Transformer Oil Filtration Machines and Their Role in Power System Safety
In electrical power systems, transformers serve as the cornerstone for the reliable transmission of electrical energy. These critical devices are responsible for boosting or lowering voltage levels to ensure efficient and stable power delivery. However, the performance and the life of transformers are closely related to the quality of transformer oil, which is both an insulating medium and a cooling medium. In order to maintain the optimal operation of the transformer, transformer oil filtration machines play an indispensable role. These machines are essential to ensure that transformer oil remains free from contaminants that could compromise the safety and reliability of the entire grid.
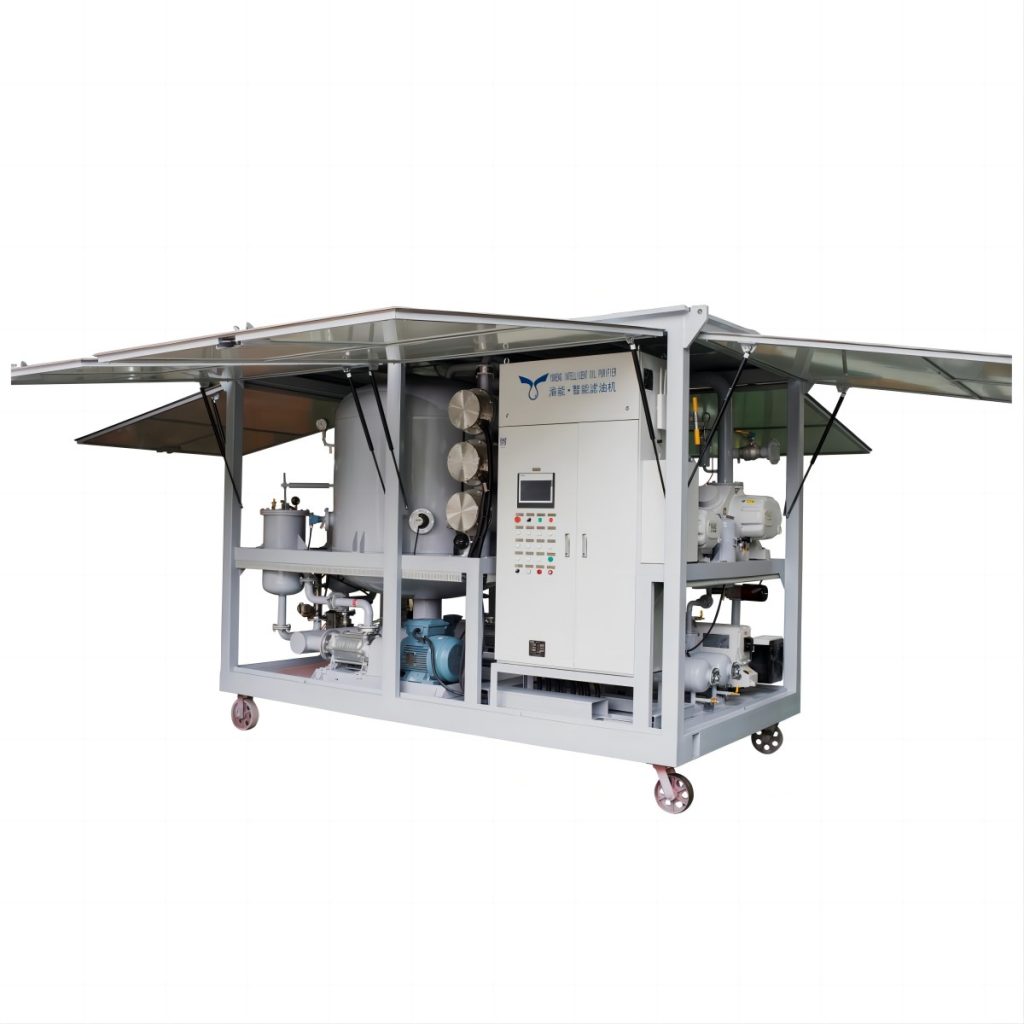
Characteristics and Importance of Transformer Oil
Transformer oil, also known as insulating oil, is a special mineral oil with alkanes, cycloalkanes, and a small proportion of aromatic hydrocarbons. This composition grants transformer oil several important properties:
- Insulation: The main function of transformer oil is to insulate the high and low voltage windings in the transformer, thereby preventing electrical short circuits.
- Cooling: The oil helps to dissipate the heat generated during the transformer operation, maintaining the transformer at a safe operating temperature.
- Arc Extinguishing: During circuit breaker operations, the oil quickly extinguishes electrical arcs, protecting the transformer from potential damage.
Despite its essential roles, transformer oil is susceptible to degradation over time due to exposure to oxygen, moisture, impurities, and acidic substances. These contaminants can significantly reduce the oil’s insulating properties, accelerate equipment aging, and, in severe cases, lead to transformer failure or even fire hazards. Therefore, regular monitoring and maintenance of transformer oil quality are crucial for ensuring the safe operation of power equipment.
Working Principles of Transformer Oil Filtration and Regeneration Machines
Transformer oil filtration machines are designed to purify transformer oil by removing impurities such as water, gases, solid particles, and acidic compounds. These machines are classified according to their filtration principles:
- Vacuum Oil Purifier: Utilizing the principle of vacuum evaporation, these purifiers remove moisture and gases from the oil. By heating the oil under a vacuum, the moisture and gases are rapidly evaporated, then condensed and collected, effectively dehydrating and degassing the oil.
- Precision Filtration Machines: Equipped with high-precision filter elements, typically made of materials like fiber, ceramic, or metal powders, these machines physically remove solid particles from the oil. This filtration process ensures the oil is free from contaminants that could impair its insulation ability and mechanical integrity.
- Regeneration Filtration Machines: Combined with chemical adsorption or ion exchange mechanisms, these machines target acidic substances and oxidation products, which can reduce the electrical properties of the oil. By using adsorbents such as activated clay or silicon, these machines extend the life of the oil by restoring its electrical properties.
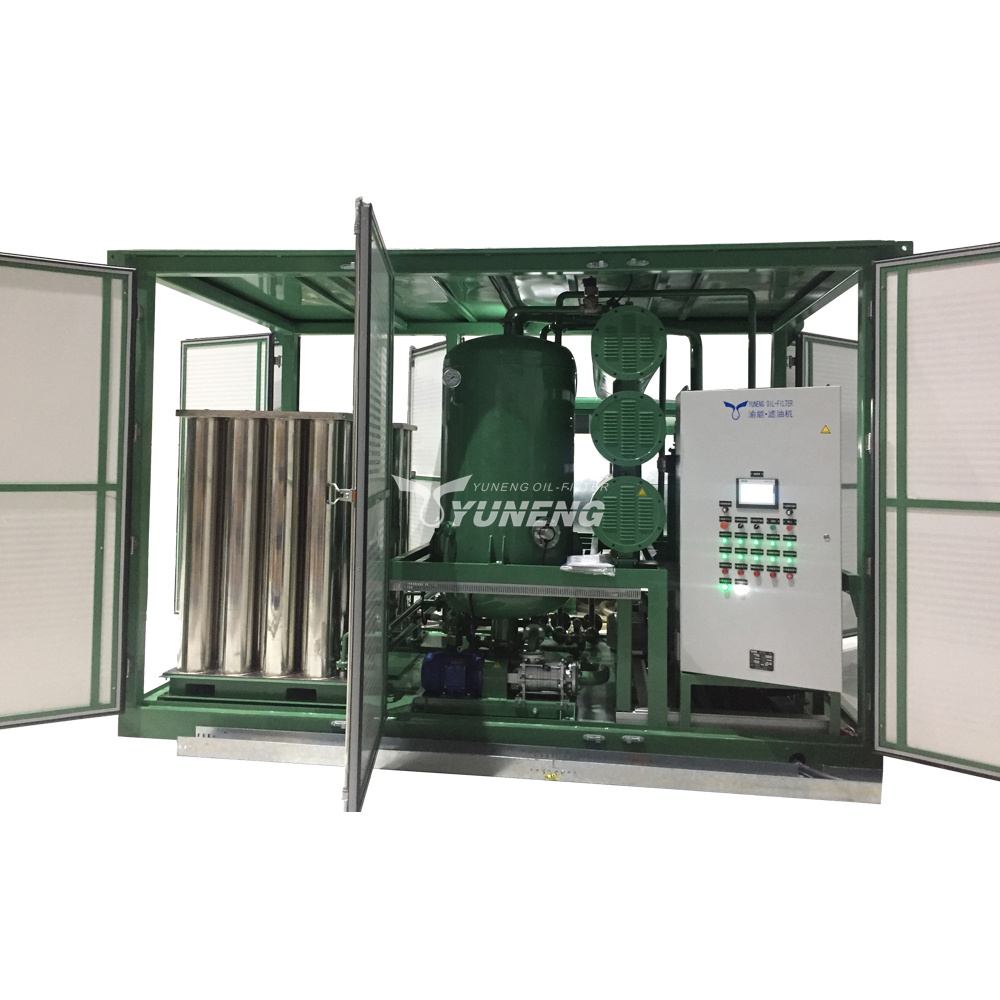
How Transformer Oil Filtration Machines Ensure Safety of Power Equipment
The transformer oil filtration machine plays a pivotal role in maintaining the safety and operational efficiency of power equipment through several mechanisms:
- Vacuum Dehydration and Degassing: The vacuum system in transformer oil filter machines creates a low-pressure environment that facilitates the rapid evaporation of moisture and gases from the oil. This process reduces the water content and gas levels in the oil, thereby improving its insulation performance and cooling efficiency. By removing these contaminants, the machine helps to ensure that the transformer operates within safe and optimal conditions.
- Precision Filtration: The filtration system of transformer oil filter machines incorporates multi-stage, progressively finer filters that effectively remove solid particles and impurities from the oil. This multi-stage approach ensures that even the smallest contaminants are captured, preventing them from entering the transformer and causing insulation breakdown or mechanical damage. Precision filtration is essential for maintaining the overall health of the transformer and extending its operational life.
- Heating System: The precise control of oil temperature prevents overheating, which could lead to the degradation of oil properties. This system ensures the oil is heated to an appropriate level, facilitating the evaporation of moisture while safeguarding against thermal damage.
- Automation Control: Advanced control systems monitor and adjust the processing parameters to minimize the possibility of human error and ensure the oil quality meets the specified standards, thereby improving the overall safety and reliability of the power equipment.
- Safety Protection Measures: Integrated safety features, including overpressure and temperature protection mechanisms, shield the equipment from potential hazards, and ensure a safe operating environment.
The Effect of Heating System on Oil Aging in Transformer Oil Filtration Machines
The heating systems within transformer oil filtration machines has been carefully designed to minimize the aging impact on the oil, thereby preserving its quality. Key features include:
- Temperature Control Systems: These systems precisely regulate the heating temperature to simulate the oil’s operating conditions without exceeding safe limits. By maintaining optimal temperature conditions that mimic the oil’s normal operational environment, these systems extend the oil’s lifespan and preserve its insulation and chemical stability.
- Optimized Heating Design: Advanced heating systems use optimized piping and heating elements to ensure even heat distribution and avoid localized overheating. This design prevents the oil from breaking down or aging prematurely.
Overall, the heating system in transformer oil filter machines plays a critical role in minimizing the impact of thermal stress on oil quality, thereby supporting the long-term performance and reliability of the transformer.
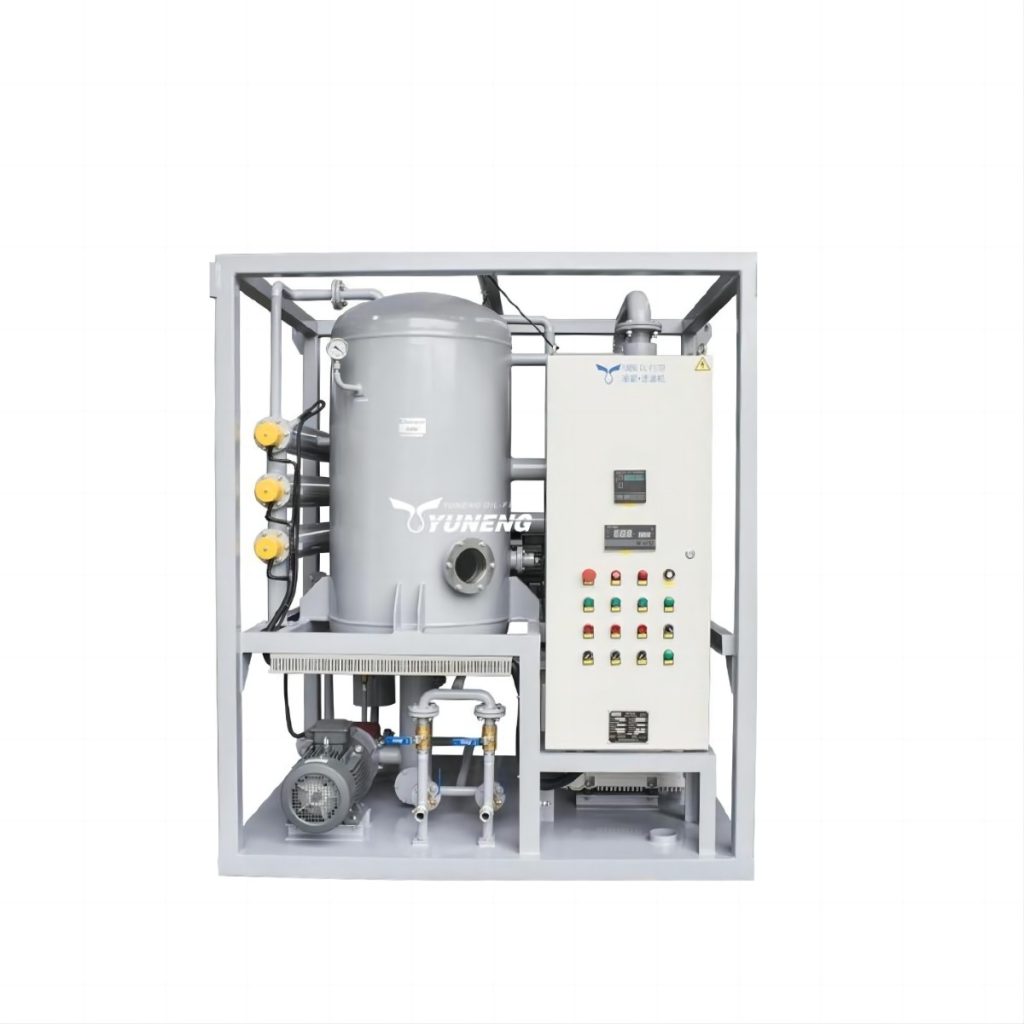
The Automatic Control System of Transformer Oil Filtration Machines
The automatic control system of transformer oil filtration machines is a kind of precision system that integrates various functions to ensure the efficiency, safety, and reliability of the machine. The system includes:
- PLC Control: The Programmable Logic Controller (PLC) acts as the central nervous system, managing the machine’s operations, from startup to shutdown, and coordinating the functions of different components to achieve seamless performance.
- Touchscreen Interface: A user-friendly interface allows operators to set parameters, monitor the machine’s status, and diagnose faults, and improve the ease and effectiveness of operation.
- Automatic Temperature Regulation: This feature maintains the oil within a safe and optimal temperature range, which is essential for effective filtration and preservation of the oil.
- Liquid Level Control: Through advanced sensors, the machine adjusts oil flow to prevent overflows and ensure continuous filtration without interruptions.
- l Foam Suppression: An automated mechanism detects and eliminates foam formation in the oil, preventing air entrainment that could lead to secondary contamination.
- Pressure Protection: Integrated sensors and protection mechanisms automatically stop operation at abnormal pressure levels, protecting equipment from damage.
- Interlock Protections: Comprehensive safety features, including overheating protection, overpressure alarms, overload alarms, oil shortage protection, spray protection, and phase sequence protection, ensure the machine operates safely under all conditions.
- Intelligent Indicators: The system provides real-time monitoring of oil temperature, pressure, vacuum level, filter core contamination level, and machine operating status, enabling operators to maintain oversight and intervene promptly when necessary.
- Modular Design: The modular architecture of the system allows the integration of other options such as frequency conversion systems, in-line humidity analyzers and vacuum gauges, customizing the machine’s functions to specific operational requirements, and increasing filtration efficiency.
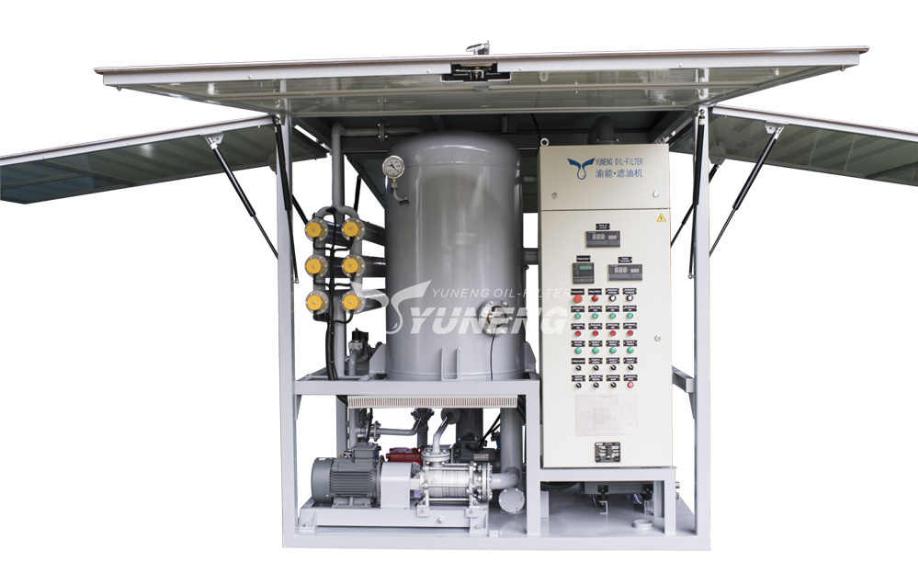
Conclusion
In the dynamic landscape of power systems, the transformer oil filtration machine stands as a guardian, ensuring the life and safety of critical infrastructure. By maintaining the quality of transformer oil through meticulous filtration and purification processes, these machines play a pivotal role in preventing equipment failure, reducing maintenance costs, and safeguarding the overall reliability of power networks. As technology continues to evolve, the future of transformer oil filtration is poised to become even more efficient and effective, contributing significantly to the advancement of power system reliability and efficiency.