Economic Analysis of Transformer Oil Regeneration for Industrial Power Systems
Table of Contents
Transformer oil plays a crucial role in the operation and longevity of electrical transformers in industrial power systems. However, over time, this oil degrades due to exposure to heat, moisture, and contaminants. Transformer oil regeneration has emerged as a cost-effective and environmentally friendly solution. This article talks about the economic analysis of transformer oil regeneration, covering its processes, components, costs, and industrial applications.
What is Transformer Oil Regeneration?
Transformer oil regeneration is a process that restores the dielectric strength and cooling properties of degraded transformer oil by removing impurities and contaminants. Unlike a simple oil filtration or purification, which only removes particulate matter and moisture, regeneration focuses on full chemical recovery, eliminating dissolved gases, acids, sludge, and oxidation by-products.
Regeneration involves passing the degraded oil through a complex series of chemical and physical treatments that restore its original quality, extending the life of both the oil and the transformer itself. The process can be conducted on-site with specialized machinery, ensuring minimal downtime for industrial power systems.
Components of a Transformer Oil Regeneration Machine
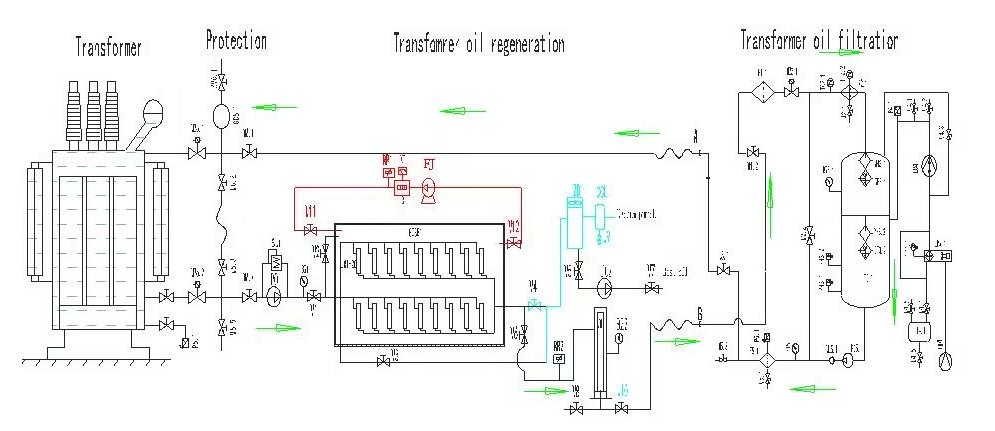
A transformer oil regeneration machine is designed for the regeneration process. It usually consists of several key components that work together to purify and restore transformer oil:
- Filtration Unit: This component removes suspended particles and sludge that accumulate in the oil over time.
- Degassing System: It extracts moisture and dissolved gases, both of which can significantly degrade the oil’s insulating properties.
- Adsorption Columns: These contain adsorbents like fuller’s earth, which remove polar compounds, acids, and oxidation products.
- Heating System: Oil is heated to optimize the regeneration process by enhancing the removal of contaminants.
- Vacuum System: It creates the required low-pressure environment for moisture and gas removal.
These machines operate on-site and can process the oil directly in the transformer, thus minimizing downtime and reducing operational disruptions.
Transformer Oil Regeneration vs. Replacement: Cost Implications
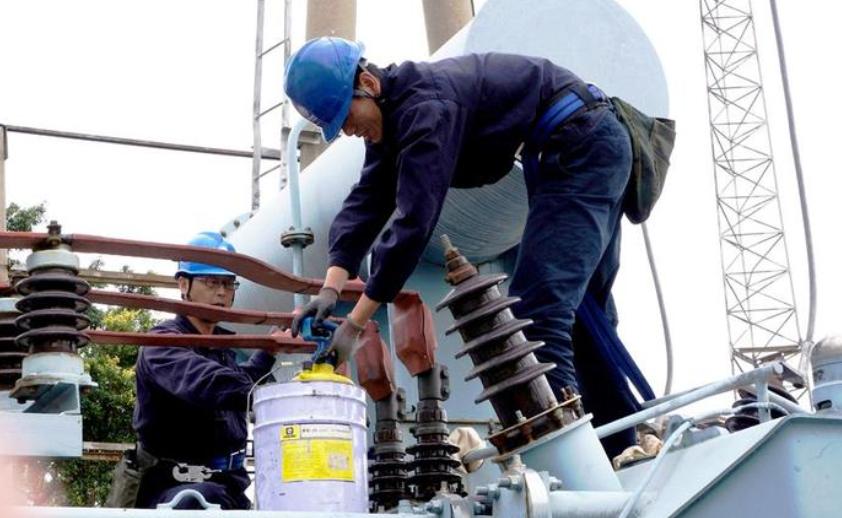
The cost of replacing transformer oil can be substantial, especially for large industrial systems where transformers require thousands of liters of oil. Replacement involves not only the cost of new oil but also labor, disposal fees for hazardous waste, and the cost of downtime.
In contrast, transformer oil regeneration offers significant cost savings. The initial investment in a regeneration machine may seem high, but the long-term benefits make it more economical:
- Lower Operational Costs: Regeneration can be done at a fraction of the cost of new oil replacement. On-site regeneration also reduces transportation and disposal costs.
- Minimal Downtime: Oil regeneration can often be performed without taking transformers offline, unlike oil replacement, which typically requires a shutdown.
- Extended Equipment Life: Regeneration improves oil quality, preventing the degradation of transformer components, leading to longer equipment lifespans and reduced capital expenditure for new equipment.
According to industry estimates, transformer oil regeneration can reduce maintenance costs by 50-70% compared to oil replacement, making it a highly attractive option for industrial power systems.
Economic Benefits of Transformer Oil Regeneration
transformer oil regeneration offers great economic advantages, particularly for industrial applications where transformers are critical to operations. The following key benefits highlight why oil regeneration is a preferred approach:
- Cost Savings: The most immediate economic benefit is the significant cost reduction compared to oil replacement. The regeneration process can cost up to 50% less than buying new oil, depending on the condition of the oil and the regeneration system used.
- Extended Transformer Life: By regenerating transformer oil, industries can extend the operational lifespan of transformers. Regular oil regeneration prevents the build-up of harmful contaminants that can damage the transformer’s insulation and core, reducing the need for expensive repairs or transformer replacements.
- Environmental Impact: Regenerating oil reduces the environmental burden of producing and disposing of large quantities of new transformer oil. This not only cuts costs but also aligns with sustainability goals, helping companies meet environmental regulations.
- Energy Efficiency: Regenerated oil improves transformer efficiency by restoring its dielectric properties. This enhances the overall energy efficiency of the power system, reducing energy losses and improving operational cost-effectiveness.
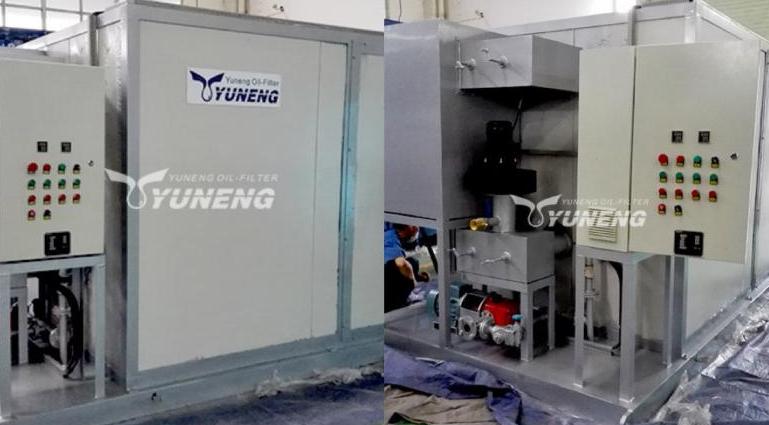
Industrial Applications of Transformer Oil Regeneration
Transformer oil regeneration is extensively utilized across industries that depend on large-scale electrical systems. Key applications include:
- Power Generation Plants: Both conventional and renewable power plants rely on substantial transformers for effective power distribution. Regenerating transformer oil helps ensure these transformers operate efficiently, minimizing the need for frequent maintenance or replacement shutdowns.
- Heavy Manufacturing: Industries that require substantial electricity, such as steel manufacturing, automotive production, and chemical processing, utilize transformer oil regeneration to sustain transformer performance and reduce costly downtime.
- Utility Companies: Electric utilities implement transformer oil regeneration throughout their networks to prolong the lifespan of their equipment. The significant scale of these operations allows for considerable cost savings by avoiding the need for regular oil replacement.
- Data Centers: In sectors like IT and telecommunications, where continuous power supply is crucial, oil regeneration mitigates the risk of transformer failures, ensuring uninterrupted operations and reliability.
Need to Regenerate Transformer Oil?
To address the challenges of transformer oil degradation, professional solutions are essential. YUNENG, a leading manufacturer of transformer regeneration machines, offers advanced technology designed to restore the quality of transformer oil efficiently. Our machines are engineered to effectively remove contaminants and restore the oil’s physical and chemical properties, ensuring that transformers operate reliably and efficiently. By choosing YUNENG for transformer oil regeneration, industries can enhance the longevity and performance of their electrical infrastructure, and reduce operational costs.