Troubleshooting and Maintenance of Vacuum Pump Units in Power Systems
Table of Contents
Vacuum pump units are essential components in power systems, playing a crucial role in ensuring the efficient and safe operation of electrical equipment. These units are widely used in various applications, including:
- Condenser Vacuuming: In thermal power plants, vacuum pump units are used to maintain a high level of vacuum in the condenser, which improves the efficiency of the steam turbine.
- Transformer Vacuuming: During the manufacturing, installation, and maintenance of transformers, vacuum pump units remove internal moisture and gases to enhance insulation performance.
- Power Cable Vacuuming: Vacuum treatment of high-voltage cables is vital for improving their operational reliability and longevity.
- Vacuum Drying of Electrical Equipment: Vacuum pump units are used to dry electrical equipment, removing moisture to extend their service life and reduce failure rates.
This article aims to systematically introduce the fault diagnosis and maintenance technologies of vacuum pump units in power systems, helping power engineers and technicians better understand and master relevant knowledge, improve fault handling capabilities, and ensure the stable operation of power systems.
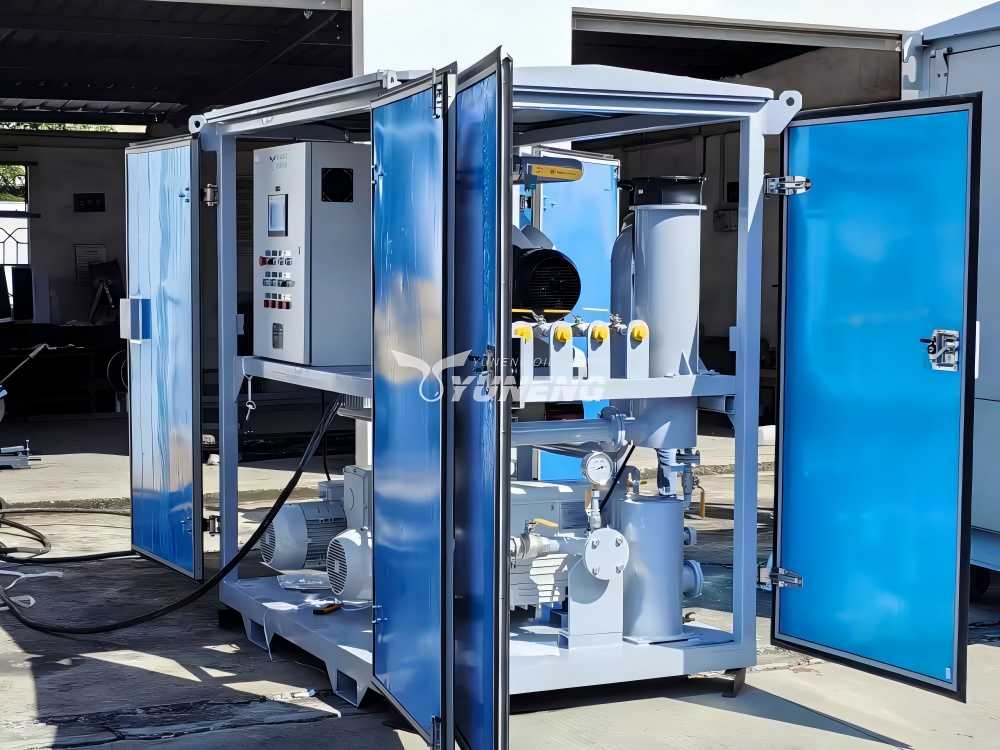
Common Faults and Causes of Vacuum Pump Units
Vacuum pump units, like any mechanical system, may encounter various faults during operation. The common faults and their causes are discussed below:
1. Decrease in Vacuum Pressure
A drop in vacuum pressure is one of the most frequent problems encountered in vacuum pump units. The main causes include:
- Seal Leaks: Aging or damaged seals lead to air ingress, which reduces the vacuum level.
- Gas Leaks: Loose or damaged flanges and pipeline joints can cause gas leaks, lowering the vacuum.
- Oil Contamination: The presence of water, impurities, or degraded oil affects the pump’s vacuum performance.
- Wear in Pump Components: The internal components of the pump may wear over time, increasing gaps and reducing the pump’s efficiency.
- Clogged Inlet: Foreign objects may block the filter or intake pipes, restricting airflow and reducing vacuum pressure.
2. Pump Overheating
Pump overheating is another significant issue, often caused by the following factors:
- Insufficient or Contaminated Oil: Low oil levels or poor-quality oil impair heat dissipation, leading to overheating.
- Motor Overload: Overloading the motor or motor faults can increase the heat generation in the pump.
- High Ambient Temperature: If the operating environment exceeds the rated temperature range, the pump will struggle to dissipate heat effectively.
3. Abnormal Noise or Vibration
Vacuum pumps may produce abnormal noise or vibrations, typically due to the following reasons:
- Loose Components: Loose internal or external components of the pump can cause abnormal noise and vibrations during operation.
- Imbalance in Rotor: An unbalanced rotor, or damage to the rotor, may lead to vibrations and noise.
- Bearing Failure: Worn or damaged bearings can cause instability and noise in the pump.
- Foreign Objects in the Pump: Any debris or foreign material entering the pump can disrupt its normal operation, causing unusual sounds or vibrations.
4. Motor Failures
Motor failures are another common fault in vacuum pump systems. These issues may arise from:
- Burnt Windings: Overloading the motor or damage to insulation can result in the winding burning out.
- Bearing Damage: Wear and tear on motor bearings can result in improper motor function, increased friction, and potential failure.
- Power Supply Issues: Voltage instability, phase loss, or power supply failures can cause motor malfunction or damage.
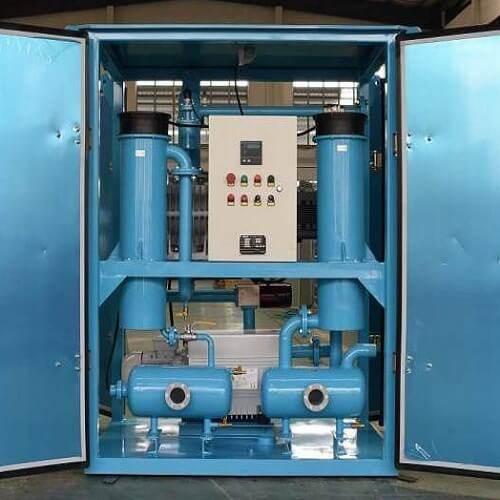
Fault Diagnosis Methods
Effective fault diagnosis is critical in identifying and resolving issues in vacuum pump units. Several methods can be employed to diagnose faults:
1. Observation Method
The observation method is a simple yet essential diagnostic approach. Technicians can assess the pump’s condition by:
- Inspecting the Pump’s Appearance: Check for visible leaks, cracks, or other forms of physical damage.
- Examining Oil Conditions: Observe the oil level and color to determine if it is within the normal range and free from contamination.
- Observing Motor Operation: Monitor the motor for smooth operation and any signs of irregular behavior.
2. Auditory Diagnosis
The auditory diagnosis method involves listening to the sounds emitted by the pump and motor to identify potential issues:
- Pump Sounds: Unusual noises such as grinding, knocking, or high-pitched sounds may indicate problems with the pump’s internal components.
- Motor Sounds: Similarly, strange noises from the motor can suggest issues such as bearing wear, rotor imbalance, or electrical malfunctions.
3. Measurement Method
This method involves using measuring instruments to gather data and assess whether the pump is operating within acceptable limits:
- Vacuum Measurement: Use a vacuum gauge to measure the vacuum level and compare it with the required specifications.
- Temperature Measurement: A thermometer can be used to measure the pump’s temperature, helping to identify overheating issues.
- Motor Current and Voltage Measurement: Use ammeters and voltmeters to ensure the motor is receiving the correct current and voltage levels.
4. Instrumental Detection Method
For more precise diagnostics, specialized instruments are used:
- Vibration Analyzer: This device helps detect imbalance or other mechanical faults in the pump and motor by measuring vibrations.
- Motor Testing Equipment: Instruments like insulation testers and power analyzers can help identify issues with the motor’s electrical components.
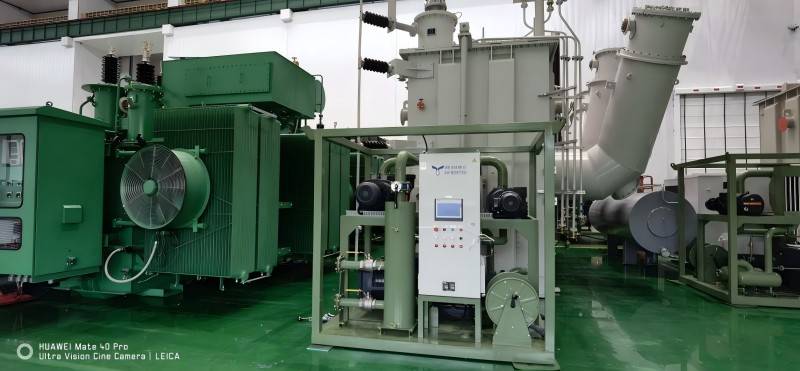
Maintenance Methods
Once a fault is identified, appropriate maintenance procedures must be followed. Some common maintenance methods include:
1. Seal Leak Maintenance
- Replace Seals: If seal leaks are detected, it is essential to replace damaged or aged seals to restore the pump’s vacuum performance.
- Tighten Flanges and Joints: Loose or damaged flanges and pipe connections should be properly tightened or replaced to prevent gas leakage.
2. Oil Contamination Maintenance
- Change the Oil: Contaminated oil should be replaced with fresh, high-quality oil to restore the pump’s lubrication and cooling properties.
- Clean the Pump Internals: In cases where oil contamination is severe, cleaning the pump internals is necessary to remove any debris or moisture that may have accumulated inside the pump.
3. Pump Wear Maintenance
- Replace Worn Components: Any internal pump components that show signs of wear, such as vanes, bearings, or seals, should be replaced promptly.
- Repair Worn Areas: Some wear can be repaired through resurfacing or reconditioning, but severely damaged parts will need to be replaced.
4. Motor Maintenance
- Repair or Replace the Motor: If a motor fails, it may need to be repaired or completely replaced depending on the extent of the damage. For example, if the windings are burnt, the motor may need rewinding or replacement.
- Check Electrical Connections: Ensure that electrical connections are intact and there are no issues with the power supply, such as voltage fluctuations or phase loss.
5. Bearing Maintenance
- Replace Damaged Bearings: Bearings that are worn or damaged should be replaced immediately to prevent further damage to the pump’s operation.
- Lubrication: Bearings should be lubricated regularly with the appropriate grease or oil to minimize wear and ensure smooth operation.
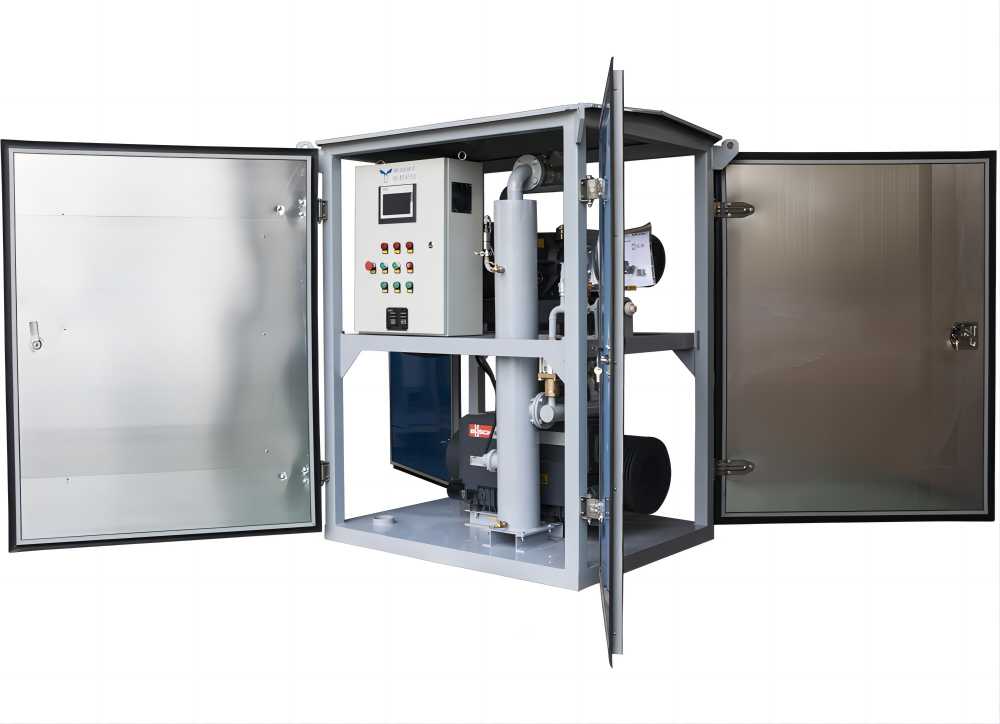
Preventive Maintenance
Regular preventive maintenance is key to prolonging the lifespan of vacuum pump units and preventing unexpected failures. Below are some best practices for preventive maintenance:
1. Regular Oil Checks and Replacements
- Monitor Oil Levels and Quality: Check the oil level and quality regularly to ensure that it remains clean and at the correct level. If the oil appears contaminated or degraded, replace it promptly to avoid damage to the pump.
- Change Oil Periodically: Even if the oil looks fine, it should be changed at regular intervals according to the manufacturer’s recommendations.
2. Regular Seal Checks and Replacements
- Inspect Seals for Wear: Over time, seals can deteriorate, leading to leaks. It is important to inspect seals regularly and replace them if necessary to maintain the vacuum level.
- Check for External Leaks: Visually inspect the pump system for signs of leaks at flanges, joints, and connections. Tightening or replacing worn seals can prevent major issues.
3. Regular Motor Inspections
- Inspect Motor for Wear: Check the motor for signs of wear, especially the bearings, windings, and insulation. Early detection of wear can help prevent costly motor failures.
- Monitor Electrical Parameters: Regularly measure voltage and current to ensure that the motor is operating within its rated specifications.
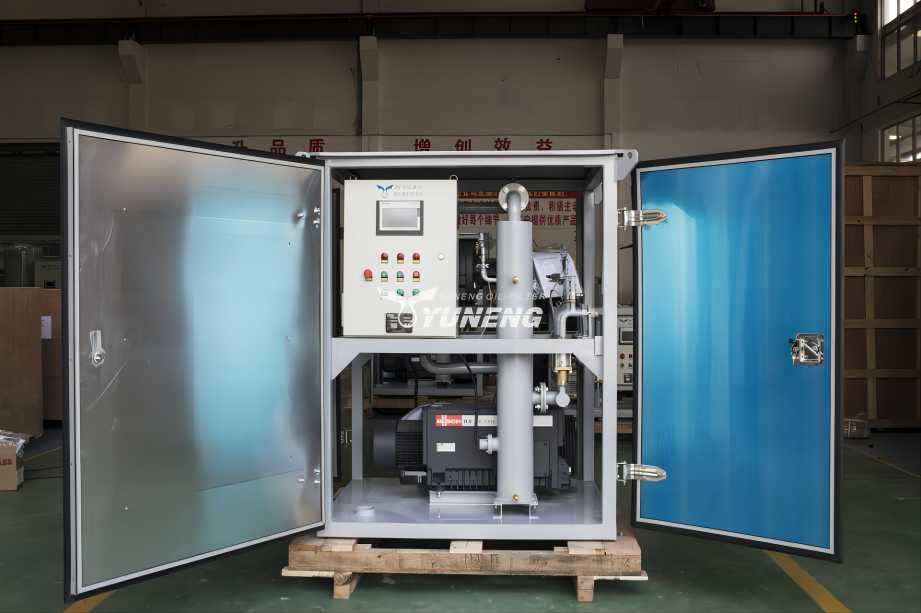
Precautions and Safety Measures
1. Safety Operating Procedures
Before performing any maintenance or troubleshooting, always follow proper safety protocols:
- Disconnect Power Supply: Always ensure that the power supply is disconnected before conducting any repairs to avoid the risk of electrical shock or accidental start-up.
- Use Proper Personal Protective Equipment (PPE): Technicians should wear appropriate PPE, including gloves, goggles, and protective clothing, to minimize the risk of injury.
2. Principles for Component Replacement
When replacing components, it is important to follow these principles:
- Use Original or Equivalent Parts: Always replace components with the same type or equivalent to ensure compatibility with the system.
- Check for Proper Fit: When installing new parts, ensure they fit correctly and are properly secured to avoid future mechanical issues.
3. Post-Maintenance Testing
After performing repairs or replacements, the system should undergo testing to ensure it is functioning as expected:
- Conduct Test Runs: After maintenance, the pump should be operated in normal working conditions to verify its performance.
- Monitor for Abnormalities: During the test run, monitor the pump for any signs of abnormal noise, vibration, or temperature increase. If any issues arise, further adjustments should be made.
Troubleshooting and maintenance of vacuum pump units in power systems are essential for ensuring the safe and stable operation of power systems. By systematically understanding common fault types, mastering detailed diagnostic methods, and comprehensive maintenance measures, fault handling capabilities can be effectively improved. At the same time, strengthening preventive maintenance, and regularly inspecting and maintaining vacuum pump units can effectively extend equipment lifespan and improve operational efficiency. With the continuous development of technology, the maintenance technology of vacuum pump units will continue to advance, providing more reliable guarantees for the safe and stable operation of power systems.