How to Determine If a Transformer Vacuum Pumping System Needs Replacement?
Table of Contents
Transformers, as the core equipment in the power system, undertake the important tasks of voltage transformation and power distribution. The stability and reliability of its operation are directly related to the safety and efficiency of the entire power grid. In the manufacturing and maintenance of transformers, the vacuum pumping system plays an indispensable role. It creates a vacuum environment to ensure the dryness of the internal insulation material of the transformer and the purity of the insulating oil, thereby ensuring the long-term stable operation of the transformer. This article will discuss in detail the functions of the transformer vacuum pump system, the criteria for evaluating whether it needs to be replaced, and recommendations for replacement.
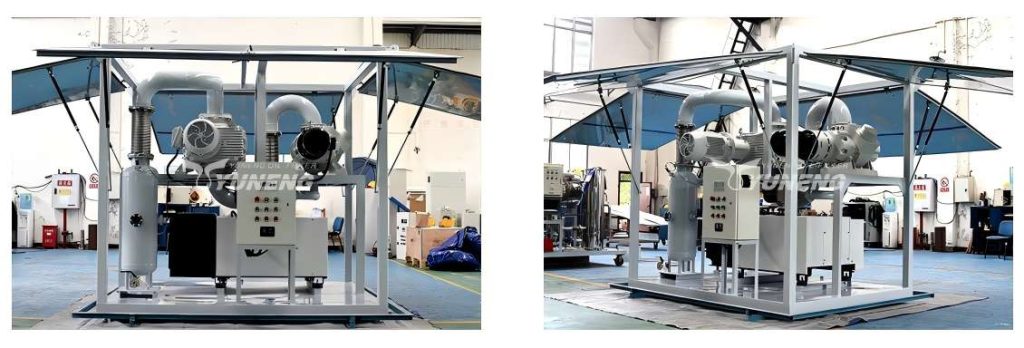
Functions of the Transformer Vacuum Pumping System
The primary function of a transformer vacuum pumping system is to extract moisture, air, and other gases from transformer oil. By reducing the content of dissolved gases in the oil, the system enhances the dielectric strength of the insulating oil, suppresses internal discharges, and prolongs the transformer’s operational life.
1. Vacuum Drying
In the manufacturing and maintenance of transformers, moisture, and gas in the insulating material are the main factors affecting its performance. Vacuum drying is to pump the inside of the transformer into a vacuum state through the vacuum pump system, thereby effectively removing moisture and gas from the insulating material. This process not only improves the electrical strength of the insulating material but also prolongs the service life of the transformer. Vacuum drying is usually carried out in the final stage of transformer manufacturing to ensure that the product reaches the best insulation state before leaving the factory.
2. Vacuum Oil Injection
The insulating oil inside the transformer not only plays an insulating role but also undertakes the functions of heat dissipation and arc extinguishing. Vacuum oil injection is to inject insulating oil into the transformer in a vacuum environment, eliminating air bubbles and impurities in the oil, and ensuring the purity and insulation performance of the oil. The vacuum pumping system maintains a stable vacuum degree during this process to ensure the smooth progress of the oil injection process, thereby improving the overall performance of the transformer.
3. Other Functions
In addition to vacuum drying and vacuum oil injection, the vacuum pumping system may also have other functions. For example, during the operation of the transformer, the vacuum pumping system can maintain the internal vacuum pressure and prevent the intrusion of external air and moisture. In addition, some advanced vacuum pumping systems are also equipped with fault alarm functions, which can monitor the operating status of the system in real time, and detect and deal with potential problems in time.
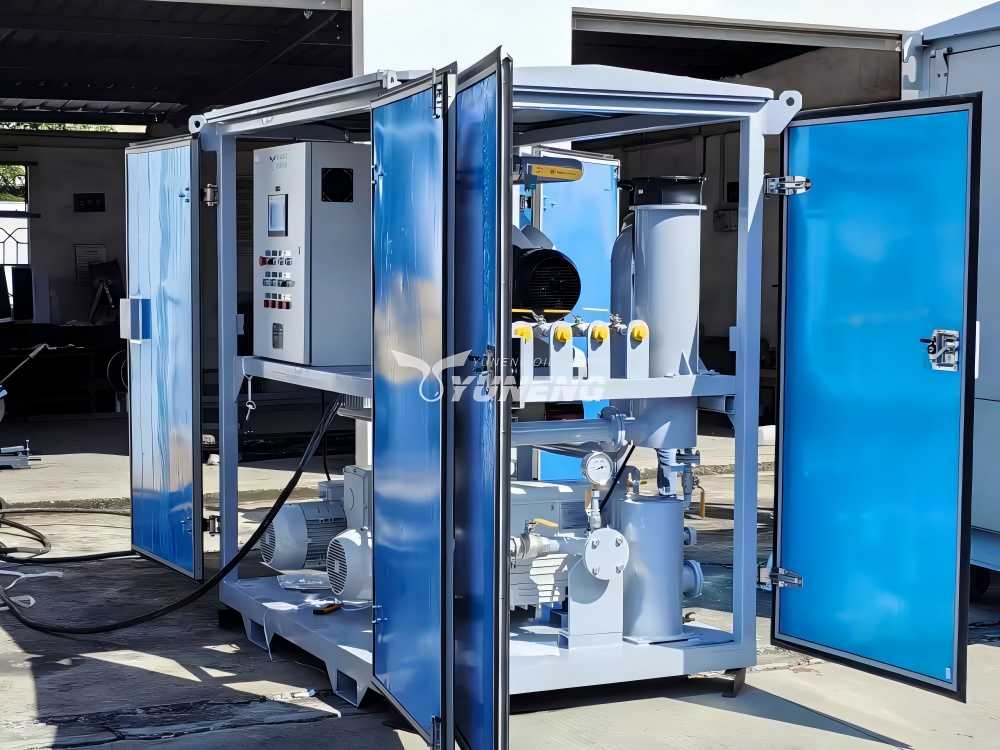
Evaluation Criteria for Replacing the Transformer Vacuum Pump
To determine whether the transformer vacuum pumping system requires replacement, several key factors must be considered:
1. Performance Degradation
The performance indicators of the vacuum pumping system are an important basis for evaluating whether it needs to be replaced. Key performance indicators include ultimate vacuum degree, pumping speed, noise level, etc. The ultimate vacuum degree refers to the lowest pressure that the vacuum pumping system can reach, and the pumping speed reflects the system’s ability to remove gas per unit time. With the aging of the equipment, these performance indicators will gradually decline. By regularly monitoring and recording these data, it can be judged whether the performance of the vacuum pumping system still meets the requirements.
2. Abnormal Operation
Abnormal operation is an early signal that the vacuum pumping system may be faulty. Common abnormal phenomena include abnormal noise, vibration, overheating, and oil leakage. Abnormal noise and vibration may indicate wear or loosening of internal parts of the equipment; overheating may be due to poor lubrication or failure of the cooling system; oil leakage will affect the sealing performance of the system. Once these abnormal phenomena are found, they should be checked and maintained in time, and consider replacing the equipment if necessary.
3. Increased Maintenance Costs
With the increase in the service life of the vacuum pumping system, the frequency and cost of maintenance will also gradually increase. Aging equipment requires more frequent maintenance and repair, and the cost of replacing parts will also increase. When the maintenance cost exceeds the value of the equipment itself, it becomes uneconomical to continue using the old vacuum pumping system. Therefore, the increase in maintenance cost is an important reference standard for evaluating whether the equipment needs to be replaced.
4. Service Life
The average service life of a vacuum pumping system is usually between 10 and 15 years, depending on the quality of the equipment and the environment of use. Although the service life is not the only evaluation criterion, the performance and reliability of equipment that has reached or exceeded the average service life will often decrease significantly. Therefore, when the equipment is close to or exceeds its service life, it should be combined with other evaluation criteria to comprehensively consider whether it needs to be replaced.

Recommendations for Vacuum Pumping System Replacement
Based on the above factors, replacement of the transformer vacuum pumping system is generally recommended under the following conditions:
1. Replacement Timing
According to the above evaluation criteria, it is recommended to consider replacing the vacuum pumping system in the following cases:
- The performance indicators have seriously declined and cannot meet the operating requirements of the transformer;
- Abnormal operation is frequent and affects the normal operation of the equipment;
- The maintenance cost is too high, exceeding the value of the equipment itself;
- The equipment has reached or exceeded its average service life.
Preventive maintenance is the key to avoiding losses caused by sudden equipment failures. Regularly assess the condition of the vacuum pump system and replace aging and performance-degraded equipment in a timely manner, which can effectively ensure the stable operation of the transformer.
2. Equipment Selection
When selecting a new vacuum pumping system, the following factors should be considered:
- Transformer capacity: Transformers of different capacities have different requirements for the vacuum pump system, and the appropriate model should be selected according to actual needs;
- Vacuum degree requirements: According to the insulation requirements and operating environment of the transformer, select equipment that can reach the required vacuum degree;
- Usage environment: Consider factors such as temperature, humidity, and dust at the equipment installation site, and choose products with strong adaptability and high reliability;
- Brand and after-sales service: Choose well-known brands and suppliers (such as Yuneng) with comprehensive after-sales service to ensure the quality of the equipment and subsequent maintenance support.
3. Replacement Process
The basic process of replacing the vacuum pumping system includes the following steps:
- Old equipment removal: Under the premise of ensuring safety, remove the old vacuum pump system and clean the installation position;
- New equipment installation: Install the new vacuum pump system in accordance with the equipment instructions and installation specifications, ensuring that all parts are firmly connected;
- Debugging and operation: Start the new equipment, carry out debugging and trial operation, and check whether various performance indicators are normal;
- Acceptance and recording: After the debugging is completed, carry out acceptance and record relevant data to ensure the normal operation of the equipment.
During the replacement process, attention should be paid to the following safety matters and operating specifications:
- Ensure that the power supply is disconnected to prevent electric shock accidents;
- Use appropriate tools and equipment to avoid damage to the equipment or personal injury;
- Strictly follow the equipment instructions and installation specifications to ensure installation quality.
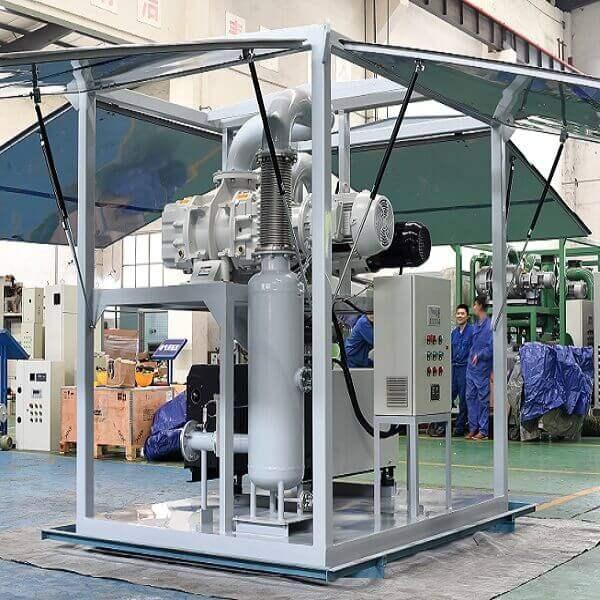
Summary
The transformer vacuum pump system plays a vital role in the manufacturing and operation of transformers. Through vacuum drying and vacuum oil injection, it ensures the dryness of the internal insulation material of the transformer and the purity of the insulating oil, thereby ensuring the long-term stable operation of the transformer. Regularly evaluating the condition of the vacuum pump system and replacing aging and performance-degraded equipment in a timely manner is the key to preventing equipment failures and ensuring the normal operation of the transformer.
With the continuous advancement of technology, future vacuum pumping systems will be more intelligent and energy-efficient. By adopting advanced control technologies and materials, the performance and reliability of vacuum pumping systems will be further improved, providing a more reliable guarantee for the safe operation of transformers.