Vacuum Pumping Systems: From Basics to Transformers
The world around us is filled with air, a mixture of various gases exerting constant pressure. However, there are numerous applications where achieving a near-perfect vacuum, a space devoid of most gases, becomes crucial. This is where vacuum pumping systems come into play. These systems are the workhorses behind various processes, enabling the creation and maintenance of controlled environments with minimal gas pressure.
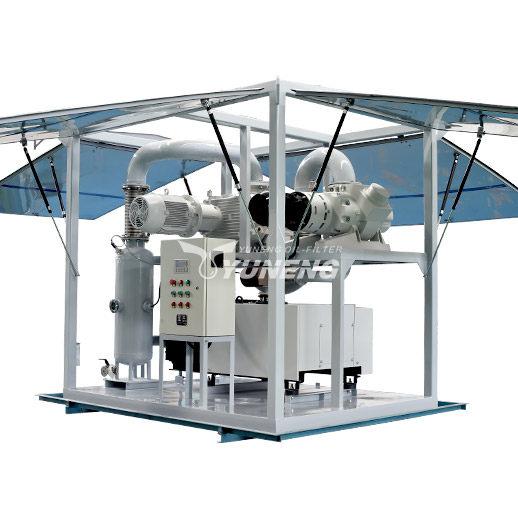
Core Components of a Vacuum Pumping System
A vacuum pumping system is an assembly of various components working together to achieve and maintain a desired level of vacuum. Let’s delve into the two key components: the vacuum pump unit and the vacuum oil purifier.
1. The Heart of the System: Vacuum Pump Unit
The vacuum pump unit is the engine that drives the entire system. Its function is to extract gas molecules from a chamber, thereby reducing the pressure within. Different types of vacuum pumps exist, each suited for specific pressure ranges and applications. Here’s a breakdown of some common types:
- Rotary Vane Pumps: These pumps utilize a rotating vane that traps gas within a chamber and then transfers it to the exhaust. They are known for their simple design, reliability, and ability to achieve rough vacuum (pressures in the range of millitorr, denoted by mTorr). However, they are not ideal for ultra-high vacuum applications due to limitations arising from internal friction and oil backstreaming (oil vapor entering the vacuum chamber).
- Piston Pumps: Similar to rotary vane pumps, piston pumps use a reciprocating piston to trap and remove gas. They offer a cleaner vacuum compared to rotary vane pumps and can achieve lower pressures. However, their moving parts can introduce vibrations and require more maintenance.
- Diffusion Pumps: These pumps employ high-speed jets of vapor (often oil vapor) to create a momentum transfer. Gas molecules collide with the vapor stream, transferring their momentum and getting pumped out of the chamber. Diffusion pumps excel at achieving high and ultra-high vacuum (pressures in the range of microns, denoted by µm, and nanotorr, denoted by nTorr). However, they require a backing pump (typically a rotary vane pump) to remove the initial load of gas and have operational complexities.
- Turbomolecular Pumps (Turbo Pumps): These pumps utilize high-speed turbine blades to impart momentum to gas molecules, similar to a fan pushing air. They offer clean, oil-free operation and are ideal for high and ultra-high vacuum applications. However, they tend to be more expensive compared to other pump types.
Selecting the right vacuum pump unit is essential for a successful system. Consider the desired pressure range, application requirements (cleanliness, pumping speed), and operational budget when making your choice.
2. Maintaining Cleanliness: Vacuum Oil Purifier
Many vacuum pumps, particularly rotary vane and diffusion pumps, rely on oil for lubrication and sealing. However, oil can become contaminated with moisture, air, and other impurities over time. This not only reduces the pump’s efficiency but can also lead to breakdowns and performance issues. Here’s where a vacuum oil purifier steps in.
A vacuum oil purifier is a device specifically designed to remove contaminants from used vacuum pump oil. It typically employs a combination of filtration and degassing techniques. Filtration removes particulate matter from the oil while degassing eliminates dissolved gases like water vapor and air. These processes help to maintain the oil’s viscosity, lubricity, and insulating properties, ultimately extending the lifespan of the vacuum pump and ensuring optimal performance.
The benefits of using a vacuum oil purifier are numerous. It reduces maintenance costs by minimizing pump breakdowns and extending oil change intervals. Additionally, clean oil improves pump efficiency, leading to faster pumping times and lower energy consumption.

Specialized Applications: Transformer Vacuum Pump
Transformers are vital components in electrical power transmission and distribution systems. However, over time, they can accumulate moisture and air within their insulation systems. This can lead to electrical breakdowns, reduced efficiency, and ultimately, equipment failure. To prevent such issues, transformer maintenance procedures often involve using specialized vacuum pumps.
1. The Role of Vacuum in Transformer Maintenance
During transformer maintenance, a vacuum pump is used to remove moisture and air from the transformer’s internal insulation system. This process, called vacuum dehydration, is crucial for several reasons. Moisture can degrade the insulating properties of the oil used in transformers, leading to electrical leakage and potential short circuits. Air, on the other hand, can promote oxidation of the transformer oil, further accelerating its degradation. By removing these contaminants, vacuum dehydration helps to maintain the integrity of the transformer’s insulation system, ensuring its reliable operation and extending its lifespan.
2. Specific Features of Transformer Vacuum Pumps
Transformer vacuum pumps are designed specifically for the demands of transformer maintenance. Here are some key features that distinguish them from general-purpose vacuum pumps:
- High Pumping Speed: Transformers can be large and contain significant volumes of air and moisture. To efficiently remove these contaminants within a reasonable timeframe, transformer vacuum pumps require high pumping speeds. This allows them to evacuate large volumes of gas quickly, minimizing downtime during transformer maintenance.
- Durability for On-Site Operations: Transformer maintenance is often performed on-site, sometimes under challenging environmental conditions. Transformer vacuum pumps are designed to be robust and handle the wear and tear associated with field use. They may incorporate features like heavy-duty construction, weatherproofing, and transportable designs for ease of movement.
- Oil Filtration Integration: As discussed earlier, maintaining clean oil is crucial for optimal performance and lifespan of any vacuum pump. Transformer vacuum pumps may come equipped with integrated oil filtration systems. This allows for continuous oil purification during operation, minimizing contamination and extending oil change intervals.
- Vacuum Level Monitoring and Control: Precise control over the vacuum level is critical during transformer dehydration. Transformer vacuum pumps typically include built-in gauges and control systems that allow operators to monitor the vacuum level in real time and adjust pump operation as needed. This ensures proper dehydration without subjecting the transformer to excessive vacuum, which could damage its insulation system.
- Safety Features: Since transformer oil is flammable, safety is paramount during maintenance procedures. Transformer vacuum pumps may incorporate features like explosion-proof designs, high-temperature shut-off switches, and oil spill containment systems to minimize potential hazards.
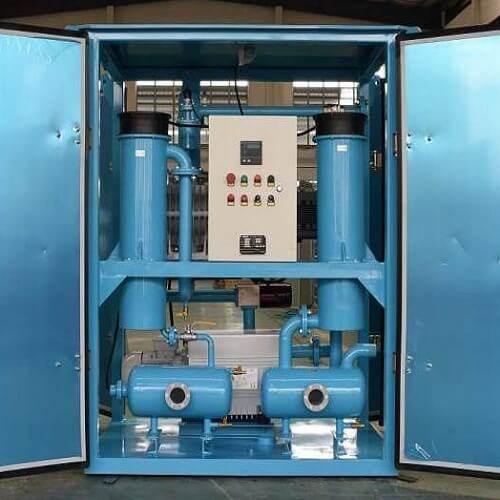
Finding a Transformer Vacuum Pump Unit from Yuneng
Yuneng is a manufacturer specializing in transformer oil purification equipment, including vacuum pumping systems specifically designed for transformer maintenance. Their ZJ Series vacuum pump unit offers a range of transformer vacuum pump units with varying pumping speeds and capacities to cater to different transformer sizes and requirements. These units boast features like high pumping speed for efficient dehydration, robust construction for on-site use, and integrated oil filtration for extended oil life.
If you’re looking for a reliable transformer vacuum pump unit, consider exploring Yuneng’s ZJ Series. Their website likely provides detailed specifications, application guides, and contact information to assist you in selecting the most suitable unit for your transformer maintenance needs. Remember, proper vacuum dehydration is essential for maintaining the health and longevity of your transformers.