Turbine Oil Purification Best Practices for Optimal Performance
Turbine oil plays a role in the operation of turbines, ensuring that they run efficiently and with minimal wear and tear. However, over time, turbine oil can become contaminated, leading to decreased performance and potential damage. Implementing best practices for turbine oil purification is essential to maintain optimal performance.
Here we talk about some best practices to ensure the optimal performance of your turbine oil.
Contamination Issues in Turbine Oil
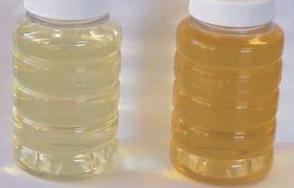
First of all, we must know that there are several factors that can contribute to turbine oil contamination:
- Oxidation: Exposure to air causes oil to break down, forming sludge and varnish deposits that can restrict oil flow and reduce heat transfer. This sludge can clog filters and reduce the oil’s ability to remove heat from critical turbine components.
- Ingress of Water: Water contamination can lead to several problems in turbine oil systems. Water can cause foaming, reducing lubrication properties by preventing the oil from forming a continuous film on metal surfaces. It can also accelerate corrosion by promoting rust formation on turbine components. Furthermore, water contamination can create a breeding ground for microorganisms that can further degrade the oil.
- Dirt and Dust: Airborne particles can enter the system during maintenance or through leaks. These contaminants can cause abrasive wear on turbine components, accelerating component wear and reducing efficiency. In severe cases, large particles can even jam or damage turbine bearings.
- Metal Wear Debris: Friction within the turbine generates microscopic metal particles that can contaminate the oil. The presence of excessive wear debris can indicate potential problems within the turbine, such as bearing wear or gear scuffing. Early detection of these issues through oil analysis allows for corrective actions to be taken before major failures occur.
Turbine Oil Purification Methods
Various methods can be employed to address specific types of contamination, ensuring that the oil remains effective in its lubrication and heat transfer roles. Here’s a deeper dive into the three main methods and their strengths.
- Centrifugation: This workhorse method utilizes a high-speed centrifuge to separate contaminants based on density. The oil spins rapidly, forcing denser contaminants like water, dirt, and metal wear debris outwards, where they are collected in a separate chamber. Centrifugation is effective for removing a wide range of particulate contaminants and is a common choice for routine purification.
- Vacuum Dehydration: This method specifically targets water contamination and dissolved gases. The oil is heated under a vacuum, lowering its boiling point and causing water and gases to vaporize and be removed. Vacuum dehydration is particularly useful for removing moisture caused by condensation or leaks, which can lead to foaming and corrosion. It can also remove dissolved air, which can accelerate oxidation and degrade the oil’s lubricating properties.
- Fullers Earth Filtration: This method employs a clay filtration medium known as Fuller’s earth. The oil is passed through this clay, which acts as a magnet for polar contaminants like oxidation products (varnish and sludge) and some water molecules. Fullers earth filtration is ideal for removing these breakdown products that can thicken the oil, reduce its effectiveness, and contribute to deposit formation. However, it’s less effective for removing particulate contaminants like dirt or metal wear debris.
In practical problems, choosing the right method depends on the specific type and severity of pollutants present in turbine oil. You can use oil analysis to help you identify the main pollutants and choose the purification technology that suits you best.
Best Practices for Turbine Oil Purification
Turbine Oil Filtration Machine
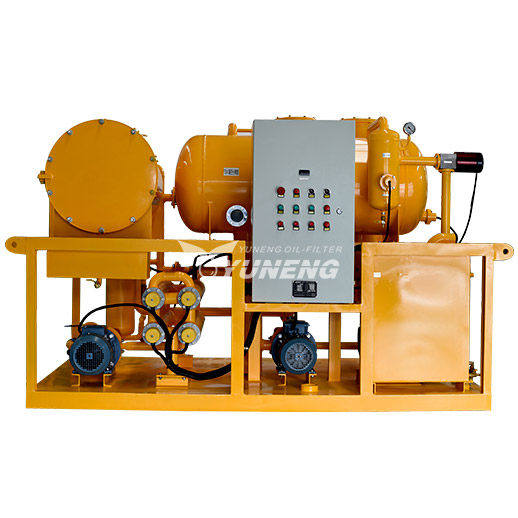
Before we delve into the specifics of best practices, let’s understand the workhorse behind the purification process: the turbine oil filtration machine.
These machines come in various configurations, but all share the same mission: to banish contaminants from your oil. Centrifuges spin oil at high speeds, flinging dirt, water, and metal debris outwards for collection. Vacuum dehydrators target moisture and dissolved gases, using heat and a vacuum to remove them. Fullers earth filters employ a special clay that attracts and removes oxidation products and some water, keeping your oil free of sludge and varnish. Choosing the right machine depends on the dominant contaminants in your oil, as identified by oil analysis. With the right filtration technology company as your partner, clean and healthy turbine oil is within reach.
Oil Analysis and Monitoring
Regular oil analysis is the cornerstone of any effective purification strategy. Schedule oil sampling at prescribed intervals, typically monthly or quarterly depending on your turbine’s operating conditions. This analysis serves as a vital diagnostic tool, revealing a wealth of information about your turbine oil’s health:
- Identifying Contaminants: The analysis pinpoints the presence and severity of various contaminants like oxidation products (varnish and sludge), water, wear debris, and soot.
- Understanding Root Causes: The analysis helps identify the root cause of contamination. Is it excessive heat causing oxidation? Water ingress from leaks or condensation? Normal wear and tear generating metal particles? This knowledge empowers you to address the root cause and prevent future issues.
- Tracking Trends: By monitoring oil analysis results over time, you can track trends in contamination levels. This allows you to predict when purification becomes necessary and avoid reactive maintenance.
- Selecting the Right Purification Method: The analysis results are your roadmap for choosing the most effective purification technique. For example, high water content indicates a need for vacuum dehydration, while excessive varnish points towards Fullers earth filtration.
Proper Purification Techniques
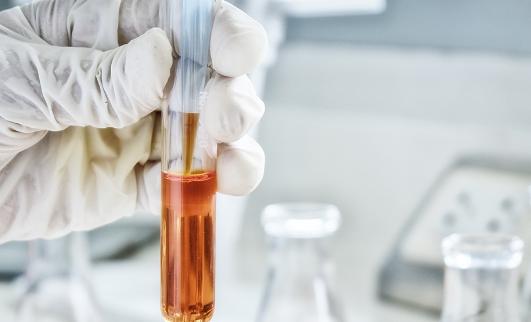
Once oil analysis has identified the dominant contaminants, it’s time to choose the most appropriate purification method. Here’s how to ensure the purification process is conducted effectively:
- Matching Method to Menace: Don’t treat all contamination with a one-size-fits-all approach. Here’s a breakdown of the best method for each common contaminant:
- Particulates: Centrifugation is your champion. Its ability to separate dense contaminants makes it ideal for removing dirt, dust, and metal wear debris.
- Water: When water is the primary concern, vacuum dehydration comes to the rescue. By removing moisture and dissolved gases, it prevents foaming and corrosion.
- Oxidation Products: If oxidation is a major culprit, Fuller’s earth filtration steps up. This method effectively removes varnish and sludge, restoring the oil’s viscosity and lubricating properties.
- System Preparation: Before purification, ensure the oil system is clean and free of large particles that could clog filters during the process. Consider flushing the system to remove any settled contaminants.
- Temperature Matters: Maintain the oil system within the recommended temperature range during purification. This ensures optimal performance of the purification equipment and avoids potential oil degradation at excessive temperatures.
- Flow Rate Control: Maintain the correct oil flow rate through the purification system. Following the manufacturer’s recommendations ensures efficient contaminant removal without stressing the system.
- Post-Purification System Flush: Consider flushing the oil system after purification to remove any residual contaminants or cleaning byproducts that may have entered the system during the process.
Oil System Maintenance
A comprehensive turbine oil management strategy goes beyond just purification. Here are some additional practices to keep your oil system healthy and minimize contamination:
- Regular System Inspections: Schedule regular inspections of the oil system for leaks or signs of contamination ingress, such as water accumulation in the reservoir.
- Proper Storage: Store spare oil in clean, dry, and sealed containers to prevent contamination before use. Moisture absorption or airborne contaminants can compromise the oil’s quality.
- Moisture Control: Implement measures to prevent moisture from entering the oil system, such as using breathers with desiccant cartridges. These cartridges absorb moisture from the incoming air, preventing condensation within the system.
- Scheduled Oil Changes: While purification extends oil life, eventually, even the best-maintained oil will degrade. Schedule oil changes based on the manufacturer’s recommendations and oil analysis results.
Conclusion
Following these turbine oil purification best practices unlocks a treasure chest of benefits: optimal turbine performance, extended equipment life, minimized downtime, and reduced maintenance costs. By proactively managing your turbine oil, you safeguard your investment and keep your turbines humming for years to come.