How VDOPS Enhance Oil Quality Through Integrated Technologies
The vacuum dehydration oil purification system (VDOPS) is a cutting-edge technology that has revolutionized the oil treatment industry. By combining the principles of vacuum drying, separation engineering, coagulation, adsorption, and precision filtration, this system effectively removes moisture, gases, and impurities from oils, thereby enhancing their insulating properties and chemical stability. This article explores the intricate mechanisms behind this system and how it ensures the rapid and reliable purification of oil.
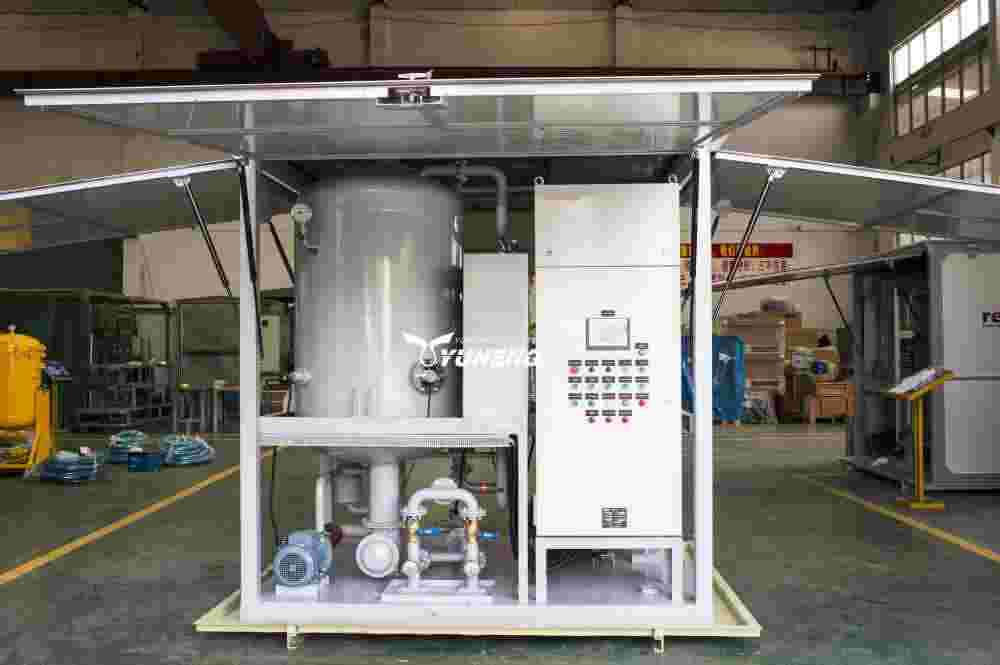
What Technologies are Integrated into the Vacuum Dehydration Oil Purification System?
1. Vacuum Drying Technology
Vacuum drying is a pivotal technology in the purification process. Under normal atmospheric pressure, water has a high boiling point, making it challenging to remove from the oil. However, in a vacuum environment, the boiling point of water is significantly reduced. This allows water to evaporate at much lower temperatures, minimizing the risk of thermal degradation of the oil.
The vacuum drying process involves the following steps:
- Heating: The oil is gently heated to accelerate the evaporation of water.
- Vacuum Application: A vacuum pump creates a low-pressure environment, further reducing the boiling point of water.
- Condensation: The evaporated water is condensed and collected for removal.
The primary advantage of vacuum drying is its efficiency in removing moisture without excessively heating the oil, which helps preserve its chemical stability and insulating properties.
2. Separation Engineering Technology
Separation engineering plays a critical role in effectively removing water, gas, and solid impurities from oil. This process can involve several methods:
- Centrifugal Separation: Utilizes centrifugal force to separate heavier water and solid contaminants from the lighter oil.
- Coalescence: Combines small water droplets into larger droplets that can be more easily separated from the oil.
- Gravity Separation: Relies on gravity to allow contaminants to settle out of the oil.
These separation methods work in conjunction to ensure that contaminants are effectively removed, thereby enhancing the overall purity and performance of the oil.
3. Coalescence Technology
Coalescence technology focuses on the removal of water droplets from the oil. This process involves the use of coalescing filters that cause small water droplets to merge into larger droplets. Once the droplets reach a sufficient size, they can be easily separated from the oil using gravity or centrifugal force.
The coalescence process offers several benefits:
- Improved Water Removal: By merging small droplets into larger ones, coalescence technology enhances the efficiency of water removal.
- Reduced Maintenance: Effective water removal helps prevent the formation of sludge and reduces the frequency of filter changes.
Integrating coalescence technology with other purification methods ensures a comprehensive approach to contaminant removal, improving the overall effectiveness of the system.
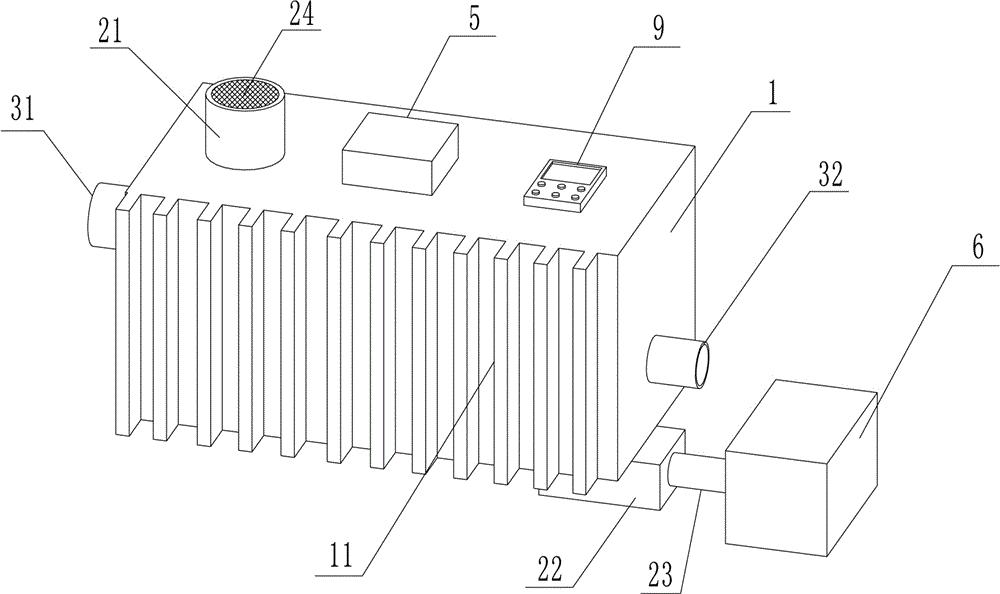
4. Adsorption Technology
Adsorption technology involves using adsorbents to attract and remove contaminants from the oil. Adsorbents are materials that can bind with impurities, effectively removing them from the oil. Common adsorbents used in oil purification include activated carbon, silica gel, and alumina.
The adsorption process works as follows:
- Contact: The oil passes through a bed of adsorbent material.
- Binding: Contaminants in the oil bind to the adsorbent material.
- Removal: The adsorbent material is then removed and replaced as needed.
Adsorption technology is particularly effective at removing trace contaminants and can significantly enhance the purity of the oil, contributing to improved insulation performance and chemical stability.
5. Precision Filtration Technology
Precision filtration is a critical component of oil purification systems. It involves using filters with very fine mesh sizes to capture small particles and impurities that other methods might miss. This technology ensures that even the smallest contaminants are removed, which is essential for maintaining the high performance of the oil.
Key aspects of precision filtration include:
- Filter Types: Various filter types, such as depth filters, membrane filters, and cartridge filters, can be used depending on the specific needs of the oil.
- Filter Efficiency: The effectiveness of the filtration process is determined by the filter’s ability to capture particles of different sizes.
By incorporating precision filtration into the oil purification process, these systems can achieve a high level of oil cleanliness, which is crucial for preventing equipment failure and extending operational life.
How Integrated Technologies of VDOPS Impact Oil Quality
The enhanced purification achieved through these integrated technologies has a profound impact on oil quality:
- Insulation Performance: Clean oil with reduced moisture and contaminants maintains its insulating properties, preventing electrical failures and enhancing the performance of electrical equipment.
- Chemical Stability: The removal of contaminants helps maintain the chemical stability of the oil, reducing the risk of degradation and prolonging its lifespan.
- Operational Benefits: Improved oil quality leads to fewer maintenance requirements, reduced downtime, and increased efficiency in industrial operations.
For more information about VDOPS integrated technologies, or looking for a VDOPS manufacturer in China, Yuneng is a good choice for you. Welcome to contact us at any time, and we will return to you within 24H.