The Importance of Vacuum Pumping System in Power System Oil Purification
In power systems, the vacuum pumping system, vacuum oil purifier, and vacuum dehydration oil purification system (VDOPS) work in concert to ensure the proper functioning of electrical equipment and the quality of the oil used within these systems. These systems, each with distinct roles, collectively form an efficient and reliable oil management framework essential for maintaining the operational integrity of power systems. This article delves into the functions and interrelations of these systems, highlighting their significance in power systems.
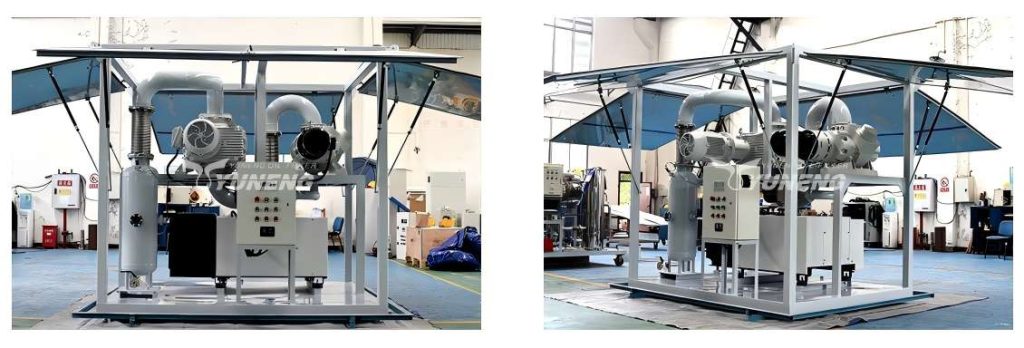
Functions of the Vacuum Pumping System in Power Systems
The vacuum pumping system plays a crucial role in power systems by performing several vital functions:
- Condenser Vacuum Extraction: The vacuum pumping system removes air and non-condensable gases from the condenser, maintaining a high vacuum state. This enhances the efficiency of steam turbines and the thermal efficiency of power plants.
- Vacuum Maintenance: During condenser operation, the vacuum pump continuously works to remove any leaked air, maintaining optimal condenser backpressure.
- Vacuum Water Suction: In the cooling water system, the vacuum pump maintains the siphon effect in pipelines, ensuring the cooling water circulation pump operates at the designed flow rate, reducing power consumption.
- Flue Gas Desulfurization: In the flue gas desulfurization process, the vacuum pump assists in dehydrating the gypsum formed and removing impurities and water vapor during filtration.
- Fly Ash Conveyance: Under vacuum conditions, fly ash is transported to a central collection point, reducing dust emissions and environmental pollution.
- Turbine Seal Drainage: The vacuum pump removes excess steam and condensate from steam turbine seal drains, maintaining seal performance.
- Boiler Water Entry System Venting: Before water enters the boiler system, the vacuum pump, in conjunction with a degasser, removes dissolved gases, preventing air blockage within the system.
- Geothermal Gas Removal: The vacuum pump also removes non-condensable gases from geothermal power generation equipment, ensuring efficient system operation.
The vacuum pumping system’s functions are critical for ensuring stable operation and improved energy conversion efficiency in power systems. By effectively managing and controlling vacuum levels, these systems help reduce energy losses and enhance the economic and environmental performance of power plants.
Functions of the Vacuum Oil Purifier
The vacuum oil purifier is primarily used for purifying oil, utilizing the principles of vacuum to remove water, gases, and impurities from the oil. It typically includes components such as a vacuum pump, filters, and heaters, significantly improving the quality and performance of the oil. The key functions of a vacuum oil purifier include:
- Water Removal: Through evaporation under vacuum conditions, the vacuum oil purifier removes free and emulsified water from the oil.
- Gas Removal: Dissolved gases are released and extracted in a vacuum environment, enhancing the insulating properties of the oil.
- Impurity Removal: The filtration system removes solid particles and other contaminants, ensuring the purity of the oil.
The vacuum oil purifier’s simple yet efficient operation makes it suitable for purifying various types of oils, including transformer oil, insulating oil, and lubricating oil. By enhancing the electrical and thermal performance of the oil, the vacuum oil purifier extends the lifespan and reliability of power equipment.
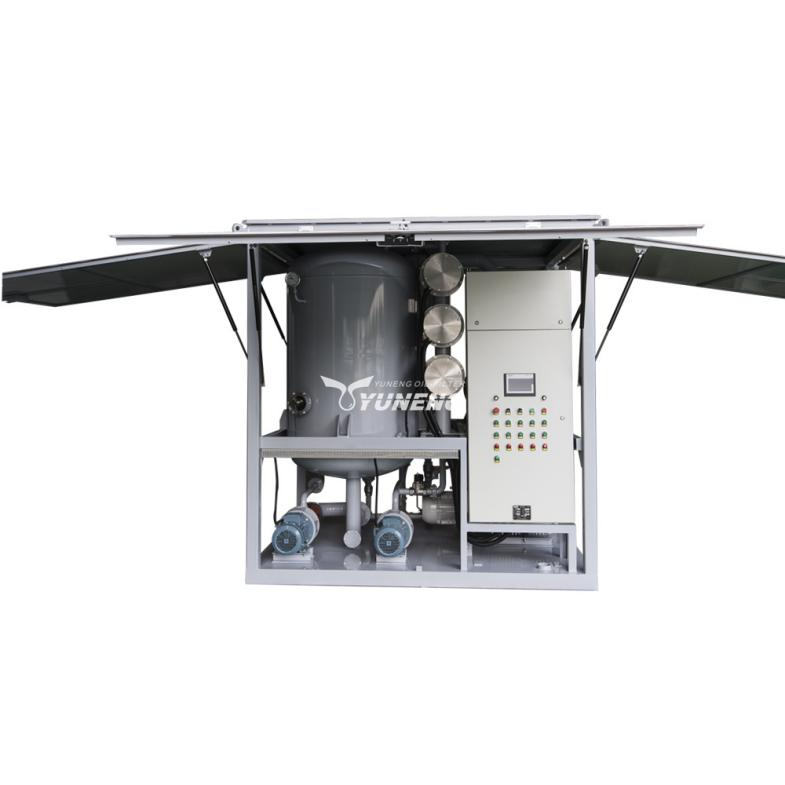
Functions of the Vacuum Dehydration Oil Purification System
The vacuum dehydration oil purification system (VDOPS) is a specialized system designed for oil dehydration and purification. Combining vacuum pumps and filtration technology, VDOPS achieves deep-level purification of the oil. This system emphasizes the removal of water, including both free and dissolved water, and performs fine filtration to eliminate micro-particles. Here is a detailed explanation as follows:
- Water Removal: VDOPS excels at eliminating all forms of water contamination, including free water (visible droplets), emulsified water (tiny droplets suspended in the oil), and dissolved water (water molecules integrated into the oil’s molecular structure). This comprehensive water removal is crucial for preventing various oil-related issues.
- Gas Removal: Beyond water, VDOPS efficiently extracts dissolved and entrained gases from the oil. These gases, such as oxygen and nitrogen, can accelerate oil degradation and contribute to equipment malfunctions.
- Particle Removal: Equipped with high-efficiency micro-glass or similar filters, VDOPS effectively captures and removes solid contaminants, including wear debris, sludge, and other particulate matter. This helps maintain optimal oil cleanliness and prolong equipment life.
- Oil Recovery: In some cases, VDOPS can also be used to recover oil from contaminated fluids or sludge, extending the lifespan of valuable oil resources.
By addressing these critical areas, VDOPS significantly enhances oil quality and performance. This leads to extended equipment life, improved system reliability, and reduced maintenance costs. VDOPS is particularly valuable in applications where oil purity is paramount, such as in transformers, turbines, hydraulic systems, and other critical machinery.
Differences Between Vacuum Oil Purifiers and Vacuum Dehydration Oil Purification Systems
Although vacuum oil purifiers and vacuum dehydration oil purification systems have overlapping functions, they differ in design purpose, application range, and specific features:
- Design Purpose: The vacuum oil purifier focuses on general oil purification, while the vacuum dehydration oil purification system emphasizes deep dehydration and fine filtration.
- Application Range: The vacuum oil purifier is suitable for purifying a variety of oils, whereas the vacuum dehydration oil purification system is often designed for specific oils or applications that require high levels of dehydration.
- Specific Features: The vacuum dehydration oil purification system may incorporate advanced dehydration technologies, such as coalescing separation, to enhance dehydration efficiency and quality.
When choosing between these systems, it is essential to consider the specific requirements of the oil, treatment goals and desired purification outcomes.
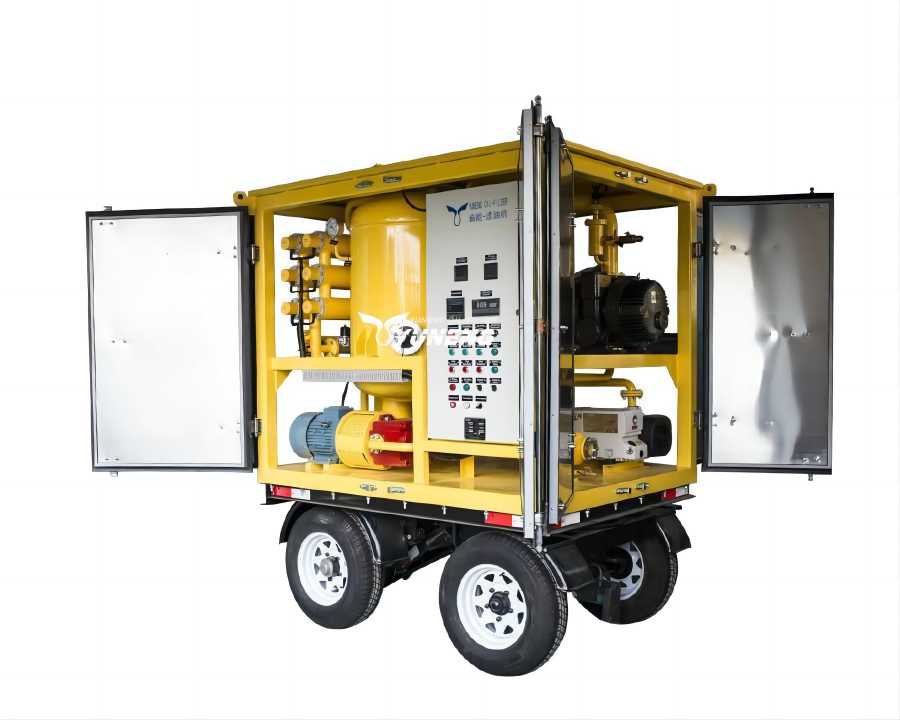
Common Components of Vacuum Oil Purifiers and Vacuum Dehydration Oil Purification Systems
Both vacuum oil purifiers and vacuum dehydration oil purification systems share several common components, which include:
- Vacuum Pump: Creates a low-pressure environment to promote the evaporation of water and gases from the oil, facilitating dehydration and degassing processes.
- Heating System: Typically includes electric heating elements to heat the oil, reducing its viscosity and accelerating the evaporation of water.
- Condenser: Cools and condenses the evaporated water and gases from the oil, allowing for their collection and removal.
- Filtration System: Comprises various grades of filter media to remove solid particles and other impurities from the oil.
- Oil Storage Tanks: Temporarily store the oil before and after processing, often equipped with level monitoring devices.
- Control System: May include temperature controllers, pressure sensors, and level sensors to monitor and automatically adjust the operating conditions of the equipment, ensuring efficient and safe processing.
- Piping and Valves: Direct the flow of oil, control the ingress and egress of fluids in different processing units, and discharge treated oil and collected by-products.
These components form the core processing flow of both systems, though their design and specific functions may differ to cater to various application scenarios and treatment requirements.
The Importance of Regular Oil Purification for Electrical Equipment
Oil in electrical equipment, such as transformer oil, plays a critical role in insulation and cooling. The quality of the oil directly affects the safety and efficiency of electrical equipment. Regular purification of the oil in electrical equipment is essential due to the inevitable mixing of water, gases, particulates, and potential degradation products over prolonged use. These contaminants can degrade the oil’s insulating properties, accelerate its aging, and even cause equipment failures.
Through regular purification, water is effectively removed, preventing oil deterioration and maintaining electrical performance. Additionally, the purification process eliminates acidic substances and other chemical contaminants, preserving the chemical stability of the oil. Removing gases helps prevent oxidation and foam formation, enhancing the thermal stability and electrical strength of the oil.
Regular oil purification extends the service life of electrical equipment, reduces maintenance costs, and ensures the stable operation of the power system. In emergencies, such as oil contamination or equipment failure, prompt purification can quickly restore oil performance, preventing significant losses and safety incidents.
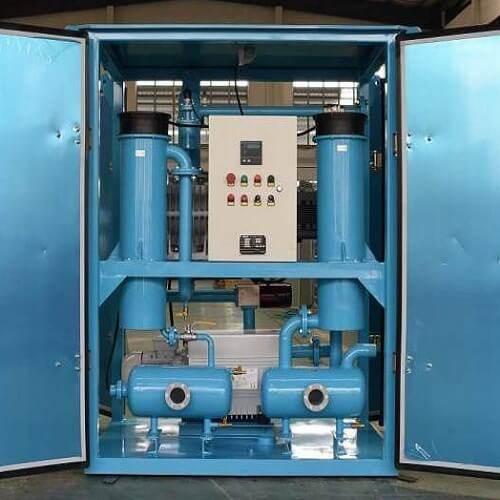
Yuneng: Your Trusted Source for Vacuum Systems
As you explore solutions to enhance the performance and longevity of your power systems, consider Yuneng, a leading oil purifier manufacturer in China. Yuneng offers top-tier vacuum pumping systems, vacuum oil purifiers, and vacuum dehydration oil purification systems designed to meet the rigorous demands of the power industry.
Our vacuum pumping systems are engineered for efficiency and reliability, creating and maintaining the vacuum conditions essential for optimal operation of cooling systems and steam turbines. Yuneng’s vacuum oil purifiers utilize advanced vacuum distillation techniques to effectively remove moisture, gases, and contaminants from transformer oil, ensuring its quality and enhancing the reliability of electrical equipment.
For applications requiring the highest degree of oil purification, Yuneng’s vacuum dehydration oil purification systems (VDOPS) provide an advanced solution. These systems combine vacuum technology with high-efficiency filtration to deliver oil of exceptional purity, which is critical for high-voltage transformers and other critical electrical systems.
Choose Yuneng for vacuum solutions that contribute to the enhanced efficiency and operational excellence of your power systems.