SF6 Gas Filling Equipment for Circuit Breakers
SF6 (sulfur hexafluoride) gas plays a crucial role in the functioning of circuit breakers, serving as an excellent insulating medium to extinguish electrical arcs. Proper filling of SF6 gas is essential for maintaining the integrity and efficiency of circuit breakers. This article explores the evolution of SF6 gas filling equipment and kits, highlighting their significance in modern industrial applications.
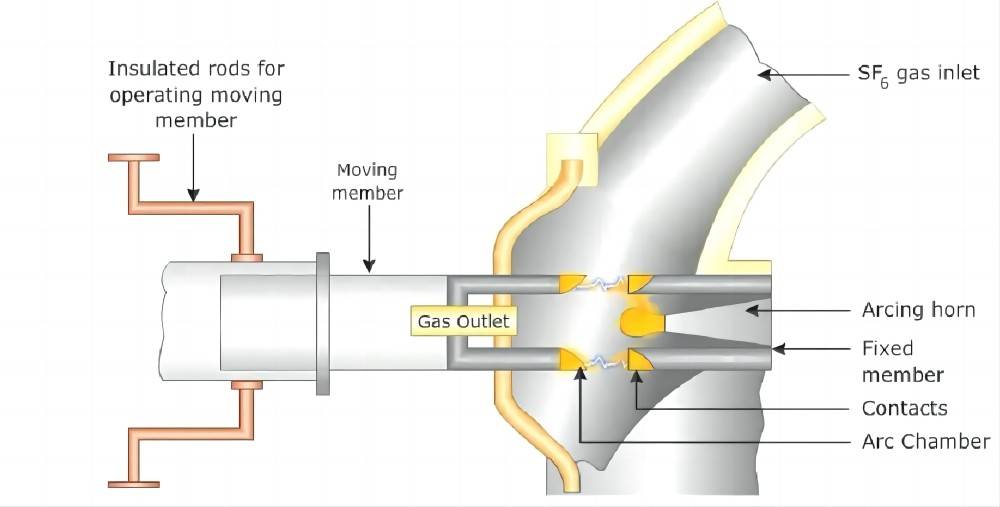
Understanding SF6 Gas Filling Equipment
SF6 gas filling equipment encompasses a range of tools and machinery designed to accurately fill SF6 gas into circuit breakers. Traditionally, this process involved manual handling and cumbersome procedures. However, advancements in technology have led to the development of automated systems, streamlining the filling process.
- Traditional equipment: Traditional SF6 gas filling equipment typically consists of gas cylinders, hoses, and pressure regulators.
- Components: It includes gas cylinders, hoses, and pressure regulators.
- Manual process: Operators manually connect this equipment to the circuit breaker and oversee the filling process.
- Reliability but labor-intensive: While reliable, this method is labor-intensive and susceptible to human error.
- Modern automated systems: Modern automated systems have revolutionized SF6 gas filling.
- Integration of advanced technology: These systems integrate sensors, control panels, and pneumatic mechanisms to automate the filling process.
- Precise parameters: Operators can set precise parameters, ensuring optimal gas levels without constant supervision.
- Efficiency, cost reduction, and safety: These automated systems improve efficiency, reduce labor costs, and enhance safety.
Evolution of SF6 Gas Filling Equipment
The evolution of SF6 gas filling equipment can be traced back to the early days of circuit breaker technology. Initially, filling SF6 gas involved rudimentary methods and basic equipment. Over time, technological advancements and industry demands have driven innovation in filling equipment.
Historically, manual processes dominated SF6 gas filling, relying on simple tools and procedures. However, as the demand for precision and efficiency increased, manufacturers began developing specialized equipment. Early innovations focused on improving accuracy and reducing filling time.
In recent years, the emergence of digital technology has transformed SF6 gas filling equipment. Automated systems now feature advanced sensors, data monitoring capabilities, and remote control functionality. These innovations have elevated the reliability and performance of SF6 gas filling, meeting the evolving needs of industries.
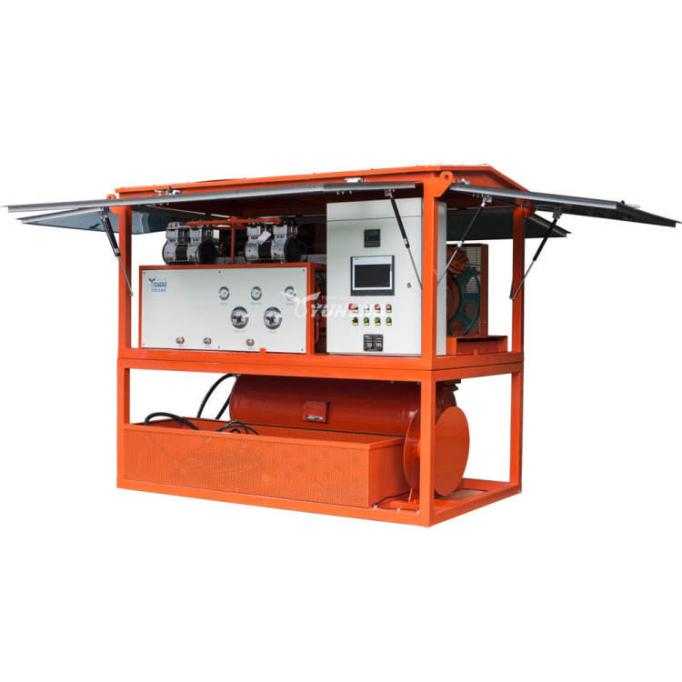
Components of an Ideal SF6 Gas Filling Kit
An ideal SF6 gas filling kit is a collection of specifically chosen parts that work together to safely and efficiently transfer gas from a cylinder to electrical equipment. Here’s a breakdown of the key components:
- High-Quality Hoses: These are heavy-duty tubes designed to transport the SF6 gas. They should have proper fittings on each end to create leak-proof connections with the gas cylinder and the circuit breaker.
- Pressure Gauges: These are instruments with dials or displays that show the pressure of the gas inside the hoses or circuit breakers. Operators rely on these gauges to monitor the filling process in real time and ensure they reach the exact pressure level required.
- Valves: These are controllable openings that regulate the flow of gas within the filling system. They allow technicians to start, stop, and adjust the gas flow during the filling process.
- Safety Devices:
- Pressure Relief Valves: These are automatic safety mechanisms that release excess pressure if it builds up beyond a safe limit. This prevents damage to equipment and potential injury.
- Emergency Shut-Off Mechanisms: These are manual or automatic systems that can quickly stop the flow of gas in case of an emergency. This can be a button on the control panel or a valve that can be closed manually.
- Clear Labeling and Instructions: The kit should have clear labels on all components, indicating their function and proper usage. Additionally, the kit should come with detailed instructions that outline the safe setup and operation of the entire filling system.
Best Practices for SF6 Circuit Breaker Gas Filling
Adhering to best practices is essential for ensuring the effectiveness and safety of SF6 circuit breaker gas filling. Operators must follow established guidelines and procedures to minimize risks and optimize performance.
1. Precautions and Safety Guidelines
- Personal Protective Equipment (PPE): Always wear appropriate gloves and eye protection specifically rated for SF6 gas handling.
- Ventilation: Ensure proper airflow in the filling area to prevent gas buildup. Stale air can pose health risks.
- Pre-Filling Inspection: Before starting, thoroughly inspect all hoses, fittings, and gauges for leaks or damage. Do not proceed if you find any issues.
2. Steps for Proper Gas Filling Procedure
- Circuit Breaker Preparation: The circuit breaker should be clean and free of any debris or moisture that could interfere with the filling process.
- Secure Connection: Carefully connect the SF6 gas filling kit to the circuit breaker using high-quality, properly sized hoses and fittings to create leak-proof connections.
- Controlled Filling: Open the cylinder valve slowly to allow for a gradual and controlled flow of gas into the circuit breaker.
- Precise Monitoring: Continuously monitor the pressure gauge to ensure the filling pressure matches the exact level required for the specific circuit breaker.
- Completion and Verification: Once the target pressure is reached, close the cylinder valve securely and disconnect the filling kit.
- Leak Check: Perform a thorough leak test on all connections to verify a perfect seal and prevent potential gas leaks.
3. Maintenance and Troubleshooting Tips
- Regular Upkeep: Schedule regular inspections and maintenance for your SF6 gas filling equipment to ensure it functions properly and maintains optimal performance.
- Prompt Repairs: Address any leaks, malfunctions, or equipment damage identified during inspections immediately. Don’t attempt to use faulty equipment.
- Training for Personnel: Invest in training your personnel on the proper use of SF6 gas filling kits and the filling procedures outlined above. This ensures everyone involved understands the importance of safety and efficient operation.
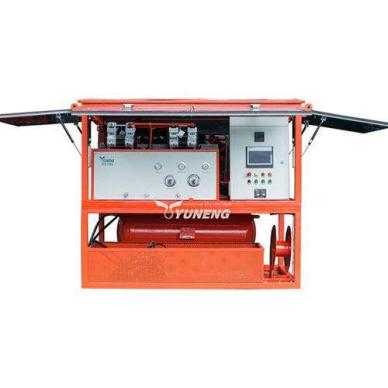
Applications and Industries Utilizing SF6 Gas Filling Equipment
SF6 gas filling equipment finds widespread applications across various industries, including power generation, distribution, and industrial manufacturing. These industries rely on circuit breakers for safe and efficient operation, making SF6 gas filling equipment indispensable.
1. Power Generation and Distribution
- Function: Utilities and power generation plants rely on high-voltage circuit breakers to safeguard electrical grids and equipment from power surges and short circuits. These circuit breakers are often filled with SF6 gas due to its insulating properties.
- Application: Ensures proper maintenance and operation of SF6-filled circuit breakers within critical power infrastructure. Technicians use this equipment to refill gas after maintenance or top up levels due to natural gas loss over time.
2. Industrial Manufacturing
- Function: Many industrial facilities utilize high-power electrical equipment that requires protection from faults and overloads. SF6 gas-filled circuit breakers are a common choice for this purpose.
- Application: Manufacturing facilities rely on this equipment to maintain and service their SF6 circuit breakers efficiently. Regular gas refills and leak checks are crucial to ensure uninterrupted operation and minimize production downtime due to electrical issues.
3. Research and Development
- Function: Research institutions and laboratories may employ SF6 gas for various experimental setups and testing applications. The gas’s insulation and other unique properties can be valuable for specific research areas.
- Application: Researchers can utilize SF6 gas filling kits to precisely control and measure gas flow rates within their experiments. This allows for controlled environments and accurate data collection during research and development projects.
Conclusion
SF6 gas filling equipment plays a critical role in maintaining the reliability and efficiency of circuit breakers in various industries. The evolution of filling equipment has led to improved accuracy, efficiency, and safety in SF6 gas handling operations. By adhering to best practices and embracing technological advancements, industries can optimize their use of SF6 gas filling equipment while minimizing environmental impact.