Maintenance Measures for Transformer Oil Filter Machines During Shutdown
Transformer oil filter machines play a crucial role in maintaining the efficiency and longevity of transformers by filtering out impurities and moisture from the insulating oil. However, during periods of inactivity or shutdown, special maintenance measures are necessary to ensure these machines remain in optimal condition. Proper maintenance during downtime not only preserves the equipment but also guarantees safe and efficient operation when it is time to restart. This article outlines comprehensive maintenance steps that should be undertaken to protect transformer oil filter machines during shutdown periods.
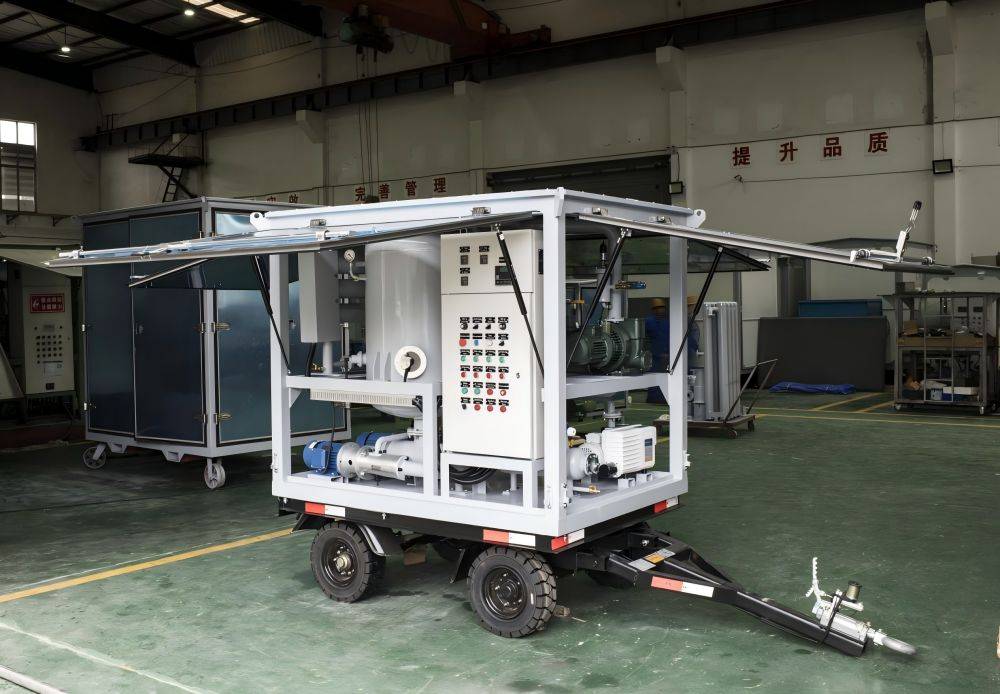
Special Maintenance Measures During Shutdown
Regular maintenance is crucial for preserving the condition of a transformer oil filter machine. When a shutdown occurs, specific maintenance measures should be implemented to prepare the equipment for subsequent operation.
1. Cleaning and Maintenance
Thorough cleaning is the cornerstone of maintenance during a shutdown. Transformer oil filter machines accumulate oil, moisture, and debris over time, which can lead to corrosion and other issues if not addressed.
- Thorough Cleaning of the Equipment: Cleaning should start with the filter plates and filter cloths. These components are directly involved in the filtration process and can harbor residues that impair performance. Using appropriate cleaning agents, all traces of oil and impurities should be removed.
- Cleaning the Hydraulic System: The hydraulic system, essential for the operation of the filter machine, must also be meticulously cleaned. Hydraulic lines, valves, and reservoirs should be flushed and cleaned to remove any contaminants. Ensuring all components are free from oil, moisture, and debris is critical. After cleaning, it is vital to ensure all parts are thoroughly dried to prevent moisture-related issues.
2. Anti-Corrosion Treatment
Metal components of the transformer oil filter machine are prone to rust and corrosion, especially during prolonged periods of inactivity. Applying anti-corrosion treatments can significantly extend the lifespan of these components.
Application of Anti-Corrosion Agents
Anti-corrosion agents, such as rust inhibitors or protective coatings, should be applied to all metal surfaces. These agents form a protective layer that prevents moisture and oxygen from reaching the metal, thereby preventing rust and corrosion. This step is particularly crucial for machines that will be inactive for extended periods.
3. Electrical System Inspection and Maintenance
The electrical system is a critical aspect of the transformer oil filter machine, and it must be thoroughly inspected and maintained during shutdown.
- Checking Electrical Connections: All electrical connections should be inspected to ensure they are secure and free from corrosion or damage. Loose or corroded connections can lead to malfunctions or even hazardous situations.
- Inspecting the Control System: The control system, including the control panel, buttons, switches, and displays, should be checked for proper functionality. Any faults or indications of wear should be addressed immediately.
- Verifying Protective Devices: Protective devices such as overload and short-circuit protection must be tested to ensure they are functioning correctly. These devices are crucial for preventing damage to the machine during operation.
- Inspecting Motors and Pumps: The condition of motors and pumps should be evaluated, focusing on bearings, seals, and rotating parts. Any unusual noises or vibrations should be investigated and resolved.
- Electrical Insulation Testing: Electrical insulation should be tested using appropriate instruments to ensure there are no leakage risks. Proper insulation is vital for safe operation.
- Checking Batteries and Backup Power: Batteries and backup power systems, including emergency stop buttons, should be checked to ensure they function correctly. These systems are essential for safely shutting down the machine in case of power failure.
- Ensuring Grounding System Integrity: The grounding system should be inspected to ensure it is secure and functioning correctly, providing a safe path for electrical faults.
- Inspecting Sensors and Instruments: All sensors and instruments should be tested for accuracy and functionality. Any damaged or uncalibrated components should be repaired or replaced.
- Maintaining Electrical Cabinets and Control Rooms: Electrical cabinets and control rooms should be kept clean, dry, and free from dust and moisture. Proper ventilation should be ensured to prevent overheating.
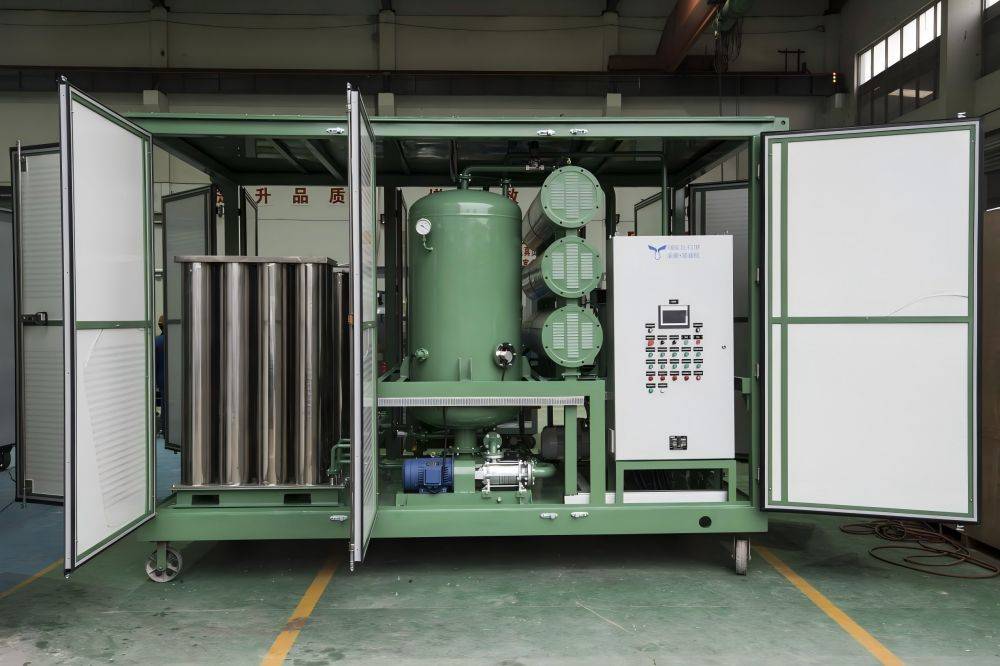
4. Proper Storage Methods
Proper storage of the transformer oil filter machine is essential to prevent damage during shutdown.
- Selecting Appropriate Storage Methods: The machine should be stored in a vertical position if possible and covered with waterproof cloth or plastic film to protect against dust and moisture.
- Ensuring a Dry, Well-Ventilated Storage Environment: The storage area should be dry, well-ventilated, and free from direct sunlight. Monitoring environmental conditions, such as temperature and humidity, can help maintain an optimal storage environment.
5. Preventing Moisture Ingress
Moisture is a significant threat to the transformer oil filter machine during shutdown. Steps must be taken to prevent its ingress.
- Cleaning Equipment Inside and Out: Before the shutdown, the machine should be thoroughly cleaned inside and out to minimize the chance of moisture absorption.
- Applying Moisture Inhibitors: Moisture inhibitors can be applied to the machine’s exterior to create a protective barrier.
- Using Desiccants: Desiccants, such as silica gel, can be placed near the machine to absorb excess moisture.
- Sealing Ventilation Ports and Seams: Sealing materials or other methods should be used to close ventilation ports and seams, preventing moisture from entering the machine.
- Regular Humidity Monitoring: Humidity levels should be monitored regularly to ensure the effectiveness of moisture prevention measures.
- Protecting the Electrical System: Control cabinet doors and valves should be closed to prevent moisture ingress into the electrical system.
- Rust Prevention Treatment: Anti-rust grease can be applied to metal parts to prevent rust formation.
- Covering the Equipment Body: Covering the machine with a protective layer prevents dust and moisture from contacting the equipment surface.
- Checking Sealing Effectiveness: Before final storage, all sealing measures should be checked to ensure there are no leaks.
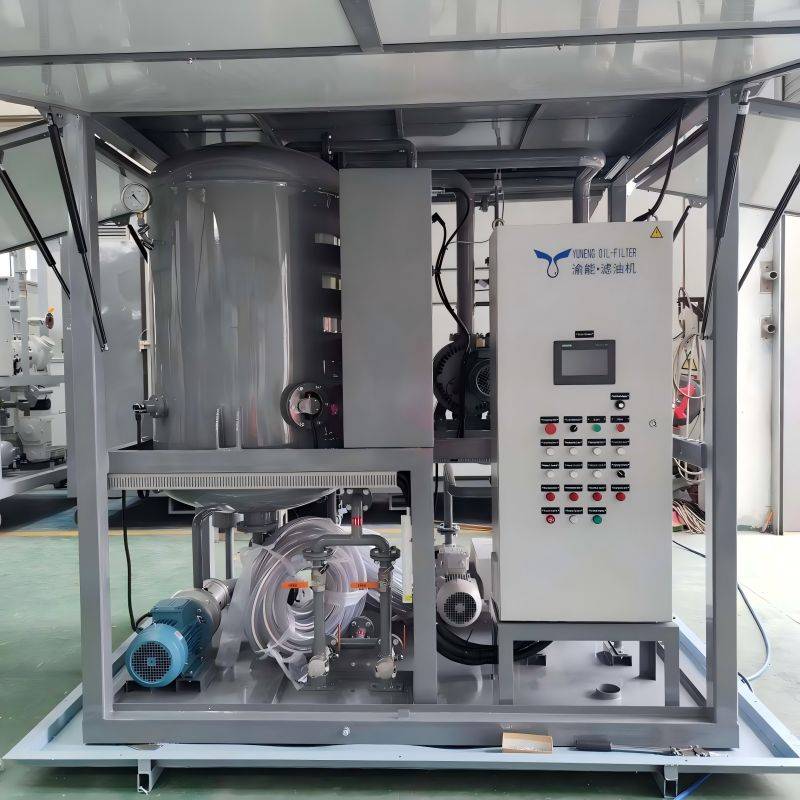
6. Preventing Metal Part Rust and Corrosion
To prevent rust and corrosion of metal parts during long-term shutdown, several steps can be taken.
- Cleaning and Drying Equipment Thoroughly: Ensuring the equipment is clean and dry before shutdown is essential. Moisture is a primary cause of metal corrosion.
- Applying Anti-Rust Coatings: Anti-rust coatings, such as paint or wax, can be applied to metal surfaces to create a protective barrier.
- Using Corrosion Inhibitors: Corrosion inhibitors can form a protective film on metal surfaces, preventing corrosion. These can be particularly effective in closed environments.
- Sealing Storage: Sealing the machine with plastic film or other materials prevents air and moisture from entering and causing corrosion.
- Regular Inspection: Periodic inspections during the shutdown can help identify and address potential corrosion issues early.
7. Maintenance Records
Maintaining detailed records of all maintenance activities during the shutdown is essential for tracking the history and ensuring continuity.
- Documenting Maintenance Activities: All cleaning, inspection, and part replacement activities should be documented thoroughly. This documentation helps in tracking maintenance history and planning future activities.
8. Regular Inspection
Even during shutdown, regular inspections are crucial to ensure the continued effectiveness of maintenance measures.
- Regular checks can identify potential issues early, allowing for timely resolution. Ensuring the effectiveness of anti-corrosion measures and other protective steps is vital.
9. Additional Considerations for Long-Term Shutdown
- Oil Condition: The condition of the oil should be assessed before shutdown. Contaminated or degraded oil can accelerate corrosion. Oil replacement might be necessary.
- Component Removal: For extended shutdowns, consider removing critical components and storing them separately in a controlled environment.
- Professional Consultation: Seeking expert advice from the transformer oil purifier manufacturer or corrosion specialist can provide tailored guidance based on specific equipment characteristics and operating conditions.
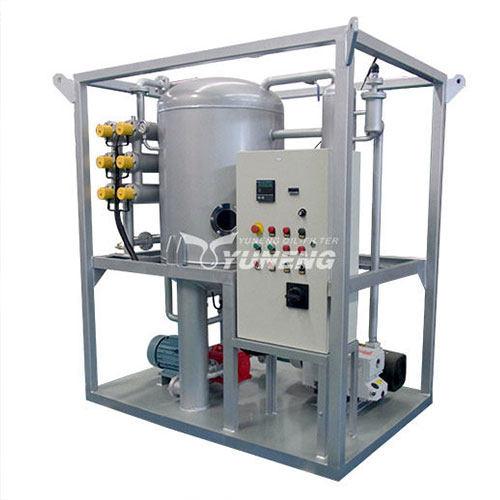
Conclusion
Proper maintenance during the shutdown of transformer oil filter machines is essential to protect the equipment and ensure its readiness for the next startup. By following the outlined steps for cleaning, anti-corrosion treatment, electrical system inspection, proper storage, and regular inspection, the longevity and efficiency of these machines can be preserved. Implementing these measures not only reduces the risk of damage during downtime but also ensures that the machine can be safely and effectively restarted, maintaining the reliability of the transformers they serve.