is the desiccant bed. This bed is filled with a specially chosen material known as a desiccant. These desiccants are highly hygroscopic, meaning they have a strong attraction to water vapor molecules in the air.
- Moisture Capture: As air is drawn into the generator by a fan, it passes through the desiccant bed. The desiccant material actively attracts and adsorbs water vapor molecules from the air stream. This adsorption process essentially “sticks” the moisture molecules to the surface of the desiccant.
- Dry Air Delivery: Once the moisture has been removed from the air by the desiccant, the now dry air exits the generator. This dry air is then directed towards the transformer for drying purposes.
- Desiccant Regeneration: To maintain its effectiveness in capturing moisture, the desiccant needs to be regenerated periodically. The regeneration process varies depending on the specific technology employed by the generator. There are two main methods:
- Regeneration by Heating (Desiccant Reactivation): In this method, the desiccant bed is heated to a specific temperature. This heat drives off the adsorbed moisture molecules from the desiccant, allowing them to be desorbed and released as water vapor. The released vapor is then expelled from the generator. Once dry, the desiccant is ready to capture moisture again.
- Regeneration by Depressurization (Pressure Swing Adsorption – PSA): This method utilizes changes in pressure to regenerate the desiccant. In a PSA system, two desiccant beds operate alternately. While one bed is actively capturing moisture from the incoming air stream, the other bed undergoes regeneration. The regeneration process involves lowering the pressure within the inactive bed, which causes the adsorbed moisture to be released from the desiccant. This released moisture is then vented from the system. The pressure is then restored, and the regenerated bed can resume moisture capture.
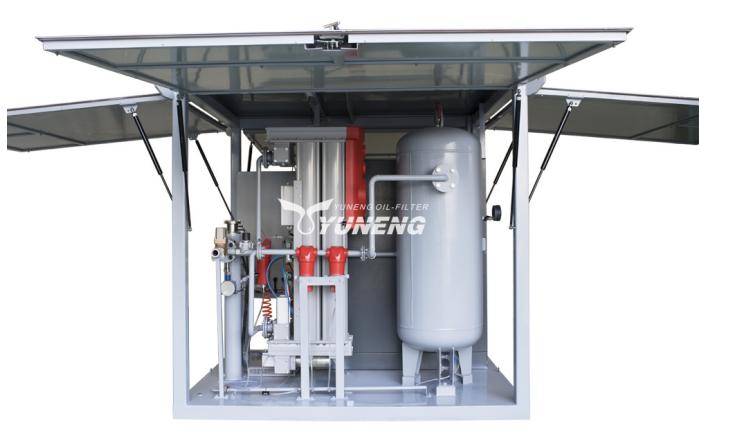
Advantages of Utilizing Dry Air Generators for Transformer Drying
Transformer dry air machines offer several significant benefits when compared to traditional methods of transformer drying. Here’s a closer look at these advantages:
- Precise Dew Point Control: Traditional methods, such as simply heating the transformer itself, often lack precise control over the moisture content of the air. Dry air generators, on the other hand, allow for very precise control over the dew point of the air entering the transformer. The dew point is the temperature at which condensation occurs. By maintaining a very low dew point in the dry air, these generators effectively prevent moisture from forming within the transformer, mitigating potential damage.
- Enhanced Efficiency: Compared to traditional methods, dry air generators offer a more targeted and efficient approach to drying transformers. They remove moisture directly from the air stream, minimizing wasted energy consumption. Traditional methods, such as heating the entire transformer, can be less efficient as they heat not only the air but also the transformer itself.
- Improved Safety: Dry air generators eliminate the need for open flames or high temperatures during the drying process. This significantly improves safety in the work environment, reducing the risk of fire hazards or burns.
- Faster Drying Times: Dry air generators can significantly accelerate drying times compared to passive methods that rely solely on ambient conditions. This translates to quicker completion of transformer maintenance tasks, minimizing downtime for critical electrical equipment.
- Reduced Environmental Impact: Dry air generators are a more environmentally friendly solution compared to some traditional methods that may involve the use of potentially hazardous chemicals for drying purposes. Additionally, the efficient operation of dry air generators minimizes energy consumption, further reducing their environmental footprint.
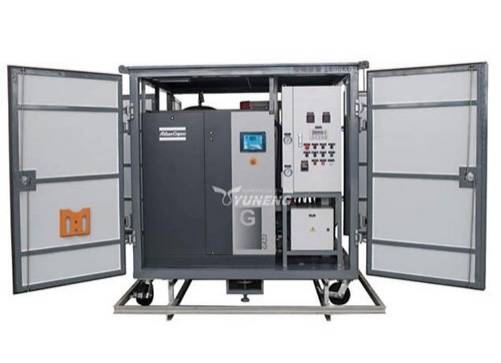
Transformer Drying Methods with Dry Air Generators
There are two primary methods for drying transformers using dry air generators: purging and displacement. Each method offers distinct advantages and is best suited for specific scenarios.
1. Purging Method: Continuous Flow Drying
The purging method utilizes a continuous flow of dry air to remove moisture from the transformer. Here’s a breakdown of the purging process:
- Pre-Purge (Optional): In the initial stage, an optional pre-purge with filtered ambient air can be performed. This pre-purge helps remove dust and loose debris from the transformer before introducing the dry air.
- Dry Air Purging: Following the pre-purge (or directly if not used), dry air from the generator is steadily introduced into the transformer. The flow rate of the dry air is carefully controlled to ensure efficient moisture removal. The duration of the purging process depends on several factors, including:
- Transformer Size: Larger transformers will naturally require a longer purging time compared to smaller ones due to the larger volume of air that needs to be dried.
- Initial Moisture Content: If the transformer has a high initial moisture content, a longer purging time will be necessary to achieve the desired dryness level.
- Desired Final Dew Point: The target dew point, which is the temperature at which condensation occurs, dictates the level of dryness required. Achieving a very low dew point will necessitate a longer purging duration.
- Continuous Dew Point Monitoring: Throughout the purging process, the dew point of the air exiting the transformer is constantly monitored. This monitoring is crucial to ensure the effectiveness of the drying process. Once the desired dew point is reached and maintained for a predetermined period, the purging process can be stopped.
2. Displacement Method: Closed-Loop Drying
The displacement method employs a closed-loop system to completely replace the moist air within the transformer with dry air. Here’s a closer look at the displacement process:
- Transformer Sealing: Prior to initiating the drying process, the transformer is meticulously sealed. This meticulous sealing ensures that the drying occurs within a closed environment, preventing the re-entry of moist ambient air.
- Dry Air Displacement: Dry air from the generator is introduced into the sealed transformer, gradually pressurizing it. As the pressure increases, the moist air within the transformer is displaced and forced out. The exiting moist air is monitored for moisture content to track the progress of the drying process.
- Maintaining Pressure and Monitoring Moisture: The displacement process continues until the desired level of dryness is achieved, as indicated by the monitored moisture content of the exiting air. Once the target dryness level is reached, the pressurization from the dry air generator can be stopped.
Choosing Between Purging and Displacement Methods
The selection between purging and displacement methods depends on several factors:
- Transformer Size: The displacement method is generally faster, particularly for larger transformers, as it replaces the entire volume of moist air more efficiently.
- Moisture Sensitivity: If the transformer components are highly sensitive to moisture, the displacement method may be preferred due to its ability to achieve a more complete and rapid drying process.
- Leakage Risk: If there’s a concern about potential leaks in the transformer seals, the purging method might be a safer option as it operates at lower pressure compared to the displacement method.
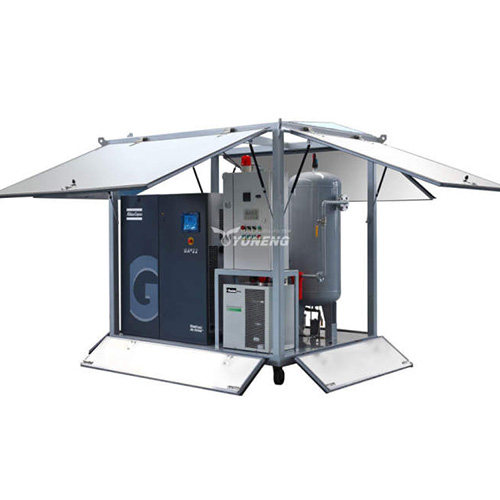
Tips for Choosing the Right Dry Air Generator
Several factors need to be considered when selecting a dry air generator for transformer drying:
- Capacity: The generator’s capacity, measured in cubic meters per hour (m³/hr), should be sufficient to handle the volume of the transformer being dried. A larger transformer will require a higher capacity generator to achieve efficient drying within a reasonable timeframe.
- Dew Point: The generator’s ability to achieve a very low dew point is crucial. The desired dew point will depend on the specific application and transformer oil type. Generally, a dew point below -40°C is recommended for optimal drying results.
- Portability: Depending on the work environment, portability may be a significant factor. Generators come in various sizes and configurations, with some designed for easy transportation and use in field applications.
Safety Precautions During Transformer Drying
Working with transformers requires adherence to strict safety protocols. Here are some key safety precautions to follow when using dry air generators for transformer drying:
- Qualified Personnel: Only qualified and authorized personnel trained in safe transformer maintenance procedures should operate the dry air generator.
- Proper Grounding: Ensure proper grounding of the transformer and all associated equipment to prevent electrical hazards.
- Explosion Protection: Some transformer oils can generate flammable gas mixtures under certain conditions. If such oils are present, use a dry air generator specifically designed for explosion-proof operation.
- Ventilation: During purging, ensure adequate ventilation to remove the displaced moist air from the work area.
- Personal Protective Equipment (PPE): Personnel working on the transformer should wear appropriate personal protective equipment (PPE) such as gloves, safety glasses, and flame-resistant clothing.
- Monitoring: Continuously monitor the dew point, pressure, and temperature throughout the drying process to ensure proper operation and avoid exceeding safe operating parameters.
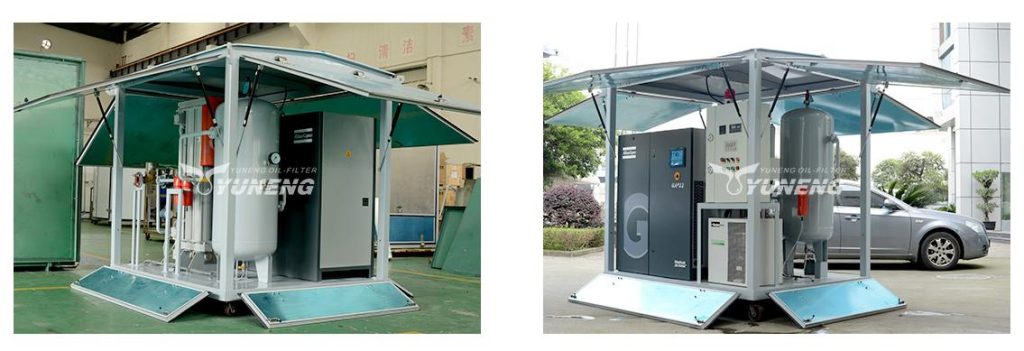
Conclusion
Dry air generators are a valuable tool for transformer maintenance, promoting safe and efficient drying procedures. These generators offer precise control over moisture removal, minimizing the risks associated with moisture and ensuring optimal transformer performance and longevity. By understanding the benefits, drying methods, and safety considerations, transformer maintenance professionals can leverage dry air generators to effectively maintain this critical electrical infrastructure.