Problem of Gases in Transformer Oil and How to Solve It
Table of Contents
Transformers are critical components in power distribution systems. However, one significant issue that can compromise their reliability and efficiency is the formation of gases in transformer oil. These gases, if not properly managed, can lead to significant operational issues and even failure of the transformer.
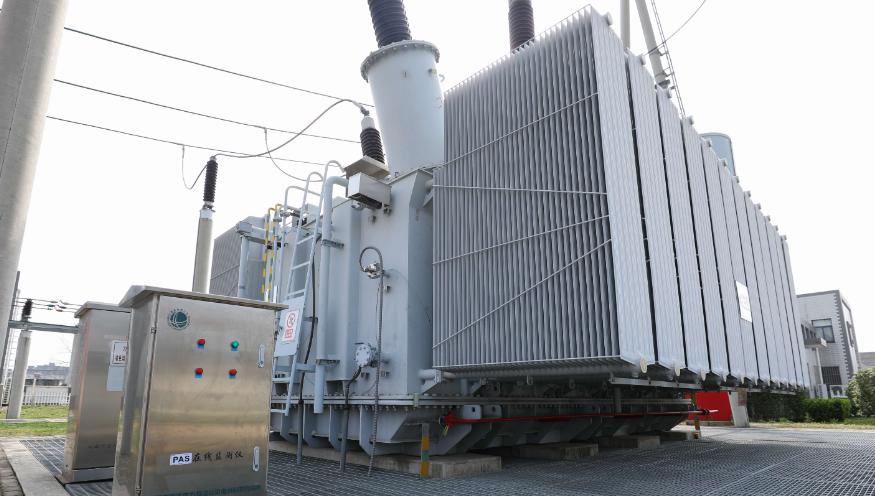
What are the Gases in Transformer Oil
Gases in transformer oil primarily result from thermal and electrical stress on the oil, leading to its decomposition. The identification and quantification of these gases are vital for assessing the condition of the transformer and predicting potential failures.
Types of Gases in Transformer Oil
The gases in transformer oil can be categorized into several key types:
- Hydrogen (H₂): Often one of the first gases detected, hydrogen is produced by low-energy electrical faults or partial discharges, and its presence can indicate the early stages of oil degradation.
- Methane (CH₄): Methane is typically formed alongside hydrogen, originating from minor overheating of the oil, often from hotspots within the transformer.
- Ethylene (C₂H₄) and Ethane (C₂H₆): These gases result from moderate to severe overheating of the oil, especially when the temperature exceeds 500°C. Ethylene is a strong indicator of insulation deterioration due to excessive heat.
- Acetylene (C₂H₂): Acetylene is primarily produced during arcing or electrical discharges and suggests serious faults within the transformer.
- Carbon Dioxide (CO₂) and Carbon Monoxide (CO): These gases are formed by the degradation of cellulose-based materials, such as paper insulation, indicating thermal stress on the solid insulation.
By identifying the types of gases and their concentrations, operators can diagnose specific issues and take timely corrective actions.
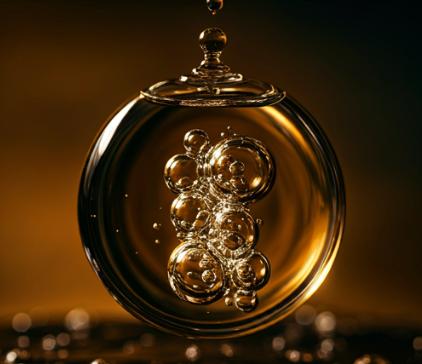
Causes and Sources of Gas Formation
Gas formation in transformer oil arises from several key factors, primarily related to thermal, electrical, and chemical stresses.
- Thermal Stress: When a transformer operates under high load or experiences inadequate cooling, it generates excessive heat. This heat causes the transformer oil to decompose, producing gases such as methane (CH₄), ethylene (C₂H₄), and hydrogen (H₂). Over time, continued thermal stress can lead to the formation of larger quantities of gas, signaling potential overheating or hotspots within the transformer.
- Electrical Stress: Electrical discharges like partial discharges, arcing, or sparking can cause localized intense heating. This results in the breakdown of oil and insulation materials, producing gases like acetylene (C₂H₂) and ethylene. Arcing, in particular, produces acetylene, which is a red flag for severe electrical stress.
- Oxidation and Moisture: Oxygen and water infiltrating the transformer oil can accelerate the breakdown of both the oil and insulation, forming gases such as carbon dioxide (CO₂) and carbon monoxide (CO). These gases often indicate insulation degradation or the presence of moisture, both of which compromise the transformer’s longevity.
Impact of Gases on Transformer Performance
The presence of gases in transformer oil can have a profound impact on the overall performance and reliability of transformers, which are vital components in electrical distribution systems.
- Decreased Insulating Properties: When gases form bubbles within the transformer oil, they diminish its dielectric strength, which is crucial for maintaining effective electrical insulation. This reduction in insulating capability can lead to electrical discharges and arcing, ultimately resulting in transformer failures or damage to connected equipment.
- Reduced Cooling Efficiency: Additionally, gas accumulation within the oil interferes with its thermal conductivity, impairing the oil’s ability to transfer heat away from critical components such as windings and cores. This inefficiency can lead to localized overheating, which may accelerate insulation degradation and shorten the lifespan of the transformer.
- Predictive Maintenance Issues: Furthermore, the accumulation of gases often signifies underlying problems, such as insulation breakdown or mechanical failures. Therefore, regular gas analysis is essential for predictive maintenance, allowing operators to identify potential issues early and take timely corrective actions, ultimately enhancing the reliability and efficiency of transformer operations.
Importance of Gas Analysis in Transformer Maintenance
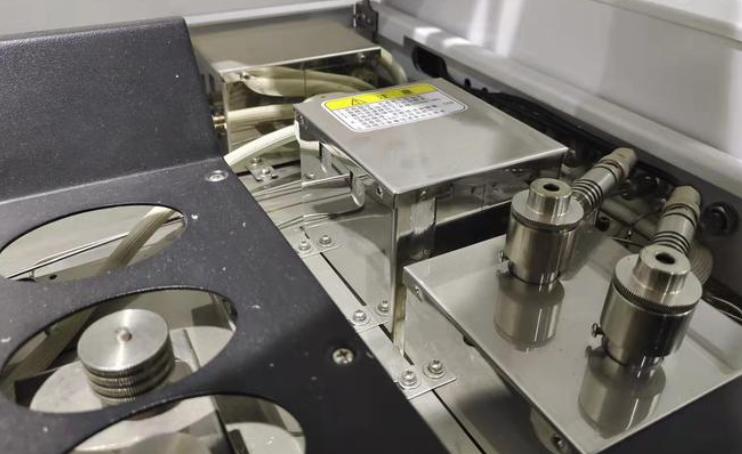
Regular gas analysis is a critical component of transformer maintenance, playing a vital role in ensuring the reliability and efficiency of transformers. By conducting dissolved gas analysis (DGA), technicians can monitor the types and concentrations of gases present in the oil, which serve as indicators of the transformer’s health. The importance of gas analysis can be highlighted through several key points:
- Early Detection of Incipient Failures: Gas analysis enables the identification of gas trends, signaling potential problems before they escalate. This proactive approach allows for timely interventions, reducing the risk of catastrophic failures.
- Assessment of Operating Conditions: By analyzing gas compositions, operators can gain insights into the operating conditions of the transformer. Unusual gas levels can indicate overheating or electrical faults, prompting necessary adjustments in load or cooling methods.
- Maintenance Planning: Understanding the gas formation patterns can help develop a comprehensive maintenance schedule. Regular analysis ensures that any emerging issues are addressed promptly, enhancing the longevity of the transformer.
- Enhanced Safety: Gas accumulation can pose safety risks, including the potential for explosive conditions. Regular monitoring allows for the identification of hazardous gas levels, ensuring that safety measures are in place.
Overall, gas analysis is an indispensable tool in transformer maintenance, providing critical information that supports informed decision-making and helps maintain operational integrity.
Solving the Problem: Transformer Oil Purification
To effectively manage the issue of gas accumulation in transformer oil, implementing a robust purification process is essential. Transformer oil purification not only addresses the immediate problems associated with gas formation but also contributes to the long-term health and reliability of the transformer.
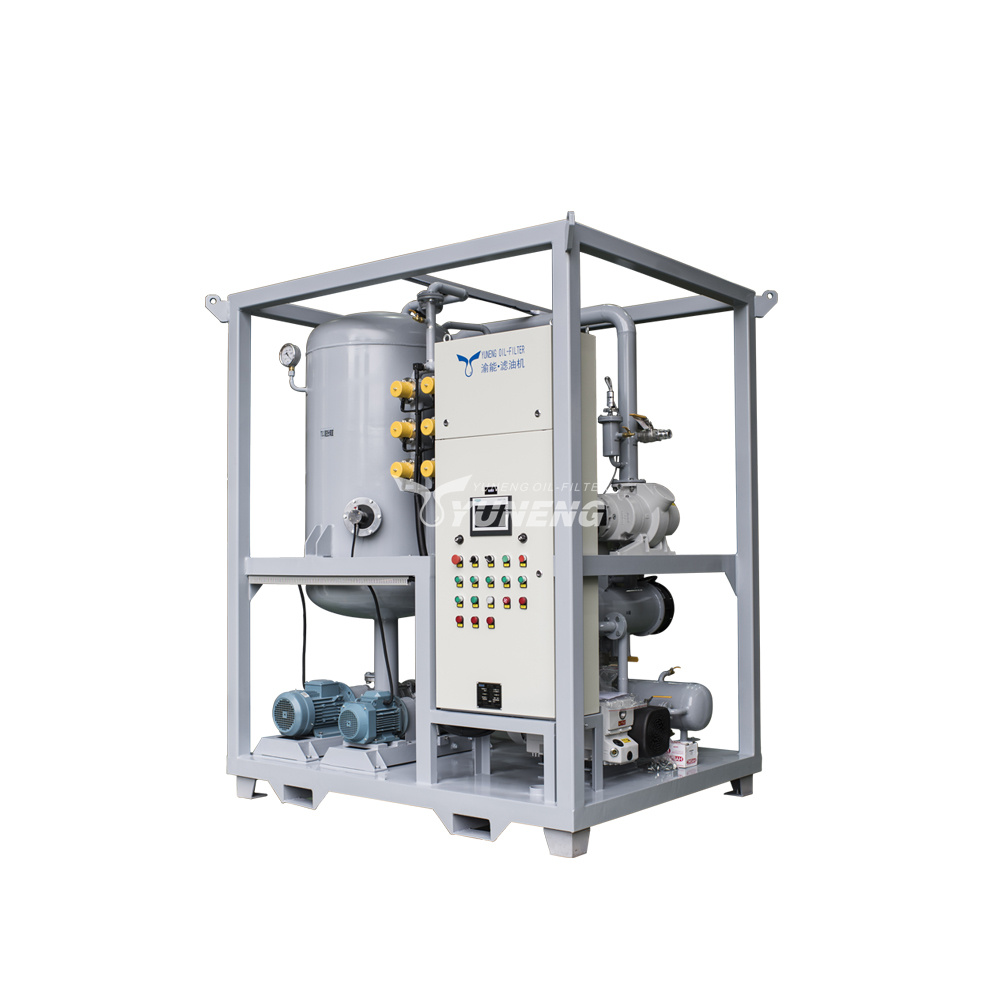
Role of Transformer Oil Filter Machines
Transformer oil filter machines are specifically designed to purify the oil, ensuring it meets the required specifications for optimal performance. These machines typically operate through several key processes:
- Vacuum Degasification: One of the primary methods used in transformer oil filtration is vacuum degasification. This process involves creating a vacuum environment that lowers the boiling point of dissolved gases, allowing them to escape from the oil. By efficiently removing gases such as hydrogen, methane, and acetylene, the dielectric strength of the oil is restored, significantly reducing the risk of electrical failures.
- Particle Filtration: In addition to gas removal, transformer oil filter machines are equipped with advanced filtration systems that eliminate solid contaminants and particulates. These impurities can lead to increased wear on transformer components and may contribute to further gas formation. By maintaining oil cleanliness, the machines help enhance the overall performance and longevity of the transformer.
- Moisture Removal: Moisture is a critical factor that accelerates the decomposition of transformer oil and the generation of gases. Many purification systems incorporate moisture removal capabilities, such as adsorption or distillation techniques. By reducing the water content in the oil, the chances of gas formation are minimized, thereby improving the insulating properties of the oil.
Regular use of transformer oil filter machines is a proactive measure that not only solves existing gas problems but also helps prevent future issues.
In summary, the presence of gases in transformer oil poses significant challenges that can impact the efficiency and reliability of transformers. Implementing transformer oil purification through advanced filter machines addresses these challenges by removing dissolved gases, solid particulates, and moisture. This comprehensive approach not only enhances the insulating properties of the oil but also ensures the long-term performance and reliability of transformers.