Understanding Oil Purification Systems and Their Benefits: A Focus on Transformer Oil
Maintaining the health of your oil is crucial for the efficient operation of various machinery and equipment. Oil purification systems play a vital role in achieving this by removing impurities and contaminants, ultimately extending oil life, enhancing performance, and minimizing environmental impact. This article provides an overview of oil purification systems, highlighting their benefits and focusing specifically on transformer oil purification machines. Additionally, it offers guidance on navigating the factors to consider when making informed decisions about these systems.
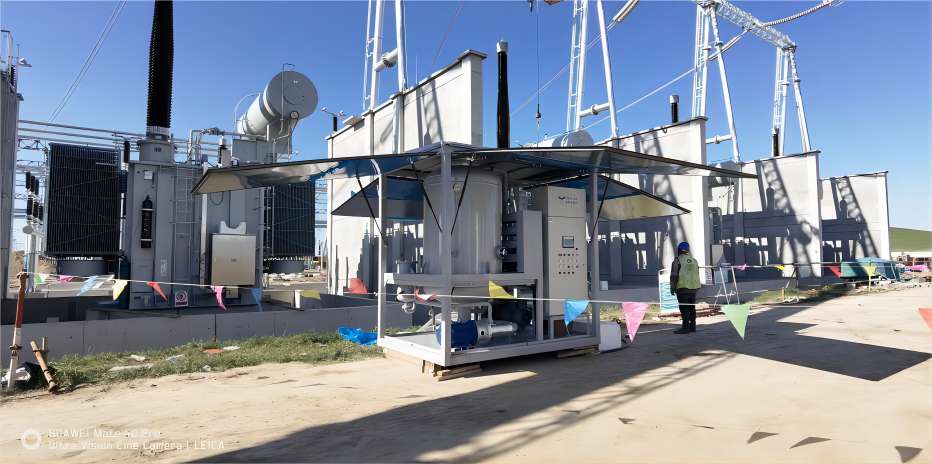
Types of Oil Purification Systems
Oil purification systems are not one-size-fits-all solutions. They come in various configurations, each specifically designed to tackle the unique challenges and requirements of different oil types and applications. Here’s a closer look at the two prominent categories:
1. Industrial Oil Purification Systems
These versatile systems are built to handle a wide range of oils commonly encountered in industrial settings, including:
- Hydraulic oil: This type of oil plays a crucial role in hydraulic systems, transmitting power by transferring pressure through a liquid medium. Industrial oil purification systems are equipped to remove contaminants that can impede this process, ensuring the smooth and efficient operation of hydraulic machinery.
- Lubricating oil: This oil serves the essential function of minimizing friction, wear, and heat generation in various components of machinery. Industrial oil purification systems help maintain the quality of lubricating oil by eliminating contaminants that can contribute to increased friction, premature wear, and overheating, ultimately protecting machinery from damage and ensuring optimal performance.
- Coolant: This fluid is used to regulate temperature in engines and other equipment, preventing overheating and ensuring proper operation. Industrial oil purification systems can remove contaminants from coolants that can hinder their ability to effectively transfer heat, safeguarding equipment from thermal damage and maintaining optimal operating temperatures.
Industrial oil purification systems employ various techniques to achieve optimal oil cleaning, including:
- Filtration: This process removes solid particles and impurities from the oil using filter media with varying pore sizes, depending on the specific contaminants targeted.
- Dehydration: This technique removes water content from the oil, which can be detrimental to its performance and contribute to corrosion and other issues.
- Degasification: This process eliminates dissolved gases from the oil, which is particularly important for certain applications like transformer oil, as these gases can negatively impact its insulating properties.
2. Transformer Oil Purification Machines
These specialized systems are specifically designed to address the unique needs of transformer oil. Transformer oil serves the critical dual function of insulating and cooling electrical transformers. Maintaining the cleanliness and quality of transformer oil is essential for the safe and reliable operation of these vital components in the electrical grid.
Transformer oil purification machines typically utilize a combination of the following techniques to remove contaminants from transformer oil:
- Filtration: Similar to industrial systems, filtration removes solid particles and impurities that can degrade the oil’s insulating properties.
- Dehydration: Removing water content is crucial for transformer oil, as water can compromise its insulating ability and lead to electrical arcing and potential transformer failure.
- Vacuum Degasification: This process is particularly important for transformer oil purification, as it effectively removes dissolved gases that can accumulate over time and significantly impact the oil’s insulating capabilities. By creating a vacuum environment, these machines facilitate the efficient removal of these dissolved gases, ensuring the continued effectiveness of the oil as an insulator.
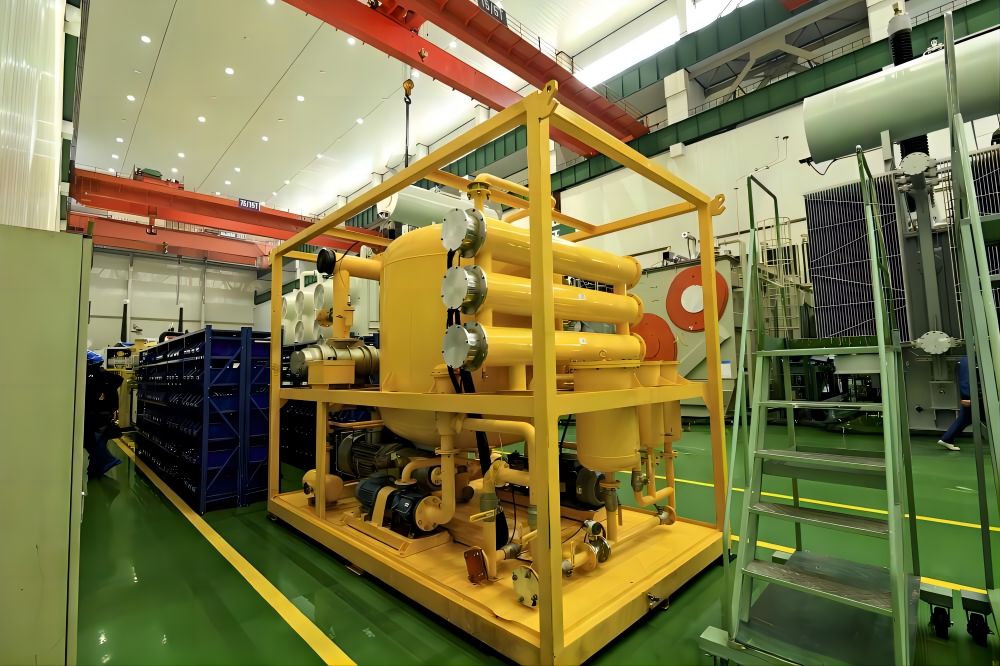
Benefits of Using Oil Purification Systems
Investing in an oil purification system offers a range of concrete benefits that positively impact both your operational bottom line and environmental sustainability. These advantages can be categorized into three key areas:
1. Extended Oil Lifespan and Cost Saving
Regularly purifying oil significantly extends its usable life by removing contaminants that degrade its performance and lead to premature breakdown. This translates to substantial cost savings in several areas:
- Reduced need to purchase new oil: By extending the lifespan of existing oil, you significantly decrease the frequency of oil changes, minimizing your expenditure on purchasing new oil.
- Lower disposal costs: Used oil requires proper disposal to avoid environmental contamination. Oil purification reduces the generation of waste oil, minimizing the associated disposal costs.
- Decreased labor expenses: Frequent oil changes involve labor costs associated with draining, replacing, and disposing of used oil. Oil purification systems minimize the need for frequent changes, reducing these labor expenses.
2. Improved Efficiency and Enhanced Performance
Clean oil ensures optimal efficiency of your equipment by:
- Reduced friction and wear: Contaminants in oil can increase friction between moving parts, leading to wear and tear, and decreased efficiency. Oil purification removes these contaminants, allowing equipment components to operate smoothly with minimal friction, resulting in improved overall efficiency.
- Prevention of breakdowns and malfunctions: Contaminated oil can contribute to equipment breakdowns and malfunctions, leading to production downtime and potential repair costs. Oil purification systems help prevent these issues by maintaining the cleanliness and quality of the oil, ensuring smooth equipment operation, and minimizing the risk of breakdowns.
- Enhanced heat transfer in cooling systems: In cooling systems, contaminated coolant can hinder its ability to effectively transfer heat, potentially leading to overheating and equipment damage. Oil purification systems remove contaminants from coolants, ensuring optimal heat transfer and safeguarding equipment from thermal issues.
3. Increased Environmental Benefits
- Reduced Waste Generation: Oil purification plays a crucial role in environmental protection by minimizing the generation of waste oil. This used oil requires proper disposal to avoid environmental contamination, which can be a costly and complex process. By extending the lifespan of existing oil, oil purification systems significantly reduce the amount of waste oil generated, minimizing the environmental impact associated with its disposal.
- Lowered Demand for New Oil Extraction and Refining: The demand for new oil is directly linked to the consumption of oil. By extending the lifespan of existing oil through purification, the need for extracting and refining new oil is reduced. This contributes to a lower environmental impact associated with oil extraction and refining processes, which can have significant negative consequences such as air and water pollution, habitat destruction, and greenhouse gas emissions.
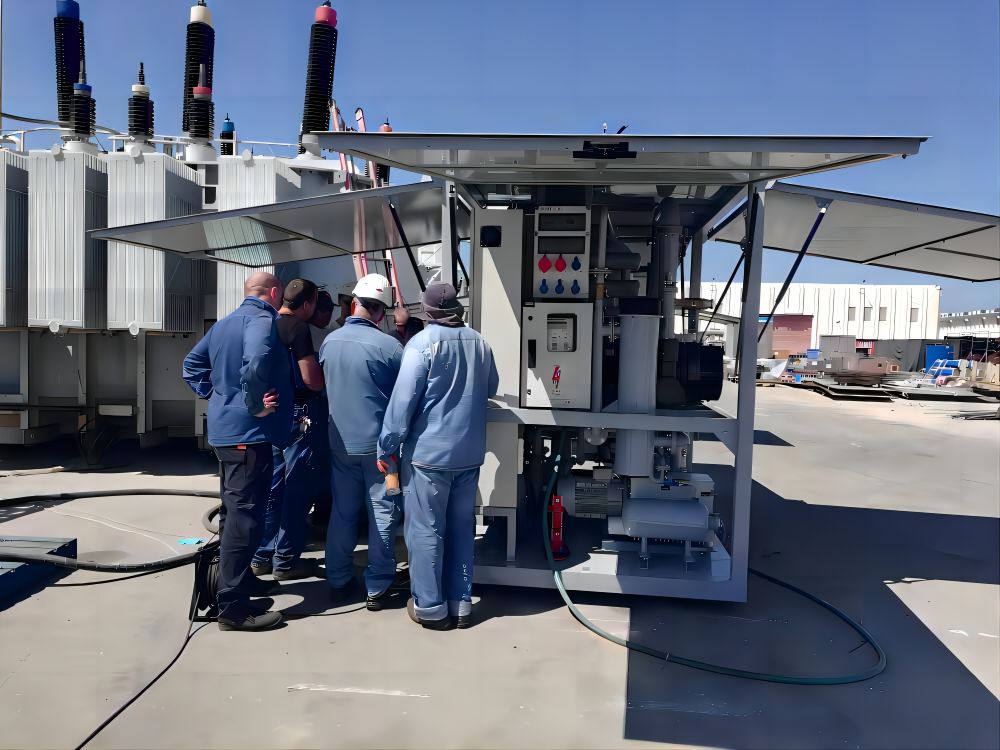
Addressing the Specific Needs of Transformer Oil: Specialized Features in Focus
Transformer oil purification machines are designed specifically to address the unique requirements of transformer oil, ensuring its continued effectiveness and safeguarding the safe and efficient operation of transformers. Here, we delve deeper into two key features incorporated into these machines:
1. Vacuum Degasification: A Crucial Step for Maintaining Insulating Properties
Transformer oil plays a crucial role in electrical transformers, acting as both an insulator and a coolant. To perform these functions effectively, the oil needs to be free of dissolved gases. These gases, which can accumulate over time due to various factors like exposure to air or electrical discharge, can significantly compromise the oil’s insulating properties. This can lead to a phenomenon known as electrical arcing, where electricity jumps across gaps in the insulation, potentially causing damage to the transformer and even leading to complete failure.
Transformer oil purification machines employ vacuum degasification to address this critical challenge. This process involves creating a vacuum environment within the machine. The oil is then introduced into this low-pressure environment, causing the dissolved gases to come out of the solution and be removed from the oil. By effectively eliminating these dissolved gases, vacuum degasification ensures that the transformer oil retains its insulating capabilities, preventing electrical arcing and safeguarding the safe and reliable operation of the transformer.
2. On-line Operation: Enabling Continuous Maintenance without Disruption
Traditional transformer oil purification methods often require taking the transformer offline, which can be a disruptive and costly process. This is particularly true for large transformers, where the process of taking them offline, purifying the oil, and then bringing them back online can significantly impact the power supply and lead to lost productivity.
Certain transformer oil purification machines offer the advantage of on-line operation. This feature allows the oil to be purified while the transformer remains in operation. This is achieved by connecting the purification machine directly to the transformer’s oil circulation system. The oil is then continuously cycled through the machine, where it undergoes purification, and then returned back to the transformer without interrupting its operation.
On-line operation provides several benefits, including:
- Reduced downtime: By eliminating the need to take the transformer offline, online operation minimizes downtime and associated productivity losses.
- Cost savings: Reduced downtime translates to cost savings on labor and lost production.
- Improved operational efficiency: On-line operation allows for continuous maintenance of the transformer oil, contributing to its overall health and efficiency.
These specialized features highlight the unique capabilities of transformer oil purification machines, enabling them to address the specific needs of transformer oil and play a crucial role in maintaining the safe, efficient, and reliable operation of electrical transformers.
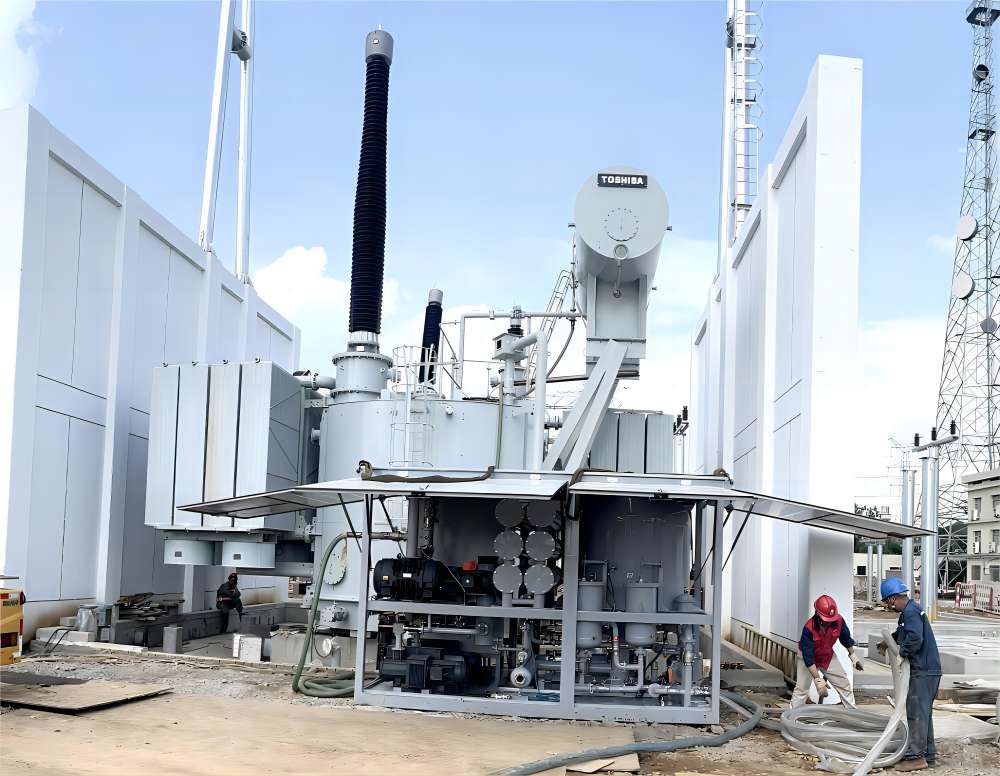
Choosing the Right Oil Purification System
Choosing the appropriate oil purification system requires careful consideration of several key factors to ensure it aligns perfectly with your specific needs and budget. Here’s a breakdown of the crucial elements to evaluate when making this important decision:
1. Cost of Oil Purification Systems
The price of oil purification systems can vary significantly, influenced by several key factors:
- Size and Capacity: Larger systems capable of processing higher volumes of oil naturally carry a higher cost compared to smaller systems with lower processing capabilities.
- Features: Systems equipped with advanced features, such as online operation or specialized filtration capabilities, typically command a higher price point compared to systems with basic functionalities.
- Brand and Manufacturer: Different brands and manufacturers may offer varying pricing strategies based on their market positioning, brand reputation, and specific features included in their systems.
2. Conducting Thorough Research
To make an informed decision, it’s crucial to conduct thorough research and gather comprehensive information on available options. This includes:
- Consulting with industry experts: Seek guidance from professionals with expertise in oil purification systems to gain insights into the different types of systems available, their functionalities, and their suitability for your specific application.
- Gathering product information: Research different brands and manufacturers to compare their product offerings, technical specifications, and available features.
- Reviewing customer reviews and feedback: Reading reviews and testimonials from existing users can provide valuable insights into the real-world performance and reliability of different systems.
3. Obtaining Quotes from Reputable Suppliers
Once you have a shortlist of potential systems based on your research, it’s essential to obtain quotes from reputable suppliers. This allows you to compare pricing, terms, and available services offered by different vendors. When requesting quotes, ensure you provide specific details about your oil purification needs, including the type of oil you intend to purify, desired processing capacity, and any specific features you require.
4. Evaluating Your Specific Needs
Carefully evaluate your specific needs when making your final decision. Consider factors such as:
- The type of oil you need to purify: Different oil types may necessitate specific features or functionalities in the purification system.
- Required processing capacity: Choose a system with sufficient capacity to handle your expected oil volume requirements.
- Budgetary constraints: Select a system that aligns with your allocated budget while meeting your essential needs.
- Desired features: Consider the specific features crucial for your operation, such as online operation or specific filtration capabilities.
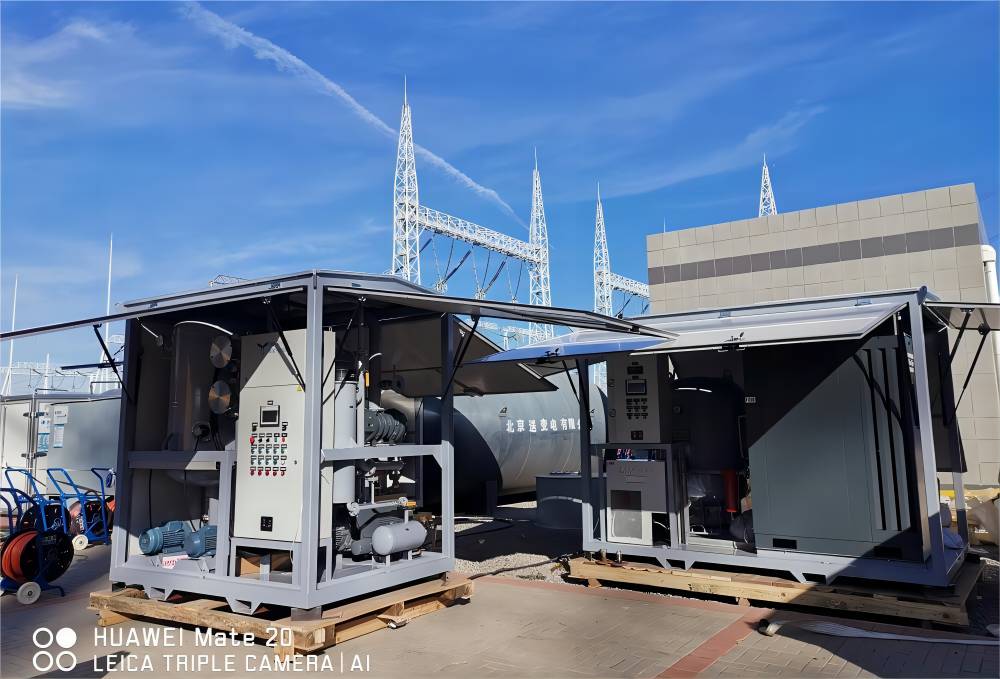
Conclusion
Oil purification systems are invaluable tools for maintaining the health of various oils used in industrial applications and transformers. Implementing these systems not only translates to cost savings and improved equipment performance but also contributes to environmental protection by reducing waste oil generation and the need for new oil extraction. By understanding the different types of oil purification systems, the benefits they offer, and the key factors to consider when choosing a system, you can make informed decisions that ensure the smooth operation of your equipment while contributing to a more sustainable future.