Top Safety Practices for SF6 Gas Recovery: Minimizing Risks in Handling and Recycling
Table of Contents
Sulfur hexafluoride (SF6) gas is essential in many electrical applications. However, it poses specific safety and environmental risks. Proper management is crucial during SF6 recovery and recycling. This article covers key safety practices to help minimize these risks.
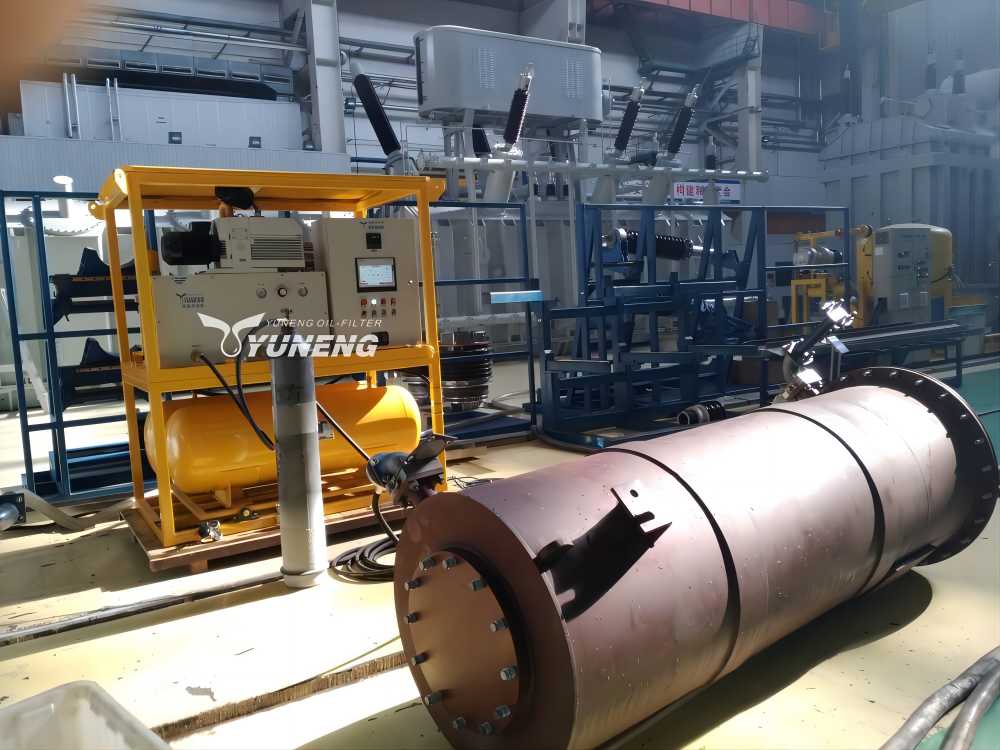
What are the Risks Associated with SF6 Gas
SF6 gas has properties that make it ideal for insulating and arc-quenching in high-voltage electrical equipment, but it also poses specific risks to health, safety, and the environment.
- Environmental Impact as a Greenhouse Gas: SF6 is one of the most potent greenhouse gases known, with a global warming potential (GWP) approximately 23,500 times greater than carbon dioxide over a 100-year period. Even small leaks or releases of SF6 can have a significant environmental impact, contributing to global warming and making its careful recovery essential for environmental responsibility.
- Asphyxiation Hazard: SF6 can displace oxygen in enclosed or poorly ventilated spaces. When SF6 gas accumulates, it can lower oxygen levels, potentially leading to asphyxiation. This risk is particularly relevant in confined spaces or indoor areas where SF6 is used or stored.
- Toxic Byproducts from Decomposition: Under normal conditions, SF6 is stable and non-toxic. However, when exposed to high temperatures—such as during electrical arcing or equipment malfunctions—it can decompose into highly toxic byproducts, including sulfur dioxide (SO2) and various reactive fluorine compounds. These byproducts are corrosive, harmful to human health, and can damage equipment, making their safe handling and detection essential.
- Risk of Pressure-Related Incidents: SF6 is often stored and transported at high pressures, which can pose risks if containers or equipment are damaged or improperly handled. A sudden release of high-pressure SF6 can lead to mechanical injuries, equipment damage, and unintended gas exposure.
These risks indicate that the recovery, storage, and disposal of SF6 require careful management and adherence to safety regulations to minimize its impacts on the environment and health.
Essential Safety Practices in SF6 Gas Recovery
Sulfur hexafluoride (SF6) gas recovery is an important process, especially in the maintenance and repair of high-voltage electrical equipment. The following safety practices should be followed when performing SF6 gas recovery:
Safety Practice | Description |
Proper Training | Personnel involved in SF6 recovery must receive specialized training covering SF6 properties, hazards, equipment handling, and emergency protocols. |
Personal Protective Equipment (PPE) | Technicians should wear PPE, including gloves, safety glasses, and respirators. If risk of exposure to decomposition byproducts exists, additional protection like flame-retardant clothing and full-face shields is required. |
Ventilation Systems | Ensure recovery operations are in well-ventilated areas to reduce asphyxiation risk. Use oxygen monitors and ventilation in confined spaces to maintain safe air quality. |
Leak Detection and Monitoring | Continuous leak detection is essential. Use specialized equipment to monitor SF6 concentrations and address leaks quickly to prevent hazardous exposure. |
Emergency Response Protocols | Establish a clear emergency response plan, including evacuation procedures, access to first-aid kits, and emergency medical services. |
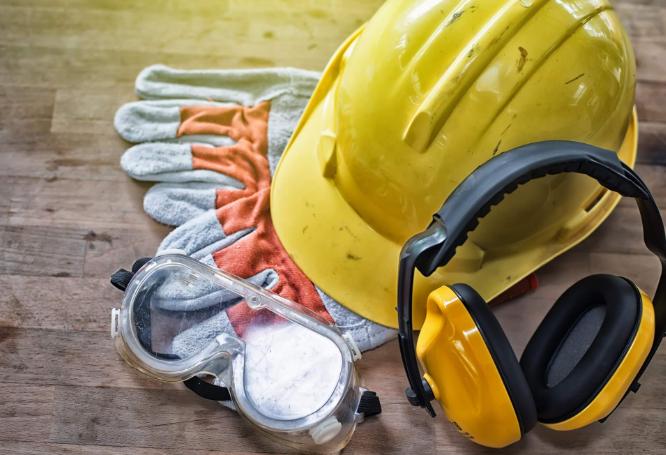
Best Practices for SF6 Gas Recovery
To ensure the safe and efficient recovery of SF6 gas, it is crucial to follow these best practices. Each of these steps is designed to improve recovery efficiency, minimize risks, and extend the life of recovery equipment.
Use Certified SF6 Gas Recovery Equipment
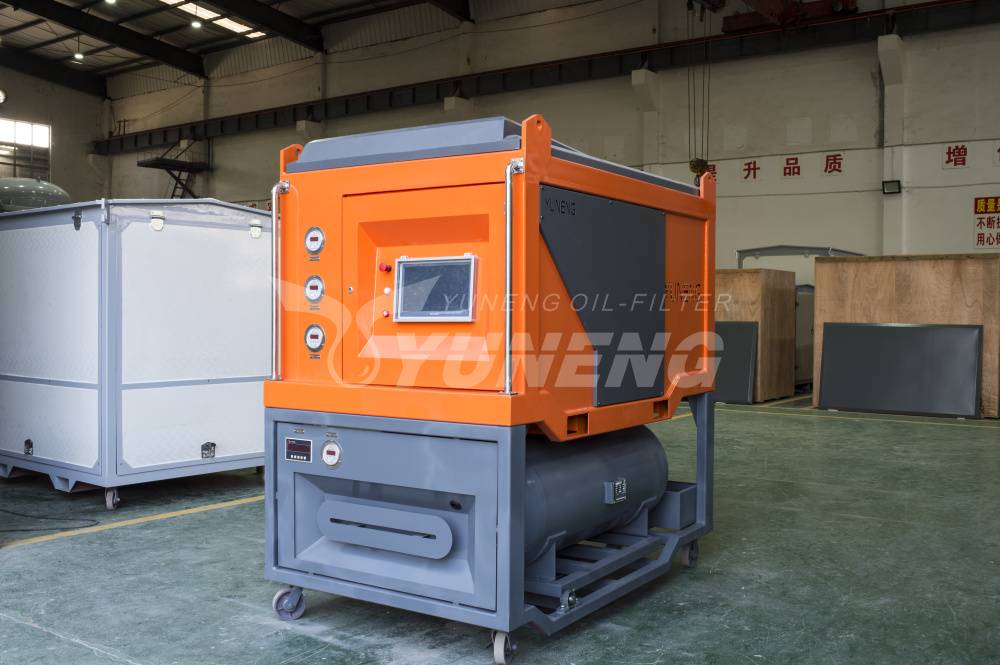
Use high-quality, certified SF6 recovery equipment. They are designed to meet specific safety standards and come with built-in safety features such as pressure relief valves, automatic shut-off mechanisms, and built-in filtration systems to prevent contamination of the recovered gas.
- Gas Purification Systems: These filters remove impurities, moisture, and potentially harmful byproducts from the gas to ensure it meets the required quality standards for reuse.
- Pressure Relief Valves: These are crucial for regulating the pressure within recovery systems, preventing over-pressurization that could lead to equipment failure or hazardous leaks.
- Storage Tanks: Recovery equipment should be paired with robust, well-sealed storage tanks that are designed for the safe containment of high-pressure SF6 gas. These tanks must be regularly inspected for integrity, and they should have monitoring devices to track pressure and detect leaks.
Using equipment that meets international safety standards, such as those outlined by the IEC or ANSI, ensures both the safety of personnel and the minimization of environmental impact.
Regular Maintenance of SF6 Gas Recovery Systems
Regular maintenance and inspection of SF6 recovery equipment is very important for its safe and efficient operation. This includes the following points:
- Inspection of Seals and Valves: Seals and valves are prone to wear and tear due to pressure fluctuations. Regular checks and timely replacement of worn-out parts can prevent leaks during gas recovery, which can lead to safety hazards and loss of gas.
- Pressure Gauge Calibration: Accurate pressure monitoring is vital for safe recovery. Gauges should be calibrated periodically to ensure they provide precise readings, helping prevent dangerous overpressurization of the recovery units.
- Leak Testing: Before using recovery systems, conduct leak detection tests to identify any weak points where gas could escape. Employ technologies such as ultrasonic detectors, infrared cameras, or gas sniffers to ensure there are no unnoticed leaks.
By performing regular preventive maintenance, you not only extend the lifespan of recovery equipment but also ensure that SF6 gas is recovered without risk of accidental release.
Minimize Handling and Maximize Recovery Efficiency
One of the best ways to maximize the efficiency and safety of SF6 recovery is to minimize the handling of the gas and implement closed-loop recovery systems. These systems have several key advantages:
- Reduced Risk of Contamination and Leakage: A closed-loop system allows SF6 gas to be recovered, purified, and reused without exposure to the atmosphere. This reduces the chances of contamination and limits the amount of gas that could escape during handling.
- Environmental and Safety Benefits: By using a closed system, you ensure that the SF6 gas is contained throughout the recovery and recycling process. This approach helps prevent accidental releases, contributing to environmental protection and safety compliance.
- Improved Recovery Efficiency: Closed-loop systems allow for the continuous flow of SF6 gas through purification and recovery phases, maximizing the amount of gas recovered per cycle and minimizing waste. This leads to better resource utilization and cost savings.
Adopting closed-loop recovery systems not only ensures compliance with regulations but also helps significantly reduce SF6 emissions, thus supporting sustainability efforts.
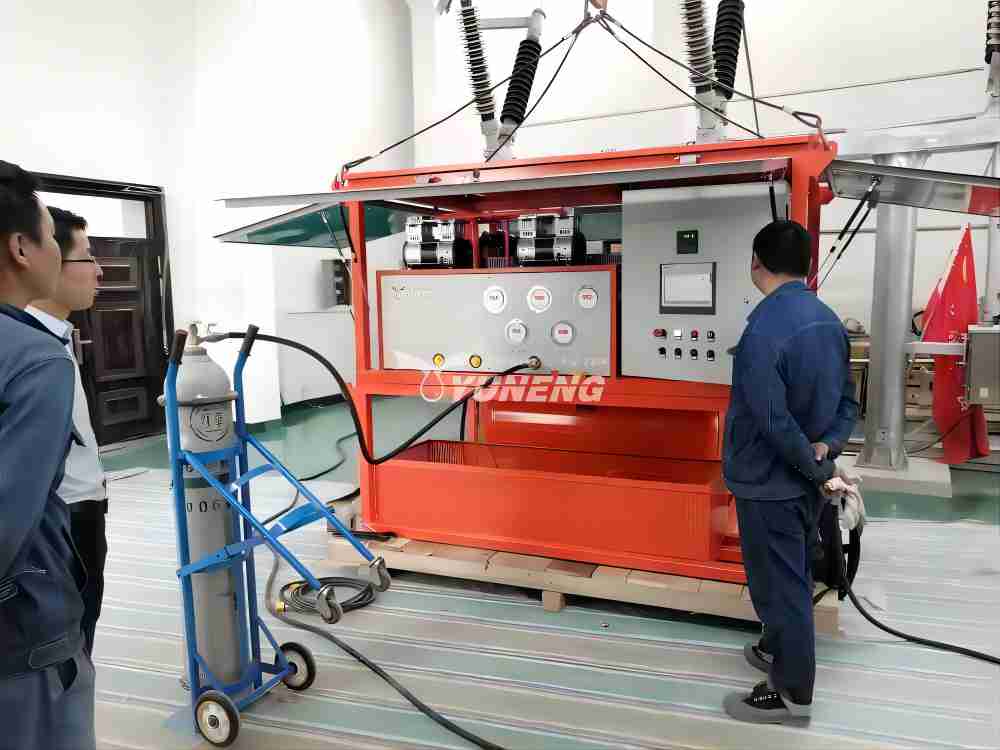
Ensure Proper Storage, Transportation, and Documentation of SF6 Gas
Secure storage and careful transportation are essential to preventing leaks and ensuring SF6 is managed responsibly. Proper documentation further supports safety and compliance with environmental guidelines.
- Safe Storage Practices: Store SF6 in designated high-pressure containers, labeled with safety information, in a well-ventilated, secure area. Containers should be regularly checked for integrity and pressure levels.
- Transport Protocols: Use certified transport vehicles equipped with leak and pressure monitoring systems, ensuring safe transport from recovery to recycling facilities.
- Detailed Record-Keeping: Maintain detailed logs of SF6 quantities, storage conditions, and any transfer activities. These records are important for regulatory compliance and help track and optimize SF6 management practices.
By following these four best practices, organizations can ensure safe and effective SF6 gas recovery while minimizing environmental impact.
Need An SF6 Gas Recovery Equipment?
If you’re looking for reliable and efficient SF6 gas recovery equipment, YUNENG offers top-of-the-line solutions designed to meet the highest safety and environmental standards. As a leading manufacturer of SF6 gas recovery equipment, YUNENG specializes in advanced recovery systems that are engineered for both reliability and efficiency. Their equipment is equipped with cutting-edge features, including real-time monitoring, automatic shut-off valves, and effective filtration systems that ensure safe and thorough gas recovery.
Choosing YUNENG means investing in the future of SF6 gas recovery, with equipment you can trust to deliver performance, sustainability, and safety. For more about our SF6 gas recovery and refining plants, you can visit our product page.