The Difference Between Lubrication Oil Purifier and Lube Oil Blending Machine
Lube oil, also known as lubricating oil, plays a critical role in the smooth and efficient operation of various machinery. It minimizes friction, protects components from wear and tear, and assists in heat dissipation. However, lube oil degrades over time due to factors like contamination and oxidation, necessitating specific processes to ensure its continued effectiveness. This article delves into the distinct functions of two essential equipment types in the lube oil management domain: lube oil purifiers and lube oil blending machines.
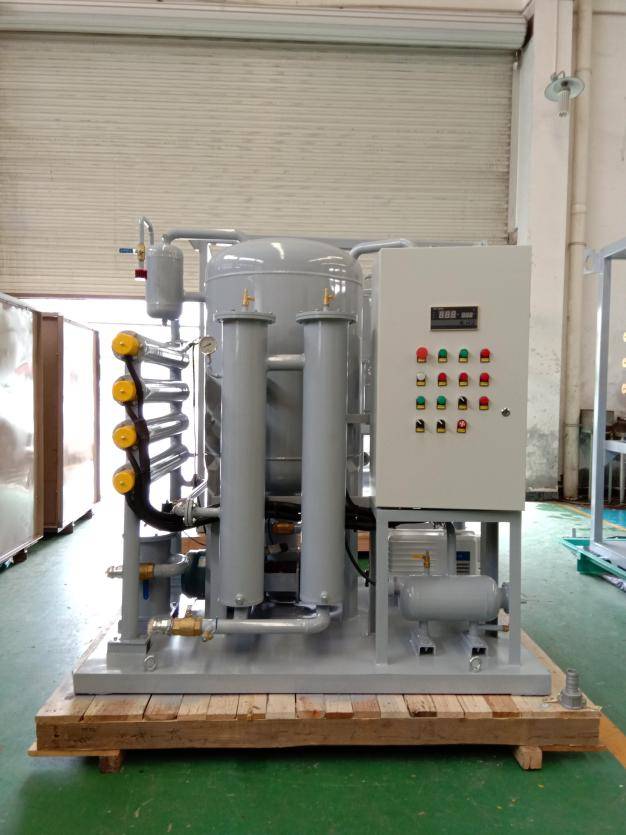
Lubrication Oil Purifier: Restoring Used Oil to Extend its Lifespan
A lubrication oil purifier is a specialized machine meticulously designed to eliminate contaminants and restore the properties of used lube oil. By removing impurities like water, dirt, and metal particles, the purifier extends the lifespan of the oil, allowing it to be reused instead of being discarded. This approach offers several significant benefits:
- Reduced Dependence on Virgin Oil: Recycling used oil through purification diminishes the need for virgin oil, a valuable, often non-renewable resource. This is crucial from an environmental standpoint, as it helps to conserve natural resources and minimize the environmental impact associated with the extraction and processing of virgin oil.
- Cost-Effective Alternative: Purifying used oil is a cost-effective alternative to replacing it entirely. This translates to substantial savings for industries and individuals utilizing significant amounts of lube oil in their operations.
Lube oil purifiers employ various technologies to achieve their cleaning and restoration capabilities. Some of the most commonly used methods include:
- Centrifugation: This technique utilizes high-speed rotation to separate heavier contaminants from the lighter oil. The oil and contaminants settle in distinct layers within the centrifuge, enabling their efficient separation.
- Filtration: This method involves passing the used oil through various filters with progressively smaller pore sizes. These filters trap contaminants while allowing the clean oil to pass through.
- Vacuum Dehydration: This process uses a vacuum to remove water from the oil. Water can negatively impact the lubricating properties of oil and accelerate its degradation.
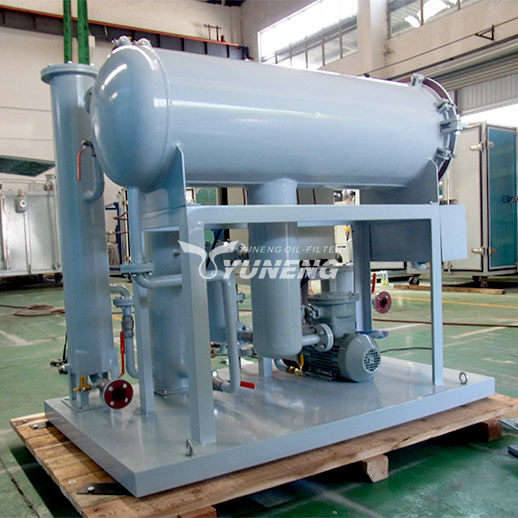
Lube Oil Blending Machine: Creating Customized Blends for Diverse Applications
In contrast to a lube oil purifier, a lube oil blending plant focuses on creating entirely new oil blends. This intricate machinery combines various base oils and additives to formulate customized lubricants suited to specific applications. By meticulously controlling the composition, lube oil blending machines enable the creation of oils with targeted properties:
- Precise Viscosity Control: Viscosity refers to the oil’s resistance to flow. Different applications require oils with varying levels of viscosity. For instance, engine oils typically require a higher viscosity compared to hydraulic oils. Lube oil blending machines allow for precise control over viscosity by adjusting the ratio of base oils and viscosity modifiers.
- Tailored Anti-Wear Properties: Oils formulated for heavy-duty machinery often require enhanced anti-wear properties to minimize friction and protect components from wear and tear. Lube oil blending machines facilitate the incorporation of specific additives that enhance these properties.
The core components of a lube oil blending plant include:
- Storage Tanks: These tanks hold the base oils and additives used in the blending process. They are typically constructed from materials that ensure the compatibility and integrity of the stored materials.
- Metering and Mixing Equipment: This equipment accurately measures and combines the base oils and additives in precise proportions as per the desired blend formulation.
- Homogenization Equipment: After the ingredients are combined, this equipment ensures their thorough mixing to create a uniform and consistent blend. This is crucial for ensuring the consistent performance of the final product.
The application of lube oil blending plants extend across various industries:
- Automotive Industry: Engine oils, transmission fluids, and other lubricants used in automobiles are typically formulated through lube oil blending processes.
- Industrial Applications: These machines are also essential in manufacturing lubricants for industrial equipment like gearboxes, compressors, and turbines.
- Marine Engines: Lube oil blends specifically designed for marine engines are created through meticulous blending processes to withstand the challenging operating conditions at sea.

Key Differences: Understanding the Distinction Between Purifiers and Blenders
While both lube oil purifiers and blending machines play vital roles in the management and utilization of lube oil, they serve distinct purposes and operate in fundamentally different ways. Here’s a summary table for a breakdown of the key differences:
Feature | Lube Oil Purifier | Lube Oil Blending Machine |
Purpose | Restores used oil for reuse | Creates new, customized oil blends |
Input | Used lube oil | Virgin base oils and additives |
Output | Cleaned and revitalized lube oil | Customized oil blends for specific applications |
Complexity | Less complex technology (centrifugation, filtration) | More complex technology (metering, mixing, homogenization) |
Regulations | Plays role in adhering to waste reduction regulations | Governed by regulations for new oil product production and storage |
Conclusion
Lube oil purifiers and blending machines operate in complementary roles within the overarching framework of lube oil management. While purifiers extend the lifespan of used oil, minimizing waste and resource consumption, blending machines create new, customized blends to cater to the diverse needs of various applications. Understanding the distinct functionalities of these machines empowers individuals and industries to make informed decisions regarding lube oil utilization, contributing to sustainability, cost-efficiency, and optimal equipment performance. By leveraging these technologies effectively, we can ensure the continued smooth and efficient operation of machinery while minimizing environmental impact.