The Importance of SF6 Gas Purification, Disposal and Recycling
Table of Contents
Sulfur hexafluoride (SF6) gas is widely utilized in high-voltage electrical equipment due to its exceptional insulating and arc-quenching properties. However, impurities in SF6 gas can significantly degrade its performance and pose environmental and safety hazards. This article delves into the sources and detrimental effects of SF6 gas impurities, emphasizes the necessity of purification, and provides a detailed exploration of SF6 gas recycling technologies, aiming to offer a thorough technical reference for the safe and efficient utilization of SF6 gas.
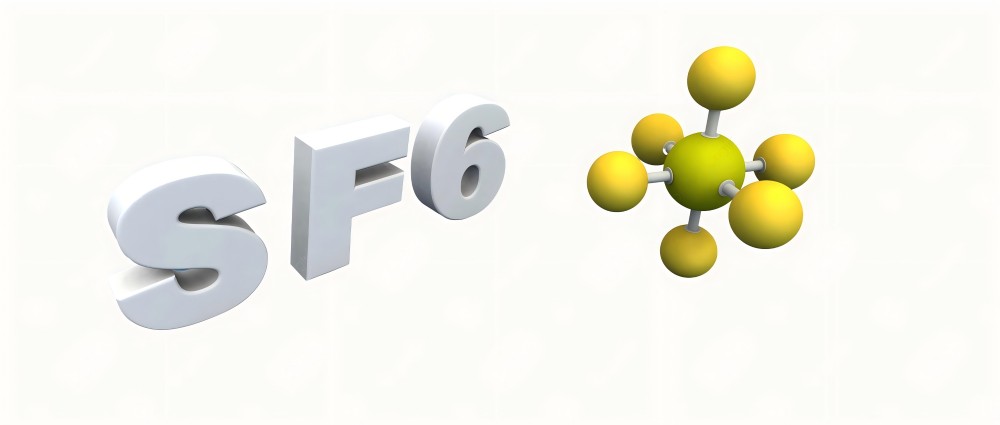
Sources and Hazards of SF6 Gas Impurities
Types of Impurities in SF6 Gas
- Moisture (H₂O): Moisture is a prevalent contaminant in SF6 gas. It diminishes the gas’s dielectric strength and reacts with SF6 decomposition products (e.g., SOF₂, HF) to form highly corrosive acids (e.g., H₂SO₄, HF), which corrode internal metal components and shorten equipment lifespan.
- Decomposition Byproducts: Electric arcs or high temperatures can decompose SF6 gas, generating harmful substances like SO₂, HF, and S₂F₁₀. S₂F₁₀ is particularly hazardous, being a highly toxic gas that severely impacts the human respiratory system.
- Air (O₂, N₂): The presence of air reduces SF6 gas’s insulating capacity, and in low-temperature environments, air liquefaction increases operational risks.
- Oil and Particulates: Oil and particulates can trigger partial discharges and lead to insulation breakdowns, jeopardizing equipment safety.
Hazard Examples
- Equipment Corrosion: The HF produced by the reaction of moisture with SF₄ corrodes metals like aluminum and copper, accelerating equipment deterioration.
- Greenhouse Effect: SF6 has a global warming potential (GWP) 23,500 times greater than CO₂, making its leakage a significant contributor to climate change.
- Human Safety: Highly toxic substances like S₂F₁₀ have extremely low exposure limits, posing severe health risks from both short-term and long-term exposure.
Can the SF6 Gas After Purification be Directly Released?
SF6 gas purification is essential to remove harmful impurities and restore the gas to its original insulating properties. Purification processes typically involve physical adsorption, chemical treatment, and filtration to eliminate moisture, oil, and decomposition byproducts. However, even after purification, SF6 gas cannot be directly released into the atmosphere due to its high GWP. Proper SF6 gas disposal or recycling is required to comply with environmental regulations.
Direct disposal of SF6 gas is prohibited due to its severe environmental impact. The gas must be either recycled for reuse or subjected to controlled degradation processes. SF6 gas disposal through incineration or chemical neutralization is possible but requires advanced technology and strict regulatory compliance. The preferred approach is SF6 gas recycling, which not only mitigates environmental harm but also reduces the need for new SF6 gas production.
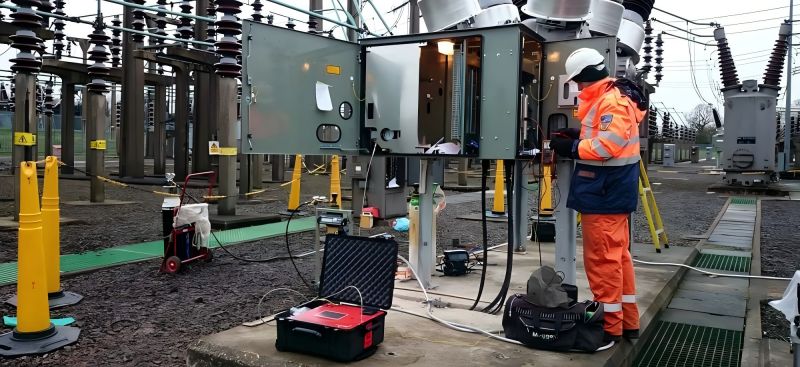
Technological Principles of SF6 Gas Recovery and Recycling
The effective management of SF6 gas necessitates a robust and comprehensive approach, encompassing safe extraction, thorough impurity removal via SF6 gas purification, efficient storage, and reliable reuse through SF6 gas recycling. This intricate process relies on a combination of physical separation, chemical purification, and precise phase change control. Key technical principles and parameters include:
1. Recovery Stage: Maximizing Extraction and Enabling Efficient Liquefaction
Vacuum Compression Technology
The initial phase of SF6 gas recycling involves the critical task of extracting the gas from electrical equipment. To achieve this, oil-free dry vacuum pumps, designed to attain an ultimate vacuum of ≤1 Pa, are employed. These pumps meticulously extract the SF6 gas, ensuring residual pressures fall below 5 kPa. This meticulous process facilitates a recovery rate exceeding 98%, minimizing losses and maximizing the volume of gas available for purification and reuse.
Following extraction, reciprocating compressors play a pivotal role in pressurizing the recovered SF6 gas to a range of 1.5-2.0 MPa. This pressurization, coupled with the operation of advanced refrigeration units capable of achieving temperatures between -30°C and -40°C, induces the liquefaction of SF6 gas. This phase change significantly reduces the gas’s volume by a factor of approximately 300, drastically enhancing storage efficiency and minimizing the physical space required for holding the recovered gas.
Refrigeration Phase Change Principles
The efficiency of SF6 gas recycling is heavily dependent on precise temperature control during the liquefaction process. Maintaining temperatures below -30°C, combined with controlled pressurization, facilitates rapid SF6 liquefaction. This meticulous approach minimizes energy loss during the phase transition, ensuring an energy-efficient recovery process.
To further enhance thermal efficiency, direct heat exchange with environmentally friendly refrigerants, such as R507A, is employed. This method offers a significant improvement in heat transfer efficiency, exceeding that of traditional indirect heat exchange methods by over 30%. This not only enhances the speed of liquefaction but also reduces the overall energy footprint of the SF6 gas recycling process.
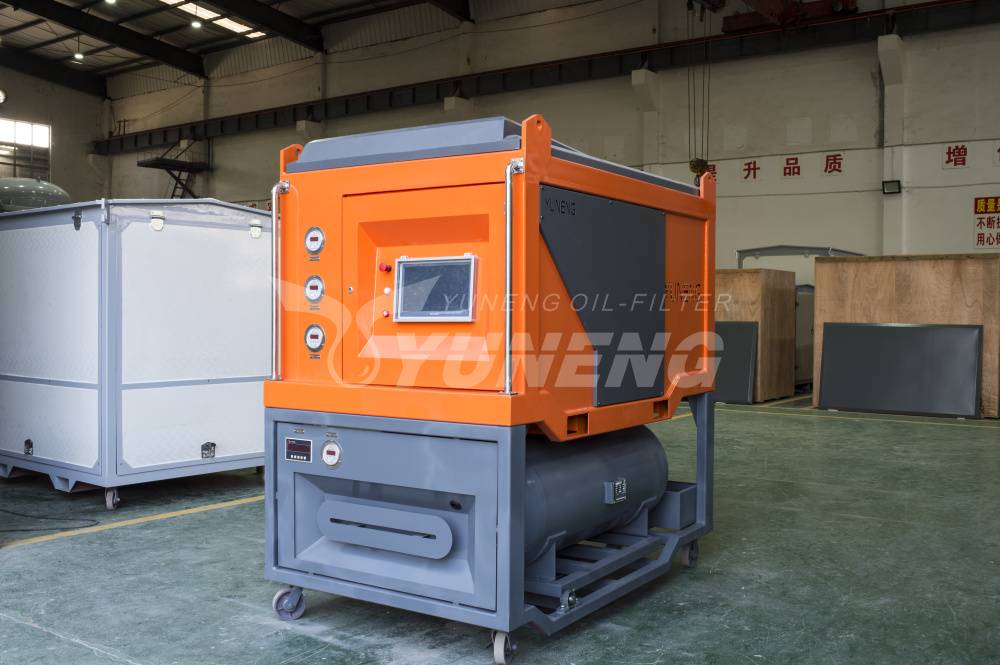
2. Purification Stage: Achieving Multi-Level Impurity Separation through SF6 Gas Purification
Physical Adsorption Purification
SF6 gas purification relies heavily on physical adsorption to remove moisture and oil contaminants. 4A molecular sieves, characterized by their 0.4 nm pores, are utilized to effectively adsorb moisture, reducing its concentration to ≤5 ppm. These sieves exhibit a dynamic adsorption capacity of 20 g H₂O/kg of adsorbent, ensuring thorough moisture removal.
High-surface-area activated carbon, boasting a surface area of 1,200 m²/g, is employed to adsorb mineral oil to a concentration of ≤1 μg/g. Additionally, this activated carbon effectively retains acidic decomposition products, such as SO₂ and HF, further enhancing the purity of the recovered SF6 gas.
Low-Temperature Condensation Separation
To separate impurities with varying boiling points, a three-stage condensation process is implemented. This involves sequentially cooling the gas to 0°C, -20°C, and -50°C, allowing for the selective condensation and removal of impurities like SF₄ (boiling point -38°C) and SO₂F₂ (boiling point -55°C).
Centrifugal oil mist separators are deployed to remove particulate matter, achieving gas cleanliness levels that meet or exceed NAS 1638 Class 6 standards. These separators effectively remove particles with a diameter of ≥0.1 μm, ensuring the gas is free from solid contaminants.
Chemical Catalytic Decomposition (for Toxic Byproducts)
For the removal of toxic byproducts, such as SOF₂ and SO₂F₂, a chemical catalytic decomposition process is employed. High-voltage electric fields, operating at 10 kV, are used to decompose these byproducts into harmless constituents, such as sulfur, fluorine, and oxygen, achieving a decomposition efficiency of >99%.
Additionally, 20% NaOH solutions are utilized to absorb fluorine, producing harmless solids, such as NaF and NaFO₃, through the chemical reaction: 3F₂ + 6NaOH → 5NaF + NaFO₃ + 3H₂O.
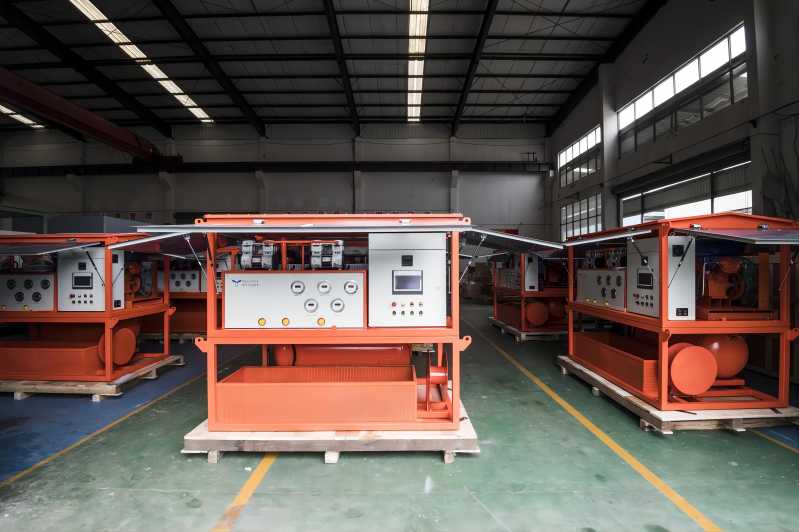
3. Storage and Detection: Ensuring Gas-Liquid Dual-State Management
High-Pressure Liquid Storage
Recovered and purified SF6 gas is stored in specialized high-pressure tanks constructed from 34CrMo4 steel, designed to withstand a pressure of 3.0 MPa and featuring a wall thickness of ≥8 mm. These tanks are designed to safely contain liquid SF6 at a density of 1.4 g/cm³.
To ensure safety in the event of overpressure, bursting discs are incorporated into the storage system, designed to activate at a pressure of 3.8 MPa.
Purity Detection Technology
Rigorous purity testing is essential to confirm the effectiveness of the SF6 gas purification process. Key parameters, including purity, moisture content, acidity (as HF), and mineral oil concentration, are meticulously measured.
Industry-standard methods, such as gas chromatography (GC), dew point analyzers, ion chromatography (IC), and infrared spectroscopy (IR), are employed to ensure that the purified SF6 gas meets stringent quality standards, including purity of ≥99.99%, moisture content of ≤5 ppmv, acidity of ≤0.1 ppmw, and mineral oil concentration of ≤1 μg/g.
4. Recharging and Reuse: Enabling Precision Control and Cycle Validation
Quantitative Recharging Technology
During the recharging phase of SF6 gas recycling, mass flow controllers are used to accurately calculate the amount of SF6 gas to be reintroduced into electrical equipment. These controllers rely on gas state equations to ensure precise measurements, with an accuracy of ±0.5%.
To prevent mechanical stress on equipment insulation, a gradual pressurization strategy is implemented, involving a phased increase in pressure from 0.2 MPa/min to 0.5 MPa/min.
Cycle Life Assessment
To ensure the long-term reliability of SF6 gas recycling, cycle life assessments are conducted in accordance with IEC 60480 standards. These standards permit up to 15 SF6 gas cycles and a cumulative use of up to 20 years.
Performance monitoring is conducted during each cycle, assessing critical parameters, such as dielectric strength (≥75 kV/cm) and arc-quenching time (≤15 ms), to ensure the recycled SF6 gas maintains its performance characteristics.

Wrap Up
The purification, disposal, and recycling of SF6 gas are critical to ensuring the safe and sustainable operation of electrical equipment. By removing harmful impurities and implementing closed-loop recycling systems, the environmental impact of SF6 gas can be significantly reduced. Advanced technologies for recovery, purification, and reuse not only enhance the efficiency of SF6 gas utilization but also contribute to global efforts to combat climate change. As the demand for reliable and eco-friendly power systems grows, the importance of SF6 gas recycling will continue to increase, paving the way for a greener and more sustainable future.