What is the Automatic Control System of the Transformer Oil Purifier?
The automatic control system of the Transformer Oil Purifier is the core component of the equipment, which ensures the automation and efficient operation of the filtering process. The automatic control system is usually composed of sensors, motors, solenoid valves, control components, and protection components. These components work together to achieve real-time monitoring and automatic adjustment of key parameters such as oil temperature, oil pressure, liquid level, vacuum degree, etc.
The Role of the Automatic Control System
The automatic control system of the Transformer Oil Purifier is a key component to ensure the efficient and stable operation of the equipment. Its main functions include:
- Real-time monitoring and adjustment: The automatic control system monitors key parameters such as oil temperature, oil pressure, liquid level, vacuum degree, etc. in real time through sensors, and automatically adjusts the working status of heating, vacuum, filtration, and other systems according to the preset program to maintain the optimal conditions of the oil treatment process.
- Protect equipment safety: The system has interlocking functions such as overload protection, overpressure alarm shutdown protection, and oil shortage protection. It can take timely measures when abnormal conditions are detected to prevent equipment damage and safety accidents.
- Improve processing efficiency: The automatic control system can automatically adjust the processing parameters such as heating temperature, vacuum degree and filtration speed according to the actual situation of the oil, thereby improving the purification efficiency of the oil and the working efficiency of the equipment.
- Ease of operation: Through automated control, operators do not need to manually adjust multiple operating parameters, which simplifies the operation process, reduces the risk of human operating errors, and reduces the dependence on professional operating skills.
- Data recording and analysis: Modern automatic control systems usually have data recording functions, which can store key data in the oil treatment process, facilitating later data analysis and equipment maintenance decisions.
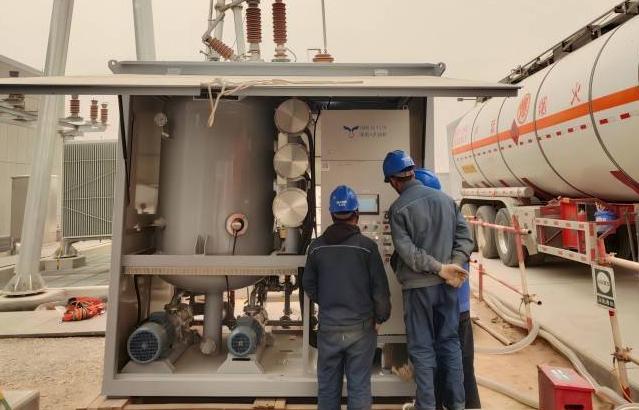
These functions of the automatic control system jointly ensure that the Transformer Oil Purifier can provide stable and reliable oil purification services under various working conditions, which is crucial to the safe operation of the power system.
Key Components of Transformer Oil Purifier Automatic Control System
The automatic control system of a transformer oil purifier is a complex network of interconnected components that work together to ensure efficient and safe operation. Below is a more detailed breakdown of these key components:
1. Programmable Logic Controller (PLC)
The Programmable Logic Controller (PLC) is the central hub of the automatic control system, often referred to as the “brain” of the operation. The PLC is responsible for executing the control logic that governs the operation of the purifier. It continuously processes input data from various sensors, makes decisions based on pre-programmed instructions, and sends commands to actuators and other control elements.
- Processing Inputs: The PLC receives data from sensors that monitor temperature, pressure, flow rates, and other critical parameters. This real-time data allows the PLC to adjust the operation dynamically.
- Executing Control Logic: The control logic within the PLC is programmed to maintain the optimal operating conditions. For example, if the oil temperature exceeds a preset limit, the PLC might trigger a cooling process or shut down the system to prevent damage.
- Flexibility and Customization: PLCs can be reprogrammed to adapt to different operational requirements or to improve the efficiency of the purification process. This flexibility makes them invaluable in handling the complexities of transformer oil purification.
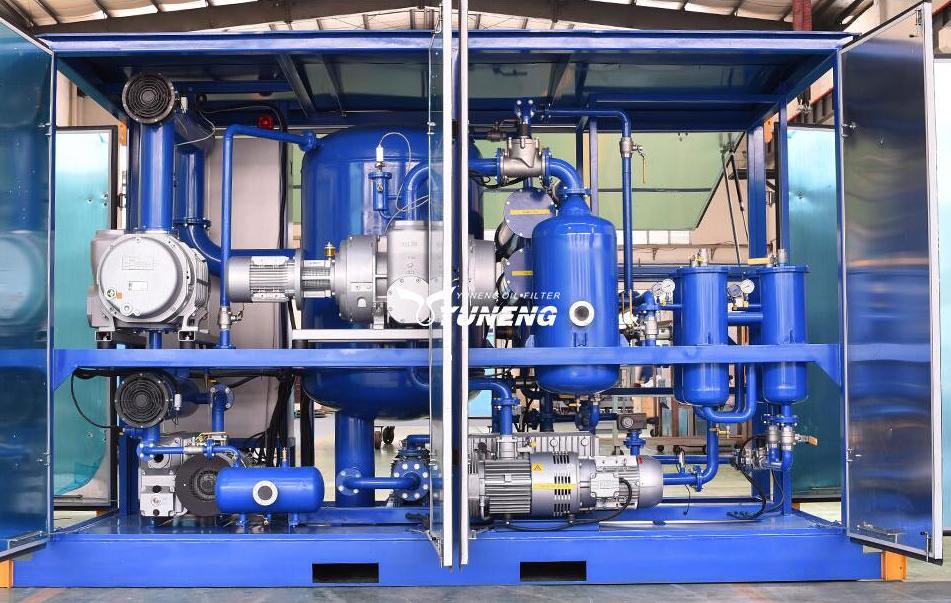
2. Sensors
Sensors continuously monitor the various physical parameters critical to the purification process. Accurate and reliable sensor data is used for the PLC to make informed decisions.
- Temperature Sensors: These sensors monitor the temperature of the oil and the purification equipment. Maintaining the correct temperature is crucial for effective purification and preventing thermal degradation of the oil.
- Pressure Sensors: Pressure sensors ensure that the oil is flowing through the system at the correct pressure. If the pressure is too high or too low, it can indicate a blockage, leak, or malfunction that needs to be addressed.
- Flow Sensors: Flow sensors measure the rate at which oil moves through the system. Consistent flow rates are essential for ensuring that the oil is properly filtered and contaminants are effectively removed.
- Moisture Sensors: In some advanced systems, moisture sensors are used to detect water content in the oil, which is critical because water can significantly degrade the insulating properties of transformer oil.
- Vacuum Sensors: In systems that use vacuum dehydration as part of the purification process, vacuum sensors monitor the vacuum level to ensure optimal removal of moisture and gases.
3. Human-Machine Interface (HMI)
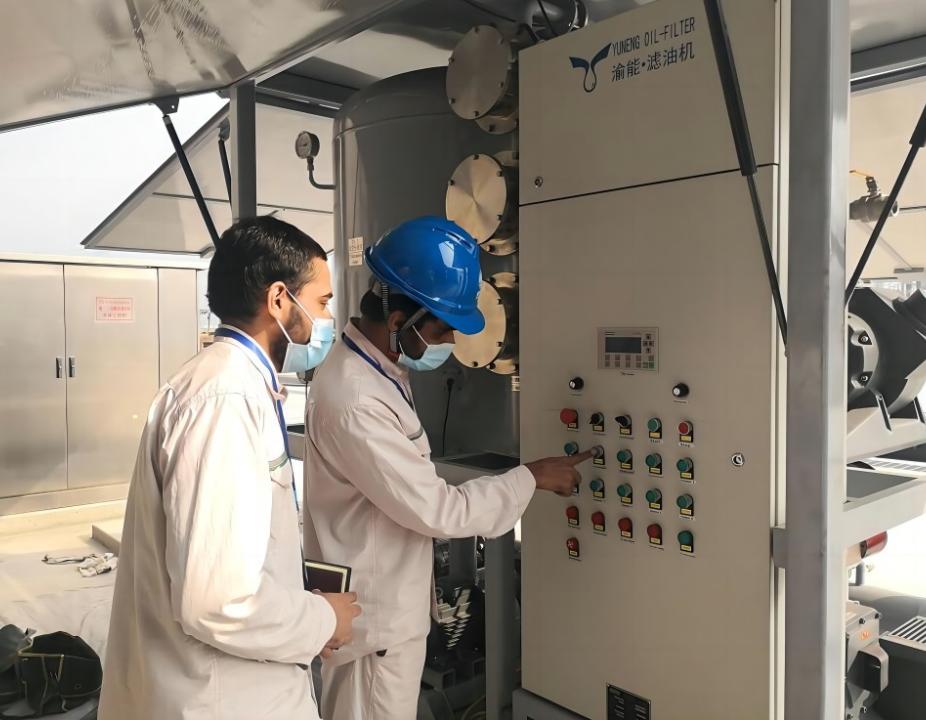
The Human-Machine Interface (HMI) is the component that allows operators to interact with the automatic control system. It provides a visual display of system operations and status, enabling operators to monitor the purification process in real time.
- Display Panel: The HMI typically includes a touchscreen or other display devices that show data such as temperature, pressure, flow rate, and alarms. This makes it easy for operators to see the current state of the system at a glance.
- Control Interface: Through the HMI, operators can manually adjust settings, start or stop the system, and respond to alarms. This interface is critical for both routine operations and troubleshooting.
- Data Logging and Analysis: Many HMIs are equipped with data logging capabilities, recording operational data over time. This data can be analyzed to improve system performance, schedule maintenance, or identify trends that may indicate potential issues.
4. Actuators
Actuators are the components that physically carry out the commands issued by the PLC. They play a vital role in adjusting various aspects of the purification process to ensure it remains within the desired parameters.
- Valves and Pumps: Actuators control valves that regulate the flow of oil, gases, and other fluids within the system. By adjusting these valves, the system can maintain the correct flow rates, pressure, and distribution of the oil during purification. Actuators also control pumps that circulate oil through the purifier. They ensure the oil moves at the required speed and volume to facilitate effective purification.
- Heating Elements: In systems where the oil needs to be heated, actuators regulate the heating elements. They ensure the oil reaches the optimal temperature for purification without exceeding safe limits.
- Vacuum Pumps: In vacuum-type purifiers, actuators control the vacuum pumps that create the necessary vacuum environment for removing gases and moisture from the oil.
- Precision Control: The actuators are designed to provide precise control over the mechanical components, enabling fine-tuning of the purification process to achieve the highest quality results.
The key components of the automatic control system in a transformer oil purifier work together to create a highly efficient and reliable system. The PLC acts as the decision-maker, while sensors provide the necessary data to inform those decisions. The HMI allows operators to monitor and control the system, and actuators execute the physical adjustments needed to maintain optimal purification conditions.
Common Faults of the Automatic Control System and How to Solve
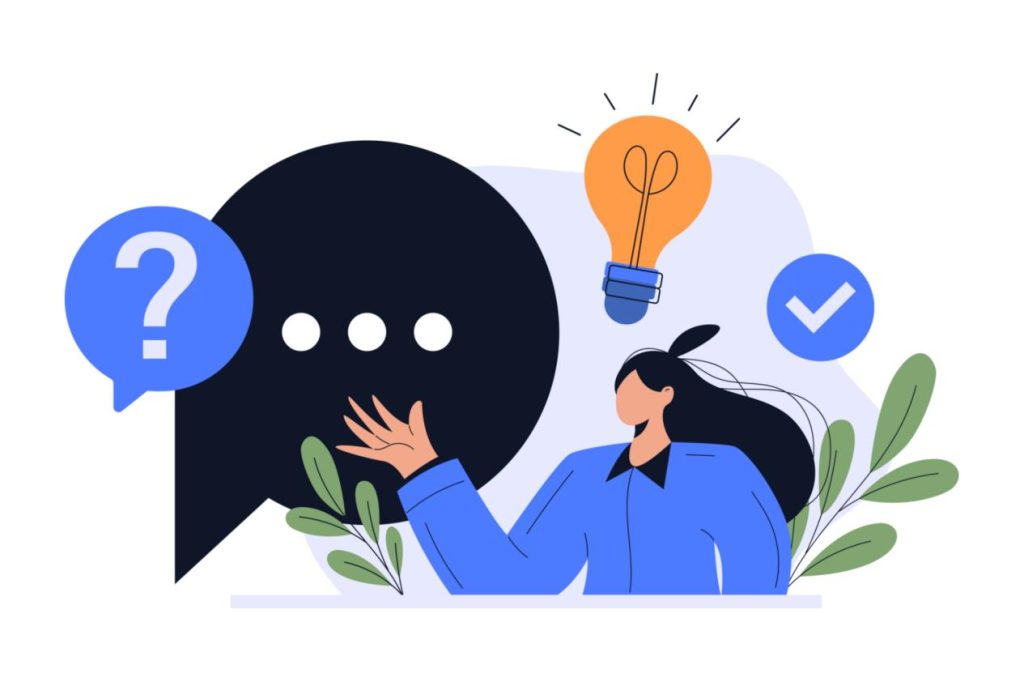
Despite its sophistication, the automatic control system of a transformer oil purifier is not immune to faults. Understanding these common issues and knowing how to resolve them can help maintain optimal operation.
- Sensor Malfunctions: Sensors can fail or provide inaccurate readings due to wear, contamination, or electrical issues. If a sensor is faulty, it should be replaced immediately to ensure accurate monitoring.
- PLC Errors: The PLC may encounter programming errors, communication failures, or hardware faults. Troubleshooting involves checking the PLC’s programming for errors, ensuring proper connections, and, if necessary, resetting or replacing the PLC.
- Actuator Failures: Actuators might fail to respond due to mechanical issues, electrical faults, or control signal problems. Regular maintenance, such as lubricating moving parts and checking electrical connections, can prevent many actuator failures. If an actuator fails, it should be inspected, and faulty components should be repaired or replaced.
- Alarm System Malfunctions: If the alarm system fails to trigger correctly, it may be due to wiring issues, software glitches, or sensor problems. Regular testing of the alarm system and ensuring all connections are secure can help prevent such malfunctions.
- HMI Display Issues: Problems with the HMI, such as unresponsive touch screens or display errors, can hinder operator interaction with the system. Troubleshooting involves checking the HMI for software updates, inspecting connections, and, if necessary, replacing the display unit.
Anyway, the automatic control system is an indispensable component of a transformer oil purifier. By automating various processes and ensuring optimal operation, it contributes to the overall efficiency and reliability of the equipment.
For the YUNENG standard transformer oil purifier, it is not equipped with the PLC. If you need the machine to be automatic, we could also offer the solution for you.