How to Choose the Right Vacuum Dehydration Oil Purification System?
Table of Contents
In the realm of power systems, the quality of insulation oil is paramount. It serves as a vital dielectric medium, preventing electrical breakdown and ensuring the smooth operation of transformers, circuit breakers, and other critical equipment. Over time, insulation oil can degrade due to factors such as oxidation, water ingress, and particulate contamination. This degradation can compromise the oil’s dielectric strength, leading to an increased risk of electrical faults and system failures.
To maintain optimal oil quality, vacuum dehydration oil purification systems are employed. These systems effectively remove moisture, dissolved gases, and solid impurities from the oil, restoring its insulating properties and extending its service life. However, selecting the right vacuum dehydration oil purification system is crucial to achieve the desired results. This article delves into the key factors and selection criteria to consider when choosing the optimal system for your power system.
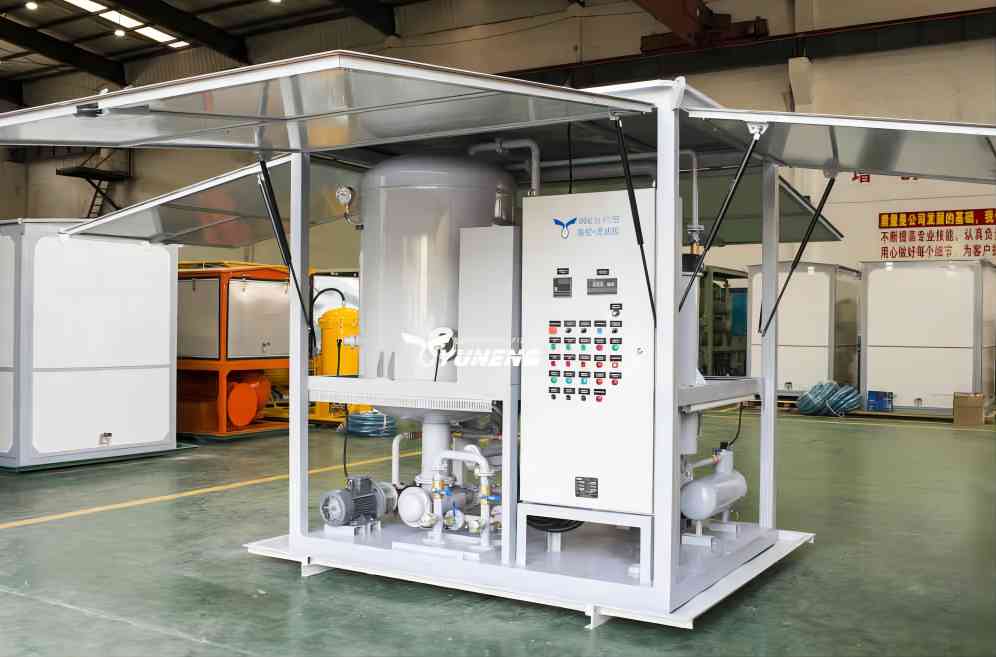
Part 1. What is Vacuum Dehydration Oil Purification System?
A vacuum dehydration oil purification system (VDOPS) is a specialized device used to purify and restore the quality of industrial oils by removing contaminants such as water, air, and solid particles. These contaminants are major contributors to oil degradation and equipment failure.
How Does a VDOPS Work?
The system uses a vacuum chamber to lower the boiling point of water, allowing it to evaporate at much lower temperatures. This process ensures that water and gas are efficiently separated from the oil without causing any thermal degradation. A series of fine filters also trap particulates, ensuring clean and purified oil exits the system.
Key Components of VDOPS:
- Vacuum Pump: This component creates the vacuum environment necessary for the dehydration process. It efficiently removes air and other gases from the system.
- Heater: The heater raises the oil’s temperature, increasing the vapor pressure of water and other volatile contaminants. This accelerates the evaporation process.
- Filter: The filter removes solid particles, such as dirt, metal particles, and other debris, from the oil. This prevents these contaminants from affecting the oil’s dielectric properties.
- Dehydrator: The dehydrator, often a molecular sieve or silica gel bed, absorbs water vapor from the oil. This final stage ensures that the oil is thoroughly dried.
Applications of VDOPS in Power Systems:
- Transformers: Maintaining dielectric strength of insulating oils.
- Turbines: Removing moisture and contaminants from turbine lubricants.
- Hydraulic Systems: Ensuring smooth operation by keeping hydraulic oil free of impurities.
- Gearboxes: Prolonging the life of lubricants and reducing wear on components.
By removing moisture, gases, and contaminants, VDOPS not only improves oil performance but also minimizes equipment downtime and repair costs, making it an essential tool for power systems.
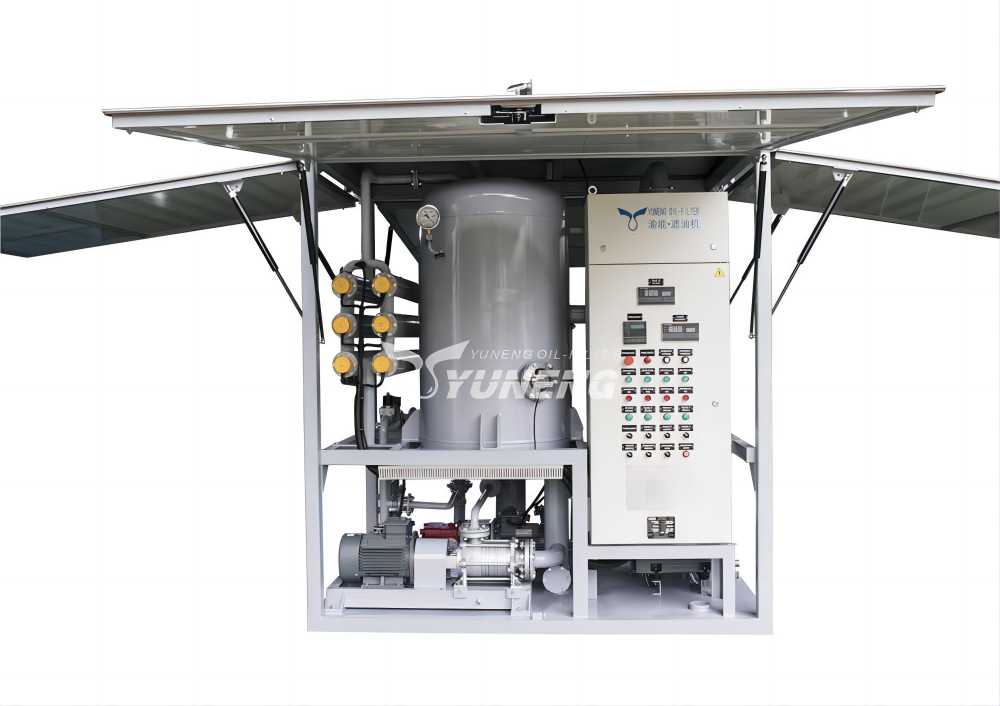
Part 2. Factors Affecting Vacuum Dehydration Oil Purification System Selection
Choosing the right VDOPS depends on several critical factors. Each system has unique specifications, and selecting the wrong one can lead to inefficient performance and wasted resources. Below are the key considerations when selecting a vacuum dehydration oil purification system:
1. Oil Quality Requirements
- Dielectric Strength: This is a critical parameter that measures the oil’s ability to withstand high voltage stress without breaking down. A higher dielectric strength indicates a superior insulating capability.
- Water Content: Moisture in the oil can significantly reduce its dielectric strength. Excessive water content can lead to increased electrical conductivity, causing arcing and potential equipment damage.
- Particle Content: Solid contaminants, such as dust, metal particles, and oxidation byproducts, can accelerate oil degradation and reduce its dielectric strength.
2. System Capacity
- Oil Volume: The volume of oil to be treated determines the required capacity of the purification system. A larger volume necessitates a system with higher throughput.
- Treatment Frequency: The frequency of oil purification depends on factors like the age of the oil, operating conditions, and environmental factors. More frequent treatment may require a system with a higher capacity or multiple systems.
3. Power Supply and Environmental Considerations
- Power Supply Requirements: The system’s power consumption and voltage requirements must be compatible with the available power supply.
- Environmental Impact: The system should comply with local and international environmental regulations, including noise and emissions standards. Factors like energy efficiency, waste minimization, and the use of environmentally friendly materials should be considered.
4. Operating Conditions
- Ambient Temperature and Humidity: The system’s performance can be affected by the ambient temperature and humidity. Extreme temperature and humidity conditions may require special considerations, such as temperature-controlled enclosures or additional cooling systems.
- Oil Temperature: The oil’s operating temperature influences the efficiency of the dehydration process. Higher temperatures can accelerate the evaporation of water and other volatile contaminants.
5. Maintenance and Operation Costs
- Initial Investment Cost: The initial cost of purchasing and installing the system, including equipment, installation, and commissioning.
- Operating Costs: Ongoing costs associated with the system’s operation, such as energy consumption, maintenance, replacement of consumables (filters, desiccant), and labor.
- Maintenance Requirements: The frequency and complexity of maintenance tasks, including cleaning, filter replacement, vacuum pump servicing, and system calibration. A system with lower maintenance requirements can reduce operational costs and downtime.
By carefully considering these factors, you can select a vacuum dehydration oil purification system that meets your specific needs and ensures the optimal performance and longevity of your power system.
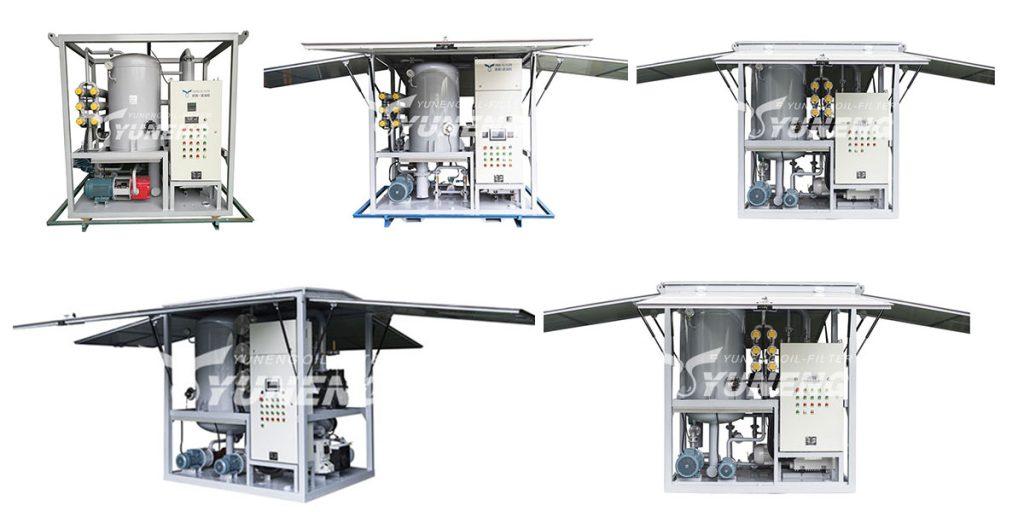
Part 3. How Do You Determine if the Vacuum Dehydration Oil Purification System is Qualified?
Selecting a system is only half the battle; you must also ensure it meets your performance expectations. Here are the steps to evaluate whether the system is qualified for your needs:
1. Technical Specifications
- Vacuum Pump Capacity: A high-capacity vacuum pump is crucial for ethe fficient removal of dissolved gases and moisture. The pump should be capable of achieving a high vacuum level, typically in the range of 1-10 Pa.
- Heater Power: The heater’s power rating determines the rate at which the oil can be heated, accelerating the evaporation of water and other volatile contaminants. A sufficient heating capacity is essential for effective dehydration.
- Filter Efficiency: The filter’s efficiency in removing solid particles is measured by its pore size and filtration media. A high-efficiency filter can remove particles as small as a few micrometers, ensuring the oil’s cleanliness.
- Dehydrator Capacity: The dehydrator’s capacity to absorb moisture is crucial for achieving the desired level of dryness. The dehydrator should be capable of handling the expected moisture load and regenerating efficiently.
2. Performance Testing
- Dielectric Strength Test: This test measures the oil’s ability to withstand high voltage stress without breaking down. After purification, the dielectric strength should be significantly improved, typically exceeding 70 kV/mm.
- Water Content Test: This test determines the amount of water present in the oil. The water content should be reduced to a very low level, ideally below 10 ppm (parts per million).
- Particle Count Test: This test measures the number and size of solid particles in the oil. After purification, the particle count should be significantly reduced, with a particle count of less than 10 particles/ml for particles larger than 10 micrometers.
3. Manufacturer’s Reputation and After-Sales Service
- Experience and Expertise: The manufacturer should have a strong track record in designing and manufacturing oil purification systems.
- Warranty and Maintenance Support: A comprehensive warranty and reliable after-sales service are essential for ensuring the long-term performance of the system.
By carefully evaluating these factors, you can select a vacuum dehydration oil purification system that meets your specific requirements and delivers the desired level of oil quality.
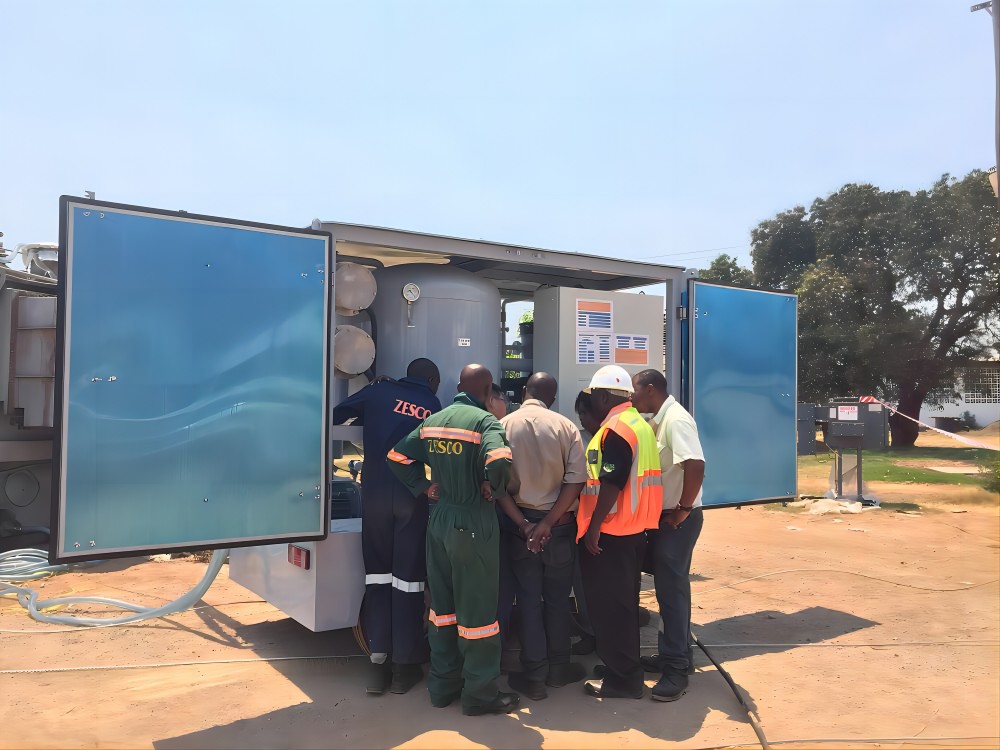
In Summary
By carefully considering the factors discussed in this article, you can select the right vacuum dehydration oil purification system to optimize the performance and lifespan of your power system. A well-chosen system will ensure that your insulation oil remains in top condition, minimizing the risk of electrical failures and maximizing the efficiency and reliability of your power equipment.
If you are seeking a reliable and high-performing solution, the Yuneng transformer oil dehydration machine is a recommended choice. Yuneng’s oil purifiers are known for their efficiency, robust design, and compliance with international standards, making them an excellent investment for maintaining clean and high-quality transformer oil. With Yuneng, you can ensure your power systems run smoothly and efficiently for years to come.