Lube Oil Purifiers: Purification Technologies and Selecting Method You Need to Know
In the complex world of industrial machinery and engines, lubrication plays a vital role in ensuring smooth operation and longevity. However, with usage comes the inevitable generation of waste lubricating oil, presenting environmental challenges. To address this issue, lube oil purifiers emerge as essential components in the recycling process, offering an efficient means to reclaim and reuse oil, minimizing environmental impact. This article delves into the multifaceted landscape of lube oil purifiers, exploring their roles, types, and selection criteria, and recommending Yuneng’s JT Series as a cutting-edge solution.
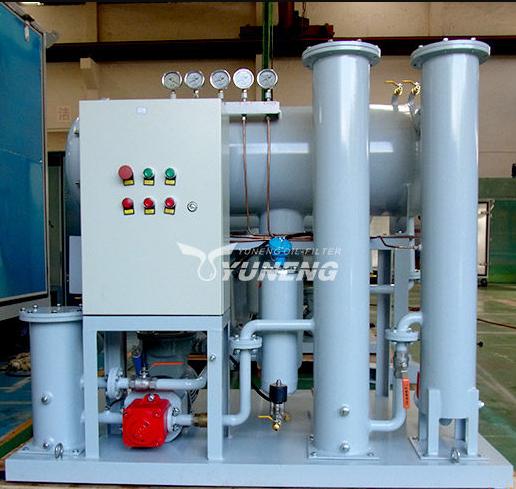
The Role of a Lube Oil Purifier Machine in Waste Lube Oil Recycling
1. The Purpose of Lube Oil Purification
Lubrication oil purifiers, also known as oil cleaning systems, are specialized machines designed to remove contaminants from used lubricating oil. As engines and machinery operate, lubricating oil becomes contaminated with impurities such as dirt, metal particles, and oxidation by-products. The primary purpose of lube oil purification is to restore the oil to a usable state, extending its lifespan and reducing the need for new oil production. To neutralize the insidious effects of operational wear and tear, extracting contaminants like:
- Particulate Invaders: Microscopic foes such as soot, metal fragments, and combustion residues infiltrate oil, accelerating wear and tear in machinery. Lube oil purifiers are adept at exorcising these particulate demons through various filtration methods.
- Water Woes: The infiltration of water is a double whammy, compromising lubrication properties and promoting rust. Purification processes like vacuum dehydration evict this unwelcome guest, ensuring oil remains a potent ally against friction.
- Hydrocarbon Heretics: Unburnt fuel residues lurk within used oil, hindering efficiency and contributing to emissions. Lube oil purifiers employ sophisticated methods to vanquish these hydrocarbon heretics, restoring the oil’s purity and environmental virtue.
- Oxidation’s Corrosive Clutches: As oil ages, it succumbs to oxidation, forming byproducts that thicken it and diminish its performance. Purification processes like chemical treatment counteract this oxidative assault, revitalizing the oil’s youthful vigor.
2. Environmental Impact and Importance of Recycling Lube Oil
The environmental consequences of improper disposal of used lubricating oil are significant. It can contaminate soil, water, and air, posing risks to ecosystems and human health. Lube oil purifiers emerge as powerful tools in combating these challenges by:
- Neutralizing Contaminant Threats: By removing harmful elements like heavy metals and organic compounds, lube oil purifiers safeguard the environment from ULO’s toxic touch.
- Resource Conservation: Every drop of recycled oil represents a victory for resource conservation. Lube oil purifiers breathe new life into used oil, reducing dependence on virgin oil extraction and its associated environmental footprint.
- Circular Economy: By closing the loop on the oil life cycle, lube oil purifiers champion sustainability principles, paving the way for a future where resources are cherished and waste is minimized.
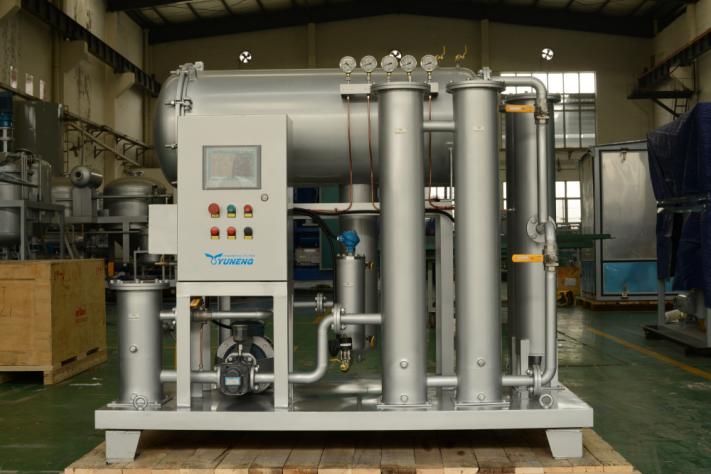
Types of Lubrication Oil Purifiers
Lubrication oil purifiers are essential equipment for maintaining the integrity and performance of lubricants in various industrial applications. These machines employ diverse mechanisms to remove contaminants and extend the lifespan of lubricating oils, ultimately leading to increased equipment efficiency and cost savings. Here’s a detailed breakdown of the primary types of lubrication oil purifiers:
A. Vacuum Separation System
- Mechanism: The vacuum separation system employs a combination of heat and reduced pressure (vacuum) to separate oil from impurities. The lower pressure allows the oil to vaporize at lower temperatures, facilitating the separation of contaminants with higher boiling points.
- Applications: Vacuum separation is highly effective in removing volatile contaminants, oxidation products, and dissolved gases, making it suitable for purifying oils used in high-temperature environments or sensitive equipment.
- Limitations: Vacuum separation units can be complex and energy-intensive, requiring specialized operation and maintenance.
B. Adsorption Filters
- Mechanism: Adsorption filters utilize porous materials like activated clay, alumina, or silica gel to capture impurities through a process called adsorption. The porous structure of these materials provides a large surface area for contaminant molecules to adhere to, allowing clean oil to pass through.
- Applications: Adsorption filters are adept at removing finer particles, polar contaminants, and some dissolved impurities, making them suitable for applications requiring high cleanliness levels, such as turbine oils and compressor lubricants.
- Limitations: The effectiveness of adsorption filters can be affected by the type and concentration of contaminants present in the oil. Additionally, the adsorbent material needs periodic regeneration or replacement.
C. Membrane Filtration Systems
- Mechanism: Membrane filtration systems employ semi-permeable membranes with microscopic pores that allow only oil molecules to pass through while rejecting larger contaminants and dissolved impurities. This precise separation process ensures exceptional oil purity.
- Applications: Membrane filtration is ideal for applications demanding the highest level of cleanliness, such as medical equipment, food processing machinery, and sensitive electronic components.
- Limitations: Membrane filtration systems can be susceptible to clogging by certain contaminants and require regular maintenance to maintain optimal performance.
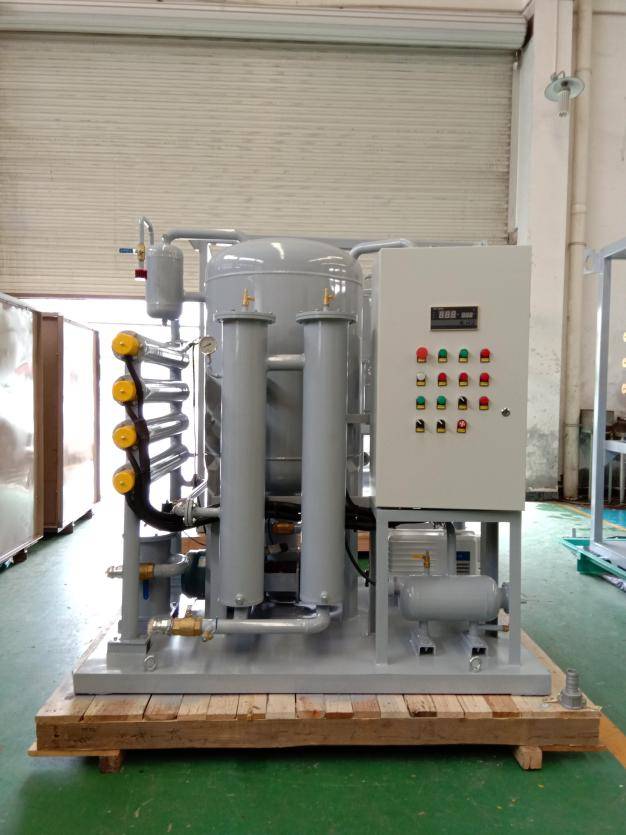
How to Choose the Right Lubrication Oil Purifier?
Selecting the optimal lubrication oil purifier necessitates a comprehensive evaluation of various factors that influence its effectiveness and compatibility within your specific industrial context. Here’s a more detailed breakdown of crucial considerations:
1. Oil Properties and Contaminant Characteristics
- Oil Viscosity: Different purifiers are designed for varying viscosities. Ensure the chosen purifier can handle the viscosity range of the specific lubricant you intend to process. Mismatched viscosities can lead to inefficient separation and potential damage to the equipment.
- Contaminant Type and Size: Identify the dominant types and sizes of contaminants present in your used oil. Choose a purifier equipped with a filtration mechanism adept at removing the targeted contaminants. For instance, centrifugal separators excel at large particles, while membrane filtration tackles finer impurities at the molecular level.
2. Process Capacity and Throughput
- Oil Volume: Assess the typical volume of used oil requiring purification at regular intervals. Select a purifier with sufficient capacity to handle your processing needs without frequent interruptions. Overloading the purifier can compromise its efficiency and shorten its lifespan.
- Desired Purification Rate: Consider the desired processing speed for your operations. Some applications necessitate rapid turnaround times, while others prioritize thorough purification over speed. Choose a purifier with a flow rate that aligns with your desired throughput.
3. Operational Efficiency and Sustainability
- Energy Consumption: Evaluate the energy consumption of different purifier models. Selecting an energy-efficient machine translates to reduced operational costs and aligns with green initiatives within your organization. Explore options like variable-speed drives or automatic shut-off features to optimize energy usage.
- Maintenance Requirements: Investigate the routine maintenance schedule and associated costs for each purifier option. Choose a machine with readily available spare parts and user-friendly maintenance procedures to minimize downtime and maintenance expenses.
4. Cost-Effectiveness and Long-Term Value
- Initial Investment: Compare the upfront purchase costs of different purifier models against their respective capabilities and features. Consider the total cost of ownership over the expected lifespan, including maintenance costs, energy consumption, and potential resale value when making your decision.
- Return on Investment (ROI): Analyze the potential cost savings gained from extended oil life, reduced equipment downtime, and improved operational efficiency. Choose a purifier that demonstrably contributes to a positive ROI within your specific application context.
By meticulously evaluating these considerations, you can select the lubrication oil purifier that best aligns with your operational needs, technical requirements, and long-term financial objectives. Remember, the optimal choice hinges on finding the perfect balance between effectiveness, efficiency, and cost-effectiveness for your specific industrial application.
Conclusion
In conclusion, the comprehensive exploration of lube oil purifiers in waste lubricating oil recycling underscores their indispensable role in promoting sustainability. With an array of types available and critical considerations for selection, users can make informed choices aligned with their specific needs. Yuneng’s JT Series emerges as a distinguished solution, exemplifying the intersection of technological innovation, environmental responsibility, and industrial efficiency. As industries continue to embrace sustainable practices, the adoption of advanced lube oil purifiers becomes an integral part of responsible waste management and resource conservation.