Transformer Vacuum Pump Systems and Their Industrial Importance
Table of Contents
Vacuum technology has become an indispensable part of modern industrial processes. In the power sector, where transformers play a critical role, the manufacturing and maintenance processes often require specialized vacuum pump systems. A transformer vacuum pump system, also known as a transformer evacuation system, is essential for ensuring that transformers function efficiently and reliably. This article delves into the principles, components, workflow, and significance of transformer vacuum pump systems while discussing the maintenance procedures that ensure their optimal operation.
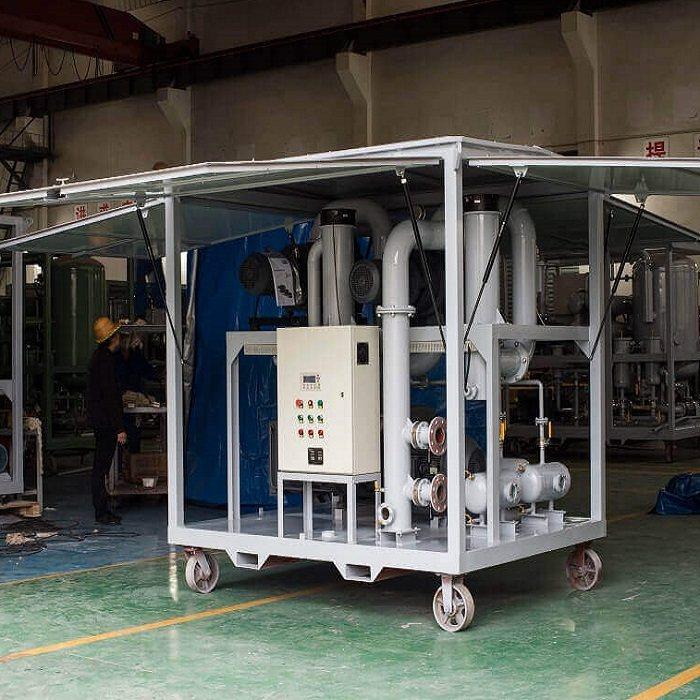
Working Principles of Vacuum Pump Systems
A vacuum pump system is a mechanical device designed to remove gases from a sealed chamber, thereby lowering the internal pressure. Vacuum pumps operate on several mechanisms, and each method of operation depends on the required level of vacuum and the application. The primary mechanisms include:
- Mechanical vacuum pumps: These pumps utilize rotating vanes, pistons, or other mechanical parts to compress and expel gas, thereby creating a vacuum.
- Molecular pumps: By using rapidly spinning blades, molecular pumps remove gas molecules and create a vacuum by capturing them and expelling them at high speeds.
- Diffusion pumps: These pumps employ high-speed oil vapor streams to capture and carry away gas molecules, making them suitable for achieving high vacuum levels.
- Sorption pumps: Utilizing materials like activated carbon, sorption pumps adsorb gas molecules onto their surface, thereby reducing the pressure inside the chamber.
The ability to generate a vacuum is advantageous in many industrial processes, including:
- Enhancing product purity: In industries like electronics and semiconductors, vacuum environments minimize the introduction of impurities, leading to higher product quality.
- Improving welding quality: Vacuum welding prevents oxidation and enhances the quality and durability of welds.
- Extending equipment lifespan: Vacuum conditions reduce wear and tear on equipment by eliminating gas particles that can cause friction and corrosion.
The Specific Role of Transformer Vacuum Pumps
Transformer vacuum pumps are specialized vacuum pump systems designed specifically for the evacuation of transformers. Unlike general-purpose vacuum pumps, transformer vacuum pumps are built to meet the specific demands of transformer maintenance, where precision and efficiency are paramount.
Key Characteristics of Transformer Vacuum Pumps:
- High Flow Rate: Since transformers contain large amounts of insulating oil, the vacuum pump system must be capable of handling high flow rates to evacuate the transformer in a timely manner.
- Corrosion Resistance: Transformer oils may contain acidic compounds or other substances that could corrode standard materials. Therefore, materials used in transformer vacuum pumps need to be resistant to corrosion to ensure durability and reliability.
- Low Noise Levels: As transformers are often maintained indoors, the noise generated by the vacuum pump system must be minimized to maintain a safe and comfortable working environment.
- Automation and Control: Modern transformer vacuum pump systems often feature high levels of automation, allowing operators to easily control and monitor the evacuation process, ensuring accurate and efficient operation.
Components of a Transformer Evacuation System
A transformer evacuation system, or transformer vacuum pump system, consists of several key components, each performing a specific function to ensure efficient and effective operation. These components include:
- Vacuum pump: The core of the system, provides the power needed to evacuate the transformer by removing gases and moisture from the transformer’s interior.
- Vacuum pipeline: This component connects the vacuum pump to the transformer, creating a closed-loop system through which air is evacuated.
- Vacuum valves: These valves control the opening and closing of the vacuum system, regulating the flow of gases and maintaining the desired vacuum level.
- Vacuum gauges: These devices measure the level of vacuum achieved inside the transformer tank, providing feedback to the operator for precise control.
- Oil-gas separator: This device separates oil vapors from the gas mixture being evacuated, preventing oil from contaminating the vacuum pump and maintaining the purity of the transformer oil.
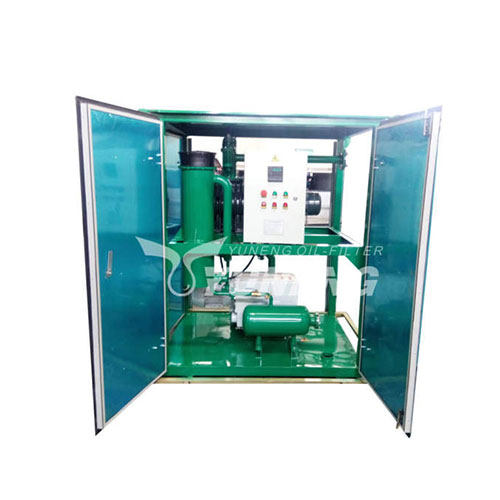
The Process of Transformer Evacuation
The process of transformer evacuation, facilitated by a transformer vacuum pump system, is essential for removing air, moisture, and contaminants from the interior of the transformer. This process prevents electrical discharges within the transformer during operation, which could otherwise lead to equipment failure or reduced lifespan. The key steps in transformer evacuation are as follows:
1. Pre-vacuum Phase: In the first phase, a mechanical vacuum pump is used to evacuate the air inside the transformer tank to a rough vacuum level. This step is crucial for removing the bulk of the air and any large particles of moisture. It prepares the transformer for the more precise evacuation steps that follow.
2. Deep Vacuum Phase: After the rough vacuum is achieved, a diffusion pump or molecular pump is employed to create a high vacuum inside the transformer. This step is necessary to ensure that any remaining gases, especially moisture, are removed to a molecular level. The deep vacuum phase helps in achieving the desired level of cleanliness and ensures that the transformer is ready for oil filling.
3. Transformer Drying: Once a high vacuum is achieved, the transformer is subjected to a drying process. In this step, residual moisture within the transformer is eliminated by heating the transformer components under vacuum conditions. Removing this moisture is critical because even trace amounts of water can negatively affect the insulating properties of the transformer oil, leading to reduced dielectric strength.
4. Oil Filling Under Vacuum: The final stage of the transformer evacuation process involves filling the transformer with insulating oil under vacuum conditions. By performing this step under a vacuum, the risk of introducing air or moisture into the transformer is minimized. This ensures the oil’s purity, enhancing its insulation and cooling properties, which are vital for the transformer’s performance.
Importance of Transformer Evacuation
Vacuum evacuation of transformers is crucial for several reasons, and failing to properly evacuate a transformer can lead to a variety of operational issues. The importance of transformer evacuation can be summarized in the following points:
- Enhancing insulation strength: Removing air and moisture from the transformer tank improves the insulation properties of the transformer oil, which is vital for preventing short circuits and electrical failures.
- Preventing partial discharges: Air gaps inside a transformer can lead to partial discharges, which cause localized heating and degradation of insulation materials. Proper evacuation eliminates these air gaps, reducing the likelihood of partial discharges.
- Improving cooling efficiency: Transformer oil serves a dual purpose of insulation and cooling. In a vacuum environment, the absence of air and contaminants allows the oil to circulate more effectively, improving the transformer’s cooling performance.
- Extending transformer lifespan: By maintaining a contaminant-free environment inside the transformer, vacuum evacuation helps to extend the equipment’s operational life. Reduced risk of electrical breakdowns and overheating means that the transformer can continue to perform reliably for longer periods.
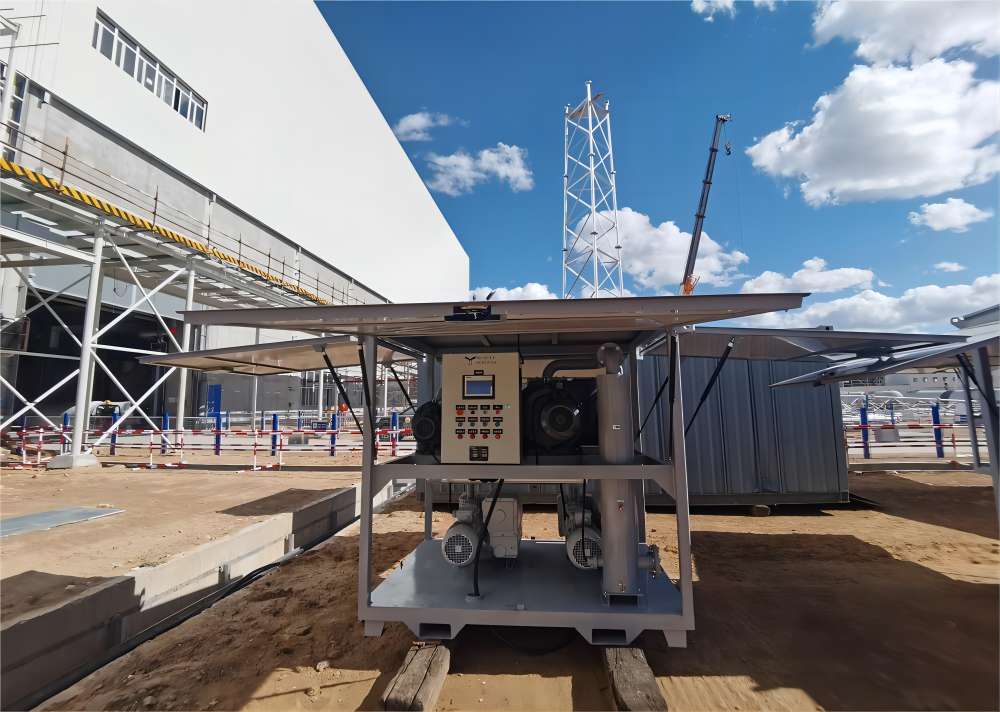
Maintenance and Care of Vacuum Pump Systems
To ensure the reliable operation of a transformer vacuum pump system, regular maintenance and care are essential. A well-maintained vacuum pump system reduces the risk of failures during transformer evacuation and prolongs the lifespan of both the pump and the transformer.
Key Maintenance Practices:
- Oil Level Checks: Vacuum pumps rely on oil for lubrication and sealing. It is important to regularly check the oil levels in the pump and add oil as necessary to prevent damage to the pump components.
- Filter Cleaning: Filters in both the vacuum pump and vacuum piping should be cleaned regularly to prevent blockages and ensure that the system operates efficiently.
- Seal Inspection: Vacuum seals are critical for maintaining the vacuum inside the transformer. Regular inspections should be performed to ensure that seals are intact and not allowing any air to enter the system.
- Replacement of Worn Parts: Vacuum pumps contain several moving parts, such as bearings and seals, which are subject to wear over time. These parts should be replaced as needed to prevent system failure and maintain optimal performance.
As mentioned above, transformer evacuation systems are an essential tool in the manufacturing and maintenance of transformers. By creating a vacuum environment inside the transformer, these systems remove air, moisture, and other contaminants, ensuring that the transformer operates at peak efficiency and reliability. Through a combination of careful system design, regular maintenance, and adherence to proper operating procedures, vacuum pump systems help extend the lifespan of transformers while improving their insulation properties and reducing the risk of failure. As technology continues to advance, transformer vacuum pump systems will remain a critical component in the power industry, enabling the production of more reliable and efficient transformers.